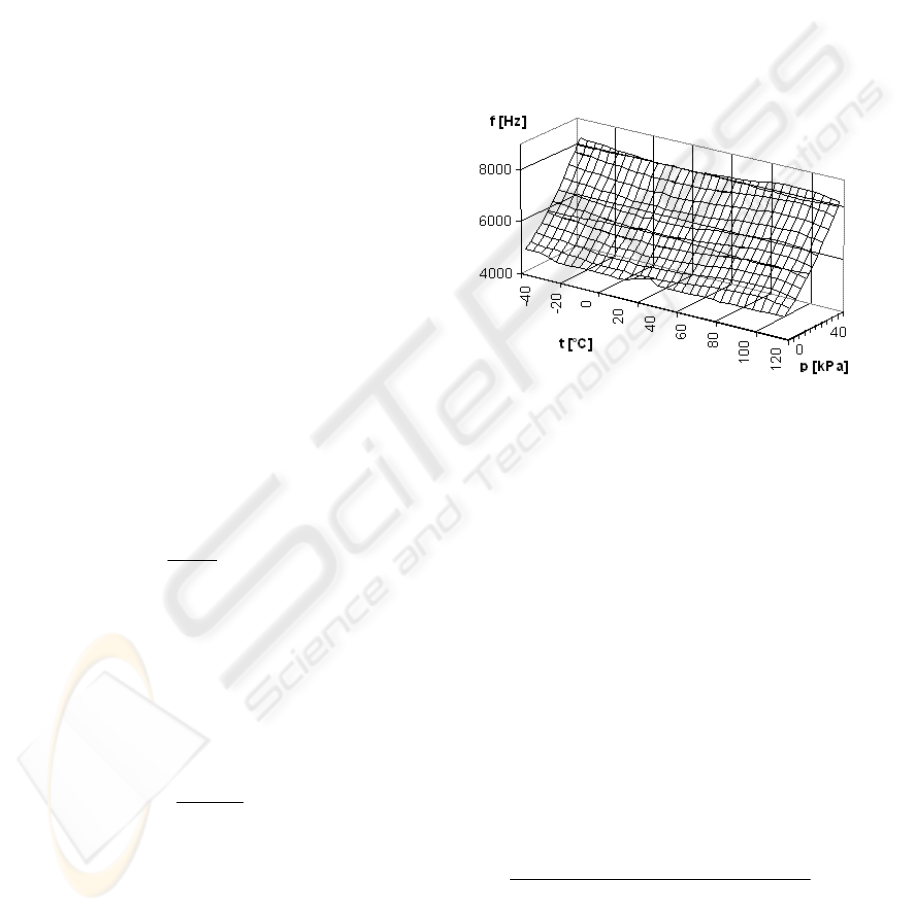
be used because it leds to increased power
consumption.
2.3 Measurement Principle
The measurement is based on counting of 255
periods of the measured signal. Microcontroller
system clock is used as a sampling signal. Quiescent
frequency of the oscillators is set to 4.5 kHz. The
microcontroller counts 255 periods in 56 ms. Thus
total measurement time is 112 ms. These
calculations are not correct because the pair of
oscillators are not really identical, but even if real
measurement can be faster or slower, complete
measurement time is constant. This attribute is given
by design of the differential pressure sensor. The
measurement algorithm is implemented in the
microcontroller as follows: Counter/Timer0 (C/T0)
is configured as an 8-bit counter (it means 255
period of input signal). The Counter/Timer1 (C/T1)
runs as a 16-bit timer with 125 kHz clock before the
counting is allowed. The low system frequency of
the microcontroller significantly reduces power
consumption [3]. But minimal 1 MHz of the system
frequency is needed to suppose desired measurement
accuracy. Due to when 253 periods are counted the
microcontroller is over-clocked to 2 MHz. The value
in C/T1 is stored for next processing and C/T1 is
cleared. When the 255 periods are counted, the
interrupt is called and value in C/T1 is red. This
value reflects the measured capacity. With no
pressure the counter counts approximately 112 000
pulses from each oscillator. By using equation
2log
log
x
n =
,
(2)
where x represents numbers of levels and n is a bit
resolution, we can calculate that we can measure
oscillator frequencies with more than 16-bit
resolution.
This accuracy is adequate. For effective
processing of the measured values, the working
variable A(p) is evaluated. Variable A(p) represents
uncorrected digital pressure
21
21
)(
ff
ff
pA
+
= ,
(3)
where f
1
and f
2
are measured frequencies of
oscillator output signals. At next stage the working
variable A(p) is calibrated using non-linear
corrections by hi-order polynomial. The calibration
provides linear response of the output value to the
pressure. The calibrated output value presents the
digital pressure and is set in specified units (bar,
kPa, etc.). After all linearization and calibration
processes the value is sent via SPI to the second
microcontroller which provides transmitting into the
current loop.
2.4 Corrections
Two corrections are calculated by the embedded
microcontroller. At first, the linearization, offset
calibration and gain correction are calculated. Next,
the temperature dependence of the measuring
electronics is compensated. Fig. 3 shows enumerated
dependencies in a 3D graph.
Figure 3: The oscillator output frequency dependence on
pressure and temperature.
There are a few calibration methods for example
lookup tables but these methods are usually of a high
cost and time consuming [2]. The polynomial of
fifth to eighth order is used for calibration of the
variable A(p). The basic form of the polynomial is
n
n
xaxaxaay ++++= ..
2
210
(4)
The Lagrange’s polynomial is used for calculation of
the calibration constants. The Lagrange’s
polynomial is the lowest order polynomial which
goes through specified values [4]. The Lagrange’s
polynomial can be calculated by
∑
=
n
i
ii
xf
1
)(
λ
(5)
where
)
)
)( ) ( )
()( )( )( )( )
niiiiiii
nii
i
xxxxxxxxxx
xxxxxxxxxx
−−−−−
−−−−−
=
+−
+−
......
......
1121
1121
λ
.
(6)
The calibration data is stored in FRAM embedded
on the oscillator board.
ICINCO 2007 - International Conference on Informatics in Control, Automation and Robotics
246