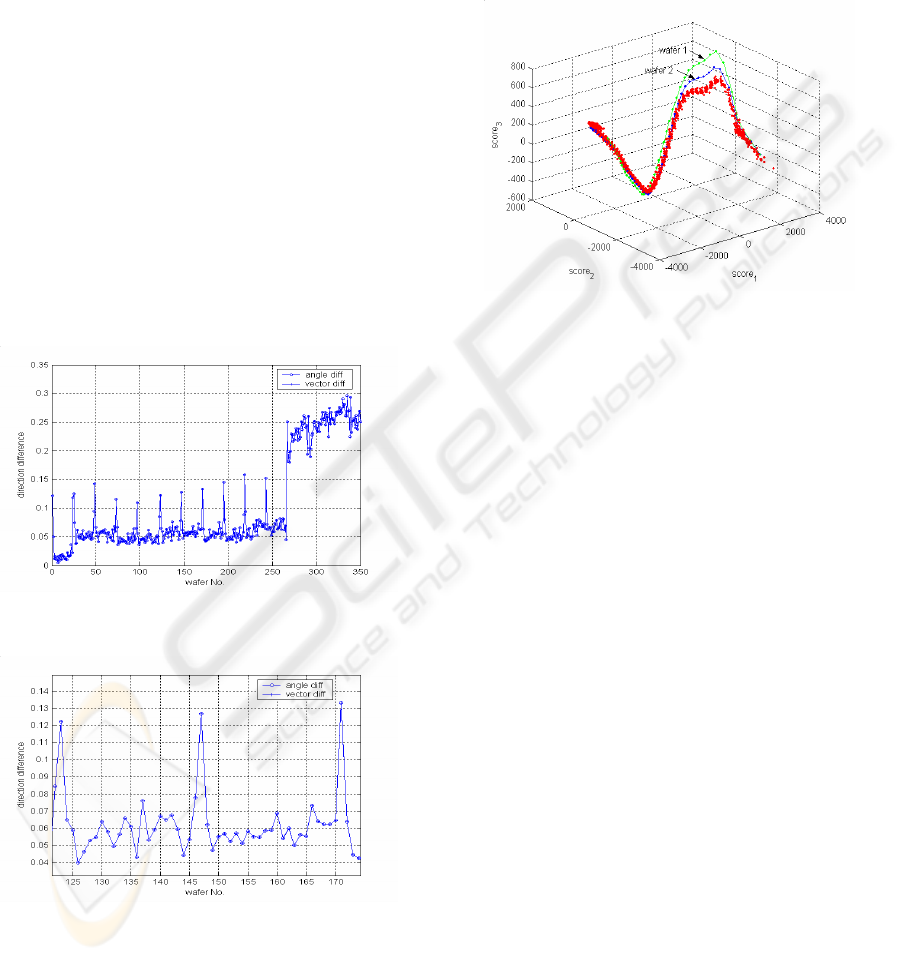
3.3 Wafer-by-wafer Analysis
Here, we simply perform PCA analysis on
individual wafer OES data sets and compare the
patterns across wafers. This allows us to explore the
variation that takes place within lots.
Fig. 7 shows the variation in wafer-PC
1
direction
over all the wafers with lot-PC
1
from lot 1 taken as a
reference. The plasma change at lot 12 observed in
the lot-PC analysis is clearly present in this data as
well, as is a small offset during the first lot.
Large spikes are evident throughout Fig. 7.
These occur at the first wafer in each lot. This is
highlighted in Fig. 8 which shows a zoomed in view
of Fig. 7 covering two lots. These sharp changes
were attributed to changes in the absorption
characteristics of the plasma chamber wall as a
result of a cleaning cycle that is performed between
lots. While a dummy etch cycle is performed
following each clean cycle to counter this affect, it is
clear from Fig. 8 that cleaning still has a significant
impact on plasma characteristics for the first (and to
a lesser extent) the second wafer etch of each lot.
Figure 7: Variation in wafer-PC
1
direction across all
wafers (using lot-PC
1
from lot 1 as a reference).
Figure 8: Variation in wafer-PC
1
direction over two lots.
3.4 Score Patterns
As an illustration of the data compression and
pattern visualisation capabilities of PCA the score
patterns generated by the OES data for all the wafers
in lot 9 are plotted in Fig. 9. Here, the first three lot-
PC loadings from lot 8 were used as a reference PC
model and the PC-scores for each wafer calculated
according to Eq. (4). It is easy to see that the
evolution of the OES data for the first and second
wafers is substantially different from the remaining
wafers, as predicted by the wafer-PC loading
analysis.
Figure 9: The first three scores of all the wafers in lot 9.
4 CONCLUSIONS
In this paper we have demonstrated how monitoring
changes in PC directions can be a useful tool in
revealing patterns contained in the high dimensional
data sets generated from OES analysis of wafer etch
plasma chambers.
ACKNOWLEDGEMENTS
The financial support provided by Enterprise Ireland
is gratefully acknowledged.
REFERENCES
Sugawara, M., 1998. Plasma Etching: Fundamentals and
applications, Oxford University Press, New York.
Splichal, M., Anderson, H., 1987. Application of
Chemometrics to Optical Emission Spectroscopy for
Plasma Monitoring. Proc. SPIE, 2, pp. 189-203.
Jackson, J. E., 1991. A User’s Guide to Principal
Components, Wiley Interscience Press, New York.
Geladi, P., Kowalski, R. B., 1986. Partial least-squares
regression: a tutorial. Analytica Chimica. Acta., 185,
pp.1-17.
Wold, S., Geladi, P., Esbensen, K., Ohman, J., 1987.
Multi-way principal components and PLS analysis.
Journal of Chemometrics, 1, pp. 41-56.
ICINCO 2007 - International Conference on Informatics in Control, Automation and Robotics
364