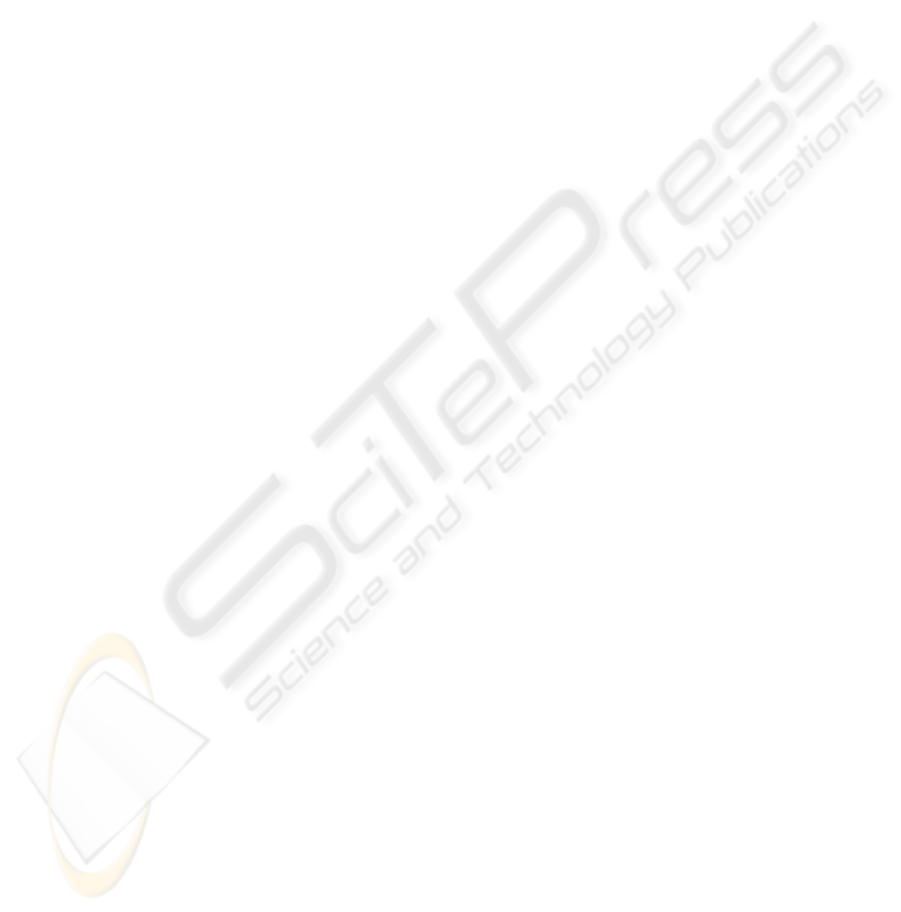
a single PLC. In the model of this system we find : 2
effective contextual components, 7 basic enriched
components, 2 support components and 18 basic
components. The control programs (XML file)
generated are composed of 61 SFCs and 21 I/Os.
Some parts of the XML file are represented on the
figure 13.
<?xml version="1.0" encoding="ISO-8859-1"?>
<K5project version="1.1" path="D:\\StraProj\\testTrMStraton\\">
…..
<variables>
<varGroup name="%IX0" kind="IO">
<var name="%IX0.0=Sensor3_I_D" type="BOOL"/>
<var name="%IX0.1=Sensor23_I_D" type="BOOL"/>
<var name="%IX0.2=Sensor4_I_D" type="BOOL"/>
<programs>
<pou name="Jack3" kind="program" period="1" phase="0" lge="SFC">
<defines name="Jack3"/>
<sourceSFC>
<SFCstep kind="init" dx="1" dy="0" ref="10" name="GS10" next="GT11">
</SFCstep>
<SFCstep kind="init" dx="0" dy="0" ref="0" name="GS0" next="GT1">
</SFCstep>
<SFCstep kind=" init " dx="1" dy="2" ref="12" name="GS12" next="GT13">
<SFCaction kind="default">
<sourceSTIL>Jack3_O_R;</sourceSTIL>
</SFCaction>
Figure 13: Example of parts of the XML file.
All the behaviors have been simulated to check
the provided control. The component with its control
is stored for reusing in a project of a conveyor with
five working areas.
6 CONCLUSION
Components have been introduced, and the
advantages they offer have been pointed out as they
may be very useful to design the control of
conveying systems through the views they gather. A
methodology allowing to generate automatically
control programs (IEC 61131-3 standard compliant)
has also been described. This methodology allows
the reduction of the development costs by
improving, facilitating and systematising the
creation of the control programs. The control
programs are created at a higher level of abstraction:
engineers manipulate models instead of languages of
the IEC 61131-3 standard. The main drawback of
this methodology is that the generated programs will
be bigger than if they were built without using any
methodology.
Transformation model techniques have been
proved to be very powerful to implement code
generation. The methodology has been illustrated
through two examples.
Further works focus on the partitioning of
control programs to obtain a distributed control.
Thus, it will make possible applying the
methodology on a industrial scale system.
REFERENCES
Berruet, P., Coudert, T., Philippe, J.L, 2003, Integration of
dependability aspects in transitic systems, Proc. IEEE-
IMACS CESA 2003, Lille.
Berruet P., Lallican J-L., Rossi A., Philippe J-L., 2005, A
component based approach for the design of FMS
control and supervision, IEEE SMC , Hawaii.
Bézivin, J., Dupé, G., Jouault, F., Pitette, G., Eddine
Rougui, J., 2003, First Experiments with the ATL
Transformation Language: Transforming XSLT into
Xquery, 2ndOOPSLA Workshop on Generative
Techniques in the context of Model Driven
Architecture, Anaheim, California.
Bézivin, J., 2005, On the Unification Power of Models,
Software and SystemModeling, Springer Verlag.
Copalp, 2002, Straton Handbook.
Coudert, T., Berruet, P., Philippe, J.L., 2002, From Design
to Integration of Transitic Systems A Component
Based Approach, Proc. IECON'02, Sevilla, Vol. 1, pp.
2487-2502.
IEC 61131-3, 1993, International Electrotechnical
Commission 61131-3, Programmable controllers - Part
3: programming languages.
Lallican, J.L., Berruet, P., Philippe, J.L, 2005, SimSED: a
tool for modeling and Simulating Transitic Systems,
I3M, CMS 2005, Marseille.
Lallican, J.L., Berruet, P., Rossi, A, Philippe, J.L, 2006,
SimSED: un environnement pour modéliser et simuler
des systèmes transitiques, MOSIM, Rabat.
Millar, J., Mukerji, J., 2001, Model Driven Architecture
(MDA), OMG, ormsc/2001-07-01, Architecture Board
ORMSC1.
OMG, 2002, OMG Meta Object Facility (MOF)
Specification.
Toguyeni, A.K.A., Berruet, P., Craye, E., 2003, Models
and algorithms for failure diagnosis and recovery in
FMS, Int. J. of Flexible Manufacturing Systems, Vol
15, N°1, pp. 57-85.
W3C, Extensible Markup Language : XML,
http://www.w3.org/XML/
ICINCO 2007 - International Conference on Informatics in Control, Automation and Robotics
336