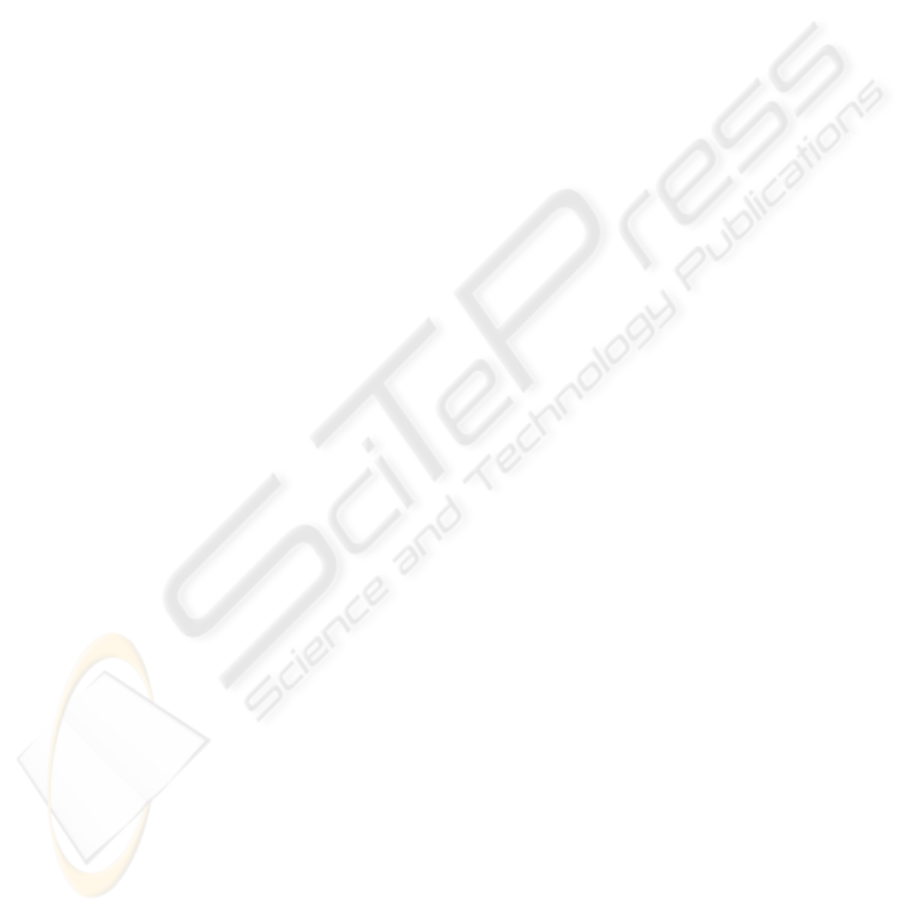
VISUAL ALIGNMENT ROBOT SYSTEM: KINEMATICS, PATTERN
RECOGNITION, AND CONTROL
SangJoo Kwon and Chansik Park
School of Aerospace and Mechanical Engineering, Korea Aerospace University, Goyang-city, 412-791, Korea
Keywords:
Visual alignment, robotics, parallel mechanism, precision control, pattern recognition.
Abstract:
The visual alignment robot system for display and semiconductor fabrication process largely consists of multi-
axes precision stage and vision peripherals. One of the central issues in a display or semiconductor mass pro-
duction line is how to reduce the overall tact time by making a progress in the alignment technology between
the mask and panel. In this paper, we suggest the kinematics of the 4PPR parallel alignment mechanism with
four limbs unlike usual three limb cases and an effective pattern recognition algorithm for alignment mark
recognition. The inverse kinematic solution determines the moving distances of joint actuators for an iden-
tified mask-panel misalignment. Also, the proposed alignment mark detection method enables considerable
reduction in computation time compared with well-known pattern matching algorithms.
1 INTRODUCTION
In the flat panel display and semiconductor industry,
the alignment process between mask and panel is con-
sidered as a core technology which determines the
quality of products and the productivity of a manu-
facturing line. As the sizes of panel and mask in the
next generation products increases but the dot pitch
becomes smaller, the alignment systems must fulfill
more strict requirements in load capacity and con-
trol precision. The alignment system largely has two
subsystems. One is the multi-axes robotic stage to
move the mask in a desired location with acceptable
alignment errors and the other one is the vision sys-
tem to recognize the alignment marks printed in mask
and panel surfaces. In a display or semiconductor
production line, the alignment systems are laid out
in series as subsystems of pre-processing and post-
processing equipments such as evaporation, lithogra-
phy, and joining processes.
The alignment stage has at least three active joints
to determine planar three degrees of freedom align-
ment motions. It usually adopts a parallel mecha-
nism, specifically when it is used for display panel
alignment, since it has the advantage of high stiffness
and high load capacity. In this paper, we are to dis-
cuss the inverse kinematics of the parallel stage which
has four prismatic-prismatic-revolute (4PPR) limbs
where all the base revolute joints are active ones. For
the same-sized moving platform, the four-limb mech-
anism brings higher stiffness and load capacity com-
paring with normal three-limb stages but inevitably it
leads to a more difficult control problem. Although
a commercial alignment stage with four driving axes
was announced in (Hephaist Ltd., 2004), reports on
the kinematics and control can be rarely found.
The next issue is the vision algorithm toextract the
position of alignment marks. In many machine vision
systems, the normalized gray-scale correlation (NGC)
method (Manickam et al., 2000) has been used as
a representative template matching algorithm. How-
ever, it requires long computation time since all pix-
els in the template image are compared in the match-
ing process. An alternative to reduce the computation
time is the point correlation (PC) algorithm (Kratten-
thaler et al., 1994) but it is still weak to the rotation of
object and the change of illumination condition. As
an another, the edge-based point correlation (Kang
and Lho, 2003) was proposed to mitigate the effect
of illumination change. In fact, commercial vision
libraries, e.g., (Cognex Ltd., 2004), are adopted in
many visual alignment systems considering the sta-
bility of the vision algorithm. However, they are com-
putationally inefficient from the point of view that
they have overspec for the monotonous vision en-
vironment of alignment systems (e.g., simple mark
shape, fine light, and uniform background). In this
paper, by incorporating the binarization and labeling
algorithm (Gonzalez and Wood, 2002) together and
designing a geometric template matching scheme in-
stead of the general methods: NGC (Manickam et al.,
2000) and PC (Krattenthaler et al., 1994), an efficient
36
Kwon S. and Park C. (2007).
VISUAL ALIGNMENT ROBOT SYSTEM: KINEMATICS, PATTERN RECOGNITION, AND CONTROL.
In Proceedings of the Fourth International Conference on Informatics in Control, Automation and Robotics, pages 36-43
DOI: 10.5220/0001632000360043
Copyright
c
SciTePress