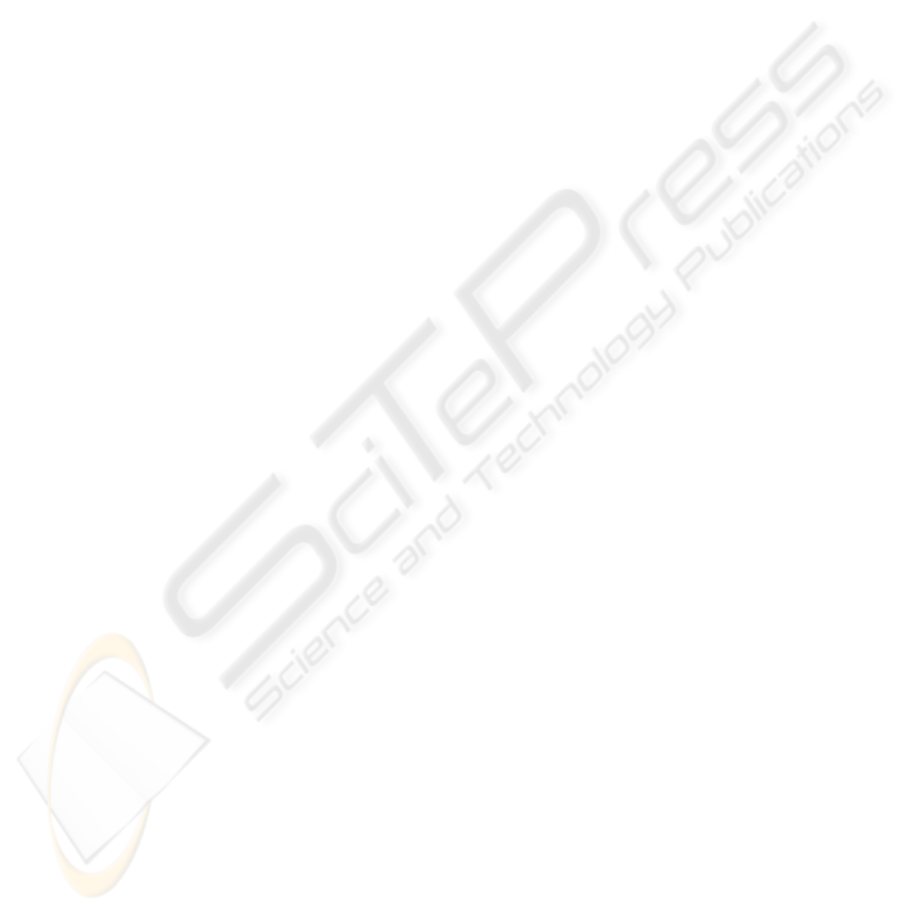
of different methodologies in a multi-formalism ap-
proach to modelling supported by an appropriate sim-
ulation environment.
In mechatronic applications, the Bond Graphs in-
troduced by (Paynter, 1960) provide a continuous sys-
tem modelling approach, oriented to a class of inter-
connected and completely different systems and tar-
geted to many user groups. Bond Graphs are very use-
ful in analysing and designing components built from
different energetic media and can represent dynamical
systems at higher level of abstraction than differen-
tial equations (van Amerongen and Breedveld, 2003),
(Ferretti et al., 2004).
In this paper, we referred to AMESim
r
(Ad-
vanced Modelling Environment for performing Sim-
ulations of engineering systems) (IMAGINE S.A.,
2004) a Bond Graph-based, multi-domain mod-
elling/optimization tool for the virtual prototyping
of the physical/geometrical characteristics of a Com-
pressed Natural Gas (CNG) injection system. In a first
step, we used this tool to obtain a virtual prototype, as
similar as possible to the actual final hardware. Then,
with reference to this prototype, we also determined
a reduced order model in form of transfer function
and/or state space model, more suitable for analytical
(or empirical) tuning of the pressure controller of the
CNG injection systems. Using the virtual prototype
in these early design stages enabled the evaluation of
the influence of the geometrical/physical alternatives
on the reduced model used for the controller tuning.
Then, based on this reduced model, the controller set-
tings were designed and adjusted in accordance with
the early stages of the mechanical design process. Fi-
nally, the detailed physical/geometric model of the
mechanical parts, created by the AMESim package,
was exported ad used as a module in a simulation
program, which enabled the evaluation of the con-
troller performance in the closed-loop system. In
other words, the detailed simulation model surrogated
for a real hardware.
2 THE INTEGRATED DESIGN
APPROACH
In this paper, we consider the opportunity of integrat-
ing different models, at different level of details, and
different design tools, to optimize the design of the
mechanical and control systems as a whole. To sum
up, the integrated design can take advantage of pecu-
liarities of different specific software packages. The
effectiveness of the approach is illustrated by means
of a case study, the pressure control of a CNG injec-
tion system for internal combustion engines, which
represents a benchmark for the evaluation of perfor-
mances of the approach. Experimental results give a
feedback of benefits of the integration of the mechan-
ical and control subsystems design.
The integrated design involves the development
of a virtual prototype of the considered system using
an advanced modelling tool (AMESim in this paper),
which is employed for the analysis of the system per-
formances during the different developing steps. Ac-
tually, the virtual prototype could be assumed as a re-
liable model of the real system. Further, a low order
analytical model of the real system can be developed
to simplify the controller design. Since AMESim can
represent physical phenomena at different level of de-
tails, it is exploited to verify assumptions in build-
ing the analytical model. Then, the control system
is designed using a specific software package, i.e.
MATLAB/Simulink
r
, and tested on the virtual pro-
totype. The virtual prototype allows to perform safer,
less expensive, and more reliable tests than using the
real system.
3 APPLICATION EXAMPLE
We consider a system composed of the following el-
ements (Fig. 1): a fuel tank, storing high pressure
gas, a mechanical pressure reducer, a solenoid valve
and the fuel metering system, consisting of a com-
mon rail and four electro-injectors. Two different con-
figurations were compared for implementation, with
different arrangements of the solenoid valve affecting
system performances (i.e. cascade connection, figure
1(a), and parallel connection, Fig.1(b), respectively).
Detailed AMESim models were developed for each
of them, providing critical information for the final
choice. Few details illustrate the injection operation
for both layouts.
With reference to Fig. 1(a), the pressure reducer
receives fuel from the tank at a pressure in the range
between 200 and 20 bars and reduces it to a value of
about 10 bar. Then the solenoid valve suitably reg-
ulates the gas flow towards the common rail to con-
trol pressure level and to damp oscillations due to in-
jections. Finally, the electronically controlled injec-
tors send the gas to the intake manifold for obtain-
ing the proper fuel air mixture. The injection flow
only depends on rail pressure and injection timings,
which are precisely driven by the Electronic Control
Unit (ECU). The variable inflow section of the pres-
sure reducer is varied by the axial displacement of a
spherical shutter coupled with a moving piston. Pis-
ton and shutter dynamics are affected by the applied
forces: gas pressure in a main chamber acts on the
ICINCO 2007 - International Conference on Informatics in Control, Automation and Robotics
12