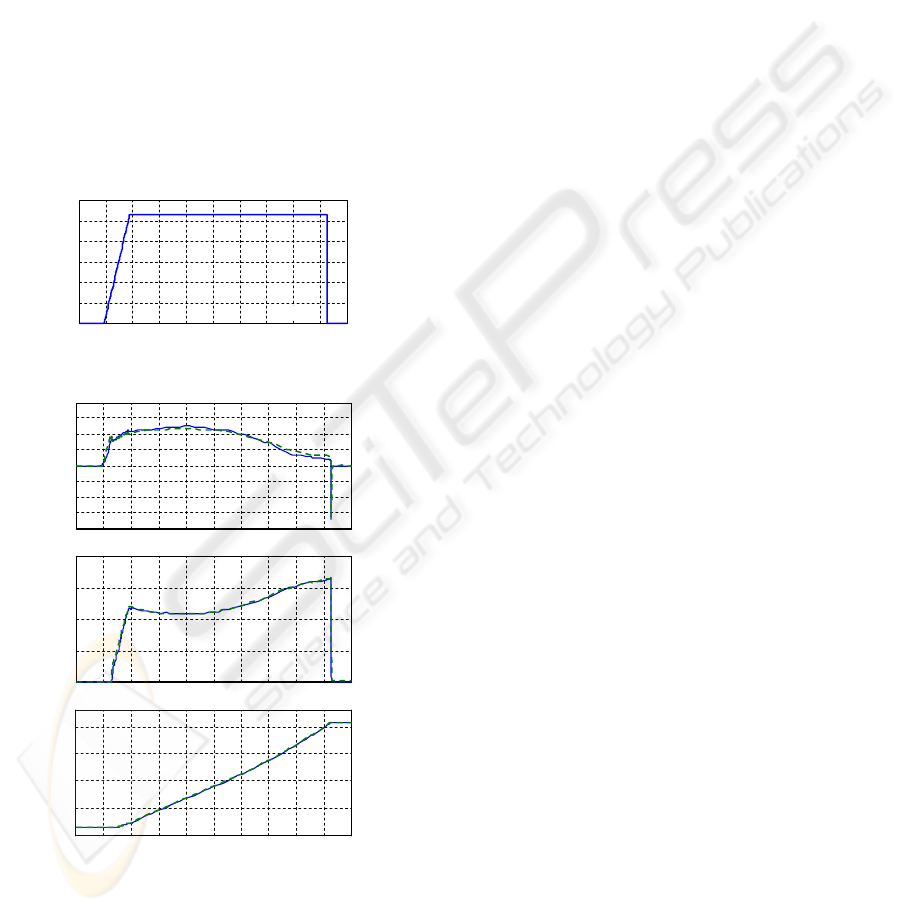
5 EXPERIMENTAL VALIDATION
The validation of the drive chain model has been
done on the pivot axis. The efficiency coefficients
have been identified using experimental measures.
We compare the open loop response of the pivot
joint and the simulation results to a voltage input for
both direct and reverse motion. Figure 9 shows the
applied voltage on the motor pivot axis for direct
motion. Figure 10 shows the experimental results
(dashed curve) of current, velocity and position and
those obtained in simulation (solid curve). We notice
in that the simulation response represents the same
behavior as the real mechanism. In this figure we
distinguish four main phases: the starting phase 24s
to 25s, the motor driving phase 25s to 37.8s, the load
driving phase 37.8s to 4.2s and the braking phase
4.2s to 4.3s.
22 24 26 28 30 32 34 36 38 40 42
0
10
20
30
40
50
60
Time (s)
Motor voltage (V)
Figure 9: Open loop motor command voltage.
22 24 26 28 30 32 34 36 38 40 42
-20
-15
-10
-5
0
5
10
15
20
Current (A)
22 24 26 28 30 32 34 36 38 40 42
0
5
10
15
20
Velocity (deg/sec)
22 24 26 28 30 32 34 36 38 40 42
-100
-50
50
100
130
0
Time (s)
Position (deg)
Figure 10: Direct motion outputs.
By comparing the obtained results, we notice that
the differences are low for direct motion as well as
for reverse motion. Therefore, these results prove
that the used model is able to represent accurately the
irreversibility property of the pivot drive chain.
6 CONCLUSIONS
In this paper, we presented a methodology in order to
model the irreversibility characteristic in
electromechanical drive chains. The proposed
approach uses a macroscopic modeling of the gears,
which are usually the origin of irreversibility in a
drive chains. It consists of creating a state machine
representing different functional states of the gears
and attributing an efficiency coefficient to each
specific state.
The validation of the proposed modeling was
carried out on the Pivot axis of the LCA robot. The
methodology has been tested in particular when the
position trajectory leads to some transitions “motor
driving to load driving” and the obtained results
confirm the correctness of the used model.
The perspectives of this work concern two
research orientations. The first one is the definition
and the study of an automatic procedure to identify
the efficiency coefficient for each state. The second
one is the investigation of the trajectory planning and
the control of robots with irreversible transmissions
when considering state machines for gear’s
modeling.
REFERENCES
Abba G., Chaillet N. (1999) “Robot dynamic modeling
using using a power flow approach with application to
biped locomotion”, Autonomous Robots 6, 1999, pp.
39–52.
Abba G., Sardain P.(2003), “Modélisation des frottements
dans les éléments de transmission d'un axe de robot en
vue de son identification: Friction modelling of a robot
transmission chain with identification in mind”,
Mécanique & Industries, Volume 4, Issue 4, July-
August, pp 391-396
Armstrong B. (1998), “Friction: Experimental
determination, modelling and compensation”, IEEE
International Conference on Robotics and Automation,
Philadelphia, PA, USA, April, vol. 3, pp. 1422–1427.
Dupont P.E.(1990) “Friction modeling in dynamic robot
simulation”, Robotics and Automation, 1990.
Proceedings., IEEE International Conference, pp.
1370-1376 vol.2
Henriot G. (1991) “Traité théorique et pratique des
engrenages”, 5
th
ed. Dunod ed. vol. 1.
Khalil W., Dombre E. (1999) “Modélisation identification
et commande des robots”, 2
nd
ed. Hermes ed.
Pinard M. (2004), “Commande électronique des moteurs
électriques”, Paris Dunod ed. pp 157-163
ICINCO 2007 - International Conference on Informatics in Control, Automation and Robotics
222