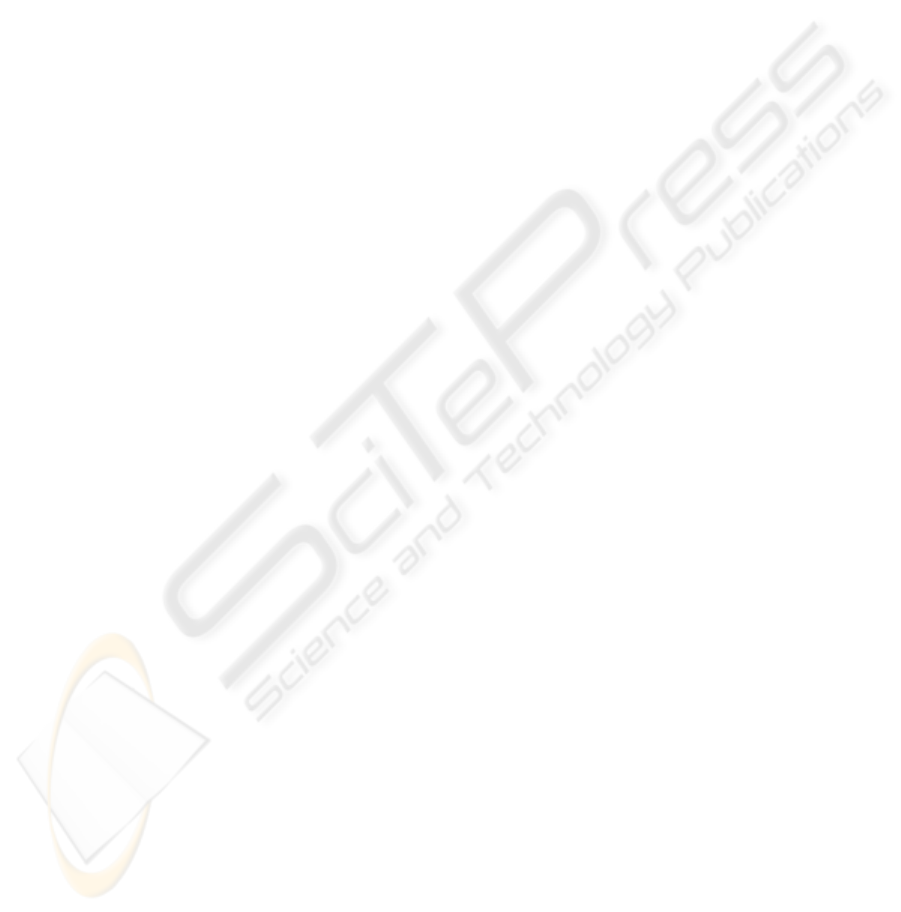
algorithm.
Further investigations on the decentralized
architecture make it possible to extend this local
control strategy to other part of the complex air
conditioning unit.
REFERENCES
Albright, L.D, Gates, R.S, Aravantis, K.G, and Drysdale,
A.E. “Environment Control for Plants on Earth and
Space,” IEEE Control Systems Magazine, pp. 28-47,
October 2001.
Arguello-Serrano, B, Vélez-Reyes, M. “Non linear control
of heting, ventilating, and air conditioning system with
termal load estimation,” IEEE Tranactions on Control
Systems technology, vol. 7, No. 1, January. 1999, pp.
56–63.
Borne, P., Dauphin Tanguy, G., Richard., J.P., Rotella, F.,
Zambrettakis, I. “Modélisation et identification des
processus”. Techniques de l’ingénieur, Technip 1990.
Camacho, E.F and Bordons, C “Model predictive
Control’’ Springer edition, 1998.
Chassériaux, G., Tawegoum , R., and Lelièvre, M.
“Thermal simulation of an air conditioning unit based
on a heating system and humid corrugated pad.” 20
th
International Congress of Refrigeration” – Sidney
(Australia)– sept. Paper code 720, 1990.
Chraibi, A., Makhlouf, S. and Jaffrin, A. “Refroidissement
évaporatif de l'air des serres ”, Journal de Physique,
n°III. Juillet 1995. Dumur,D., Boucher,P., Murphy,
K.M., Déqué, F. ‘‘ On Predictive Controller Design
for Confort Control in Single Residential Housing’’.
ECC’97, juillet 1997.
Clarke, D.W., Mohtadi, C., and Tuffs, P.S., ‘‘Generalized
Predictive Control. Part I. The Basic Algorithm.’’
Automatica, 23(2):137-148, 1987.
Clarke, D.W., Mohtadi, C., and Tuffs, P.S., ‘‘Generalized
Predictive Control. Part II. Extensions and
interpretations’’ Automatica, 23(2):149-160, 1987.
Dan Van Mien, H., and Normad-Cyrot, D. “Non linear
state affine identification methods, application to
electrical power plant”, Automatica, Vol 20, pp. 175-
188, 1984.
Dumur.D,P. Boucher, K.M. Murphy, F. Déqué “On
predictive controller design for comfort control in
single residential housing”, ECC’97-juillet 1997.
Hanan, J.J. “Greenhouse: advanced technology for
protected horticulture.”, Chapter 4, pp. 236-260, 1997.
Hansen, J.M., and , Hogh Schmidt, K., “A computer
controlled chamber system design for greenhouse
microclimatic modelling and control. ” Proc. Int.
Sym.on Plant Production in closed Ecosystems. Acta
Horticulturae, n°440, ISHS, pp. 105-110., 1996.
Jones, P., Jones., J.W., Allen, L.H. and Mishve J.W.
“Dynamic computer control of closed environmental
plant growth chambers, ” Design and Verification.
Transaction of ASAE. (American Society of
Agricultural Engineers), pp. 879-888, 1984.
Lakhdari, Z., Lécluse, Y. and Provost, J., “Dynamic
control of a system with operating point dependent
parameters, application to cryogenic.” In Proc of the
international AMSE conference, Sytems Analysis,
Control & Design, SYS'94, Lyon (France), July, vol.
2, pp. 243 -253. ISBN : 2-909214 -57-5, 1994.
Landau, I.D., Dugard, L. “Commande adaptative aspect
pratiques et théoriques,” , J. Masson, Ed. Paris , 1986,
pp. 1–81.
Landau, I. D., Normand-Cyrot, B., and Montano, A.
“Adaptive control of a class of nonlinear discrete time
systems: application to a heat exchanger,” in Proc.
28
th
Conference on Decision and Control, Los
Angeles, Ca December 1987, pp. 1990-1995.
Ljung, L. “System identification”, Theory for the user,
Prentice Hall, 1999.
M’ssad, M., Chebassier, J. “Commande adaptative des
systèmes,” Techniques de l’ingénieur, vol. 7426, pp.
1–25.
Nybrant, T.G. “Modelling and adaptive control of
concurrent flow driers, ” Computers and Electronics
in Agriculture, 1989, 3, 243-253.
Ramond,G., Dumur, D., Libaux, A., Boucher, P.,‘‘ Direct
adaptive predictive control of an hydro-electric
plant’’, Proceedings 10
th
, Conference on Control
Apllications, pp. 606-611,Mexico,Septembre 2001.
Riadi, R., Tawegoum., R., Rachid, A, Chassériaux, G.
‘‘Modeling and Identification of a Passive Air-
Conditioning Unit using the Operating Dependent
Parameters-Structure’’. Presented CESA-2006:
Computational Engineering in Systems Application,
Beijing, Chine, 4-6 Octobre 2006.
Tawegoum, R., Teixeira, R. and Chassériax., G.
“Simulation of humidity control and temperature
tracking in a growth chamber using a passive air
conditioning unit,” Contol Engineering Practice
Journal, 2006a, 14/8, 853-861.
Tawegoum R., Lecointre B., “A linear parametric model
of an air conditioning unit with operating point
dependent parameters under nearly steady weather
conditions,” 5 th Vienna Symposium on Mathematical
Modelling, Vienna-Austria, February 2006b, Mech,
3.1-3.8.
Tawegoum,, R., Bournet, P.E, Arnould, J., Riadi R., and
Chassériax., G. “Numerical investigation of an air
conditioning unit to manage inside greenhouse air
temperature and relative humidity,” International
Symposium on Greenhouse Cooling, Almeria-Spain,
April 2006c.
Young, P.C. and Lees, M.J. “Simplicity out of complexity
in glasshouse climate modeling, ” in Proc. 2
nd
IFAC/ISHS Workshop on Mathematical an Control
Application in agriculture and Horticulture, 12-15
september 1994, Silsoe, United kingdom, Acta
Horticuturae N°406, pp.15-28.
GPC BASED ON OPERATING POINT DEPENDENT PARAMETERS LINEAR MODEL FOR THERMAL PROCESS
307