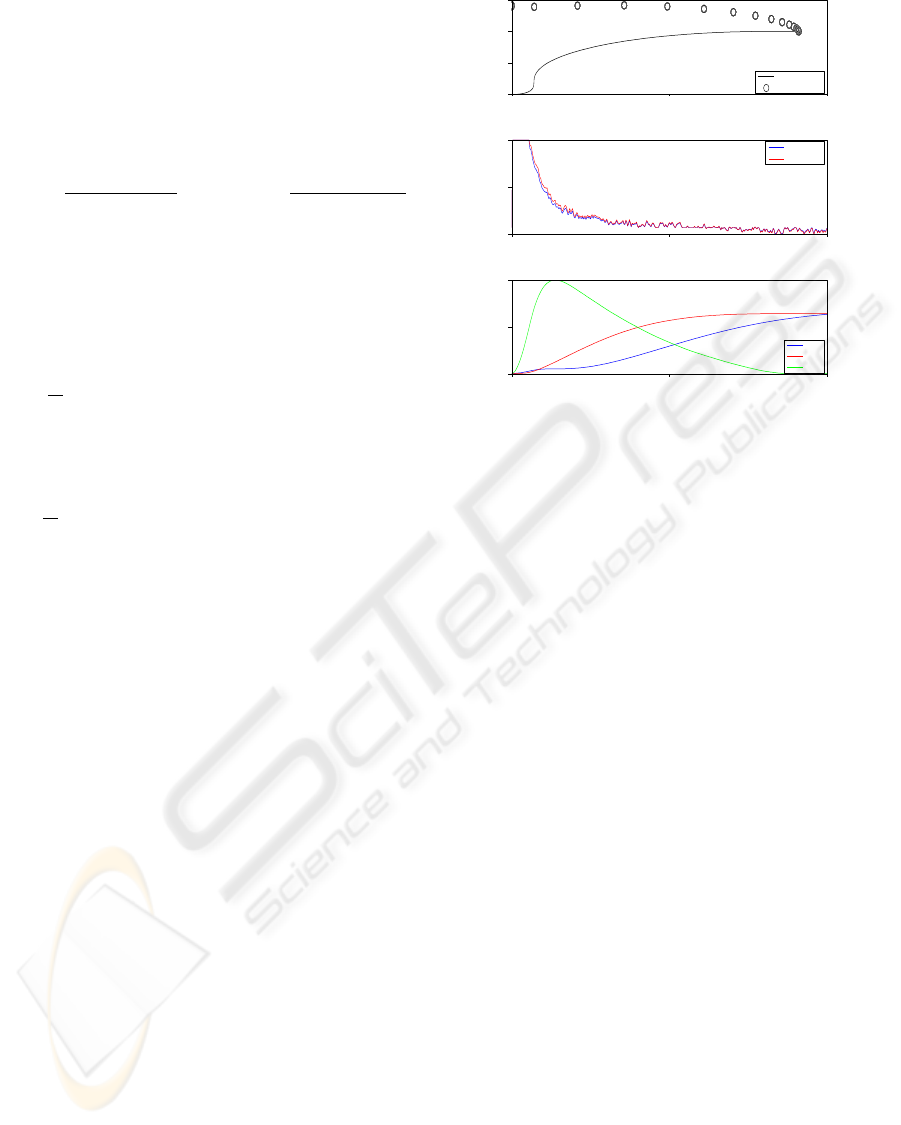
model with a normal distribution random variable of
probability between 1% and 10%. The parameters
used in the simulation are of a realistic robot, that is
not symmetrical.
A controller DMRAC is applied to each plant
(W
S
(s) and W
θ
(s) with relative degree → n
∗
= 2).
Choosing a reference model to each plant, we have
M
S
(s) =
2.25
s
2
+ 3s + 2.25
M
θ
(s) =
100
s
2
+ 20s + 100
and as filters
˙
Q
S1
= −1.5Q
S1
+ 1.5U
S
˙
Q
S2
= −1.5Q
S2
+ 1.5S
˙
Q
θ1
= −10Q
θ1
+ 10U
θ
˙
Q
θ2
= −10Q
θ2
+ 10θ
p
We choose the polynomial L
S
(s) = s + 1.5 to
DMARC
S
with F = 22s + 1, `
S
= 0.7551, α
S
= 0.05
and
Θ
S,nom
= [ −2.0 −6.75 4.5 2.25 ]
T
Θ
S,1
= [ 2.420 13.282 2.657 0.024 ]
T
We choose the polynomial L
θ
(s) = s + 10 to
DMARC
θ
with F = 56s + 1, `
θ
= 0.0051, α
θ
= 0.05
and
Θ
θ,nom
= [ −2.0 −300.0 200.0 9.7 ]
T
Θ
θ,1
= [ 0.073 101.161 175.750 0.1 ]
T
The Fig. 6 shows a simulation result of the closed
loop system. The robot going from the initial point
0 0 0
T
to desired point
1 1 0
T
. When the
robot reaches a circle of 1cm radius with center in de-
sired point, it’s considered that the task was accom-
plished. The controller shows a good transient behav-
ior that means in 3.49s the robot reaches the desired
position without vibrations.
The simulation result is closed to real physical
systems, so it includes the main nonlinearities, a plant
with unknown parameters, bounded disturbances in
the absolute positioning system and in motors driver
system. It uses a sampling interval of 10ms. These
facts did not affect the closed loop system behavior.
In the Fig. 6 is possible identify the functioning
of the DMARC controller. When the error is big a
DMARC operates as VS-MRAC and when the error
is small the DMRAC operates as MRAC.
6 CONCLUSIONS
In this paper a controller that decouples multivariable
system into two monovariable systems was proposed.
For each monovariable system an adaptive robust con-
troller is applied to get desired responses.
The closed loop system with the proposed con-
troller presented a good transient response and robust-
ness to disturbances and errors in the absolute posi-
tioning system and in driver system.
−0.00 0.55 1.10
0.0
0.5
1.0
1.5
Robot Trajectory
x
y
Trajectory
Reference Point
0.00 1.75 3.49
−0.82
4.59
10.00
Motors Signals
t
x
Right Motor
Left Motor
0.00 1.75 3.49
−0.02
0.77
1.56
X,Y,Angle Evolution
t
X
Y
Angle
Figure 6: Robot signals (control signal and output plant).
REFERENCES
Araujo, A. D. and Hsu, L. (1990). Further developments in
variable structure adaptive control based only on in-
put/output measurements. volume 4, pages 293–298.
11th IFAC World Congress.
Chang, C., Huang, C., and Fu, L. (2004). Adaptive track-
ing control of a wheeled mobile robot via uncalibrated
camera system. volume 6, pages 5404–5410. IEEE
International Conference on Systems, Man and Cy-
bernetics.
Cunha, C. D. and Araujo, A. D. (2004). A dual-mode adap-
tive robust controller for plants with arbitrary relative
degree. Proceedings of the 8th International Work-
shop on Variable Structure Systems, Spain.
Dixon, W. E., Dawson, D. M., Zergeroglu, E., and Behal,
A. (2001). Adaptive tracking control of a wheeled
mobile robot via uncalibrated camera system. IEEE
Transactiond on on Systems, Man and Cybernetics,
31(3):341–352.
Hirschorn, R. M. (1979). Invertibility of multivariable non-
linear control systems. IEEE Transactions on Auto-
matic Control, AC-24:855–865.
Hsu, L. and Costa, R. R. (1989). Variable structure model
reference adaptive control using only input and out-
put measurements - part 1. International Journal of
Control, 49(02):399–416.
Laura, T. L., Cerqueira, J. J. F., Paim, C. C., Pomlio, J. A.,
and Madrid, M. K. (2006). Modelo dinmico da es-
trutura de base de robs mveis com incluso de no lin-
earidades - o desenvolvimento do modelo. volume 1,
pages 2879–2884. Anais do XVI Congresso Brasileiro
de Automtica, 2006.
ICINCO 2007 - International Conference on Informatics in Control, Automation and Robotics
44