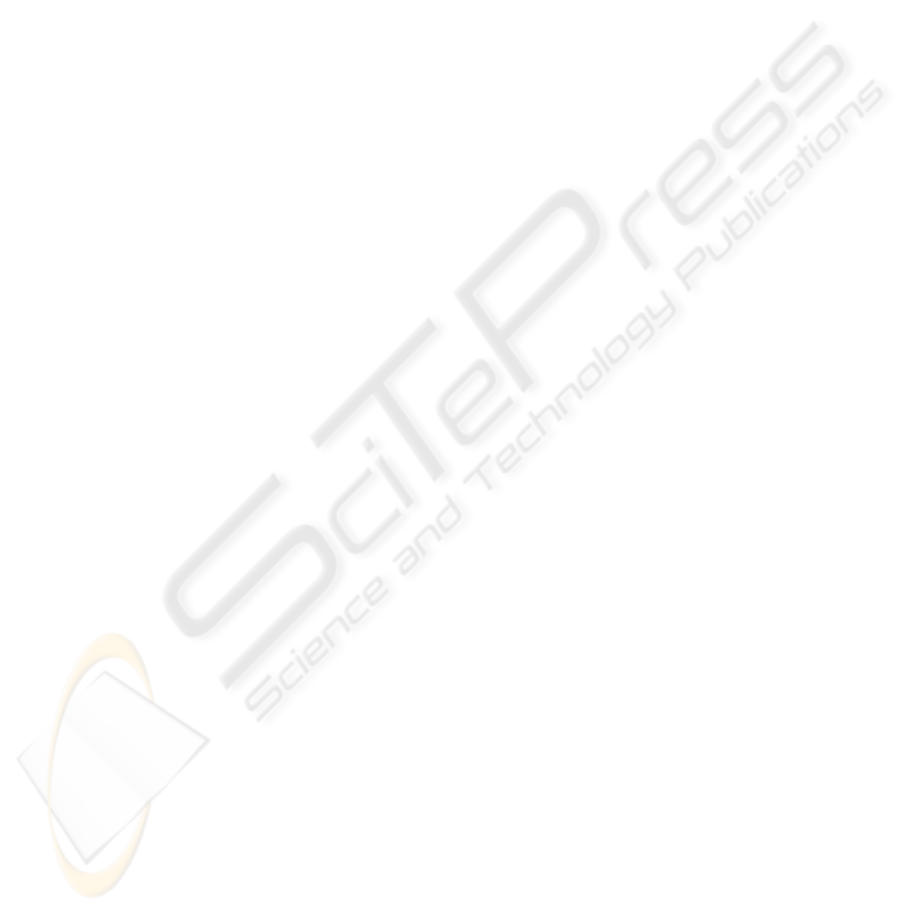
current match respectively 70 Hz and 85 Hz for –3
dB and phase lag 90° for flow rates Qd3 and Qg3 of
600 l/min.
The frequency response for 100 % of the
nominal value of the current obtained from the
model gives a cut-off frequency of 70 Hz
corresponding to a gain of –3 dB and a frequency of
73 Hz for a phase lag of 90°. One observes that the
results obtained for the servo valves corresponding
to the second and third stages from the model and
those supplied by the manufacturer are close.
Nevertheless, one can note that a difference between
the curves amplitude from the manufacturer and
those obtained from the model. Indeed, the
manufacturer curves show an under damping
probably caused by the implementation of the
corrector in the system whereas we have performed
the modeling without corrections in loop control.
5 CONCLUSION
In our work, one can note that the servo valve is the
limiting element of the servo valve + jack system.
The flow rate values (20 l/min and 600 l/min
provided by the second and the third stage
respectively), like the bandwidth values of the
driving servo valve corresponding to the second
stage and those of the amplification stage e.g. the
third stage, obtained from the model and supplied by
manufacturer are rather similar. These results
suggest that the estimated values, which cannot be
measured, such as the gap xo between the nozzle and
the pallet, the inertia J and the viscous friction
coefficients of the pallet Φ, the friction coefficients
of the slides Ψ
2,
Ψ
3
and the flow rate gains Kbuse, K1,
Kf
2
, K2, Kf
3
, are fairly close to the physical values of
the type 550 and 1160 Hydraustar servo valve. We
have shown that the nonlinear model presented in
this work have allowed us the accurate simulation of
the nonlinear behavior of three stage servo valves
between the current input and the flow rate output.
This model allows the taking into account of the
pressure into the jack chambers as a function of the
forced stress. Hence with this model is possible to
computed the dynamic and static behavior, the latter
corresponds to the short circuit generated by jack
stoppers.
At this stage, the interfacing with the
SimMecanics software, by introducing as input this
corresponding to the effort between two ”bodies”,
the quantity (P1-P2)Sp (Sp: useful piston surface),
will provide as output from the software, the speed
and the relative position of both bodies.
ACKNOWLEDGEMENTS
Special thanks go to Mr. Terrade (Hydraustar
company) for supplying technical support.
REFERENCES
Faisandier, J., 1999. Mécanismes hydrauliques et
pneumatiques , 8
e
édition, Paris, Dunod.
Mare, J.C., 2002, Actionneurs Hydrauliques, Commande .
Techniques de l’ingénieurs, traité l’informatique
industrielle.S731.
Thayer, W.J., 1965, Transfer functions for moog servo
valves , Technical bulletin I03, MOOG INC. Springer-
Verlag.
Guillon, M., 1961, Etude et détermination des systèmes
hydrauliques, Paris, Dunod.
Pommier, V., Lanusse P., Oustaloup A., 2000, Commande
CRONE d'un actionneur hydraulique. In Journée
Franco-Tunisiennes, Monastir, Tunisie.
ICINCO 2007 - International Conference on Informatics in Control, Automation and Robotics
64