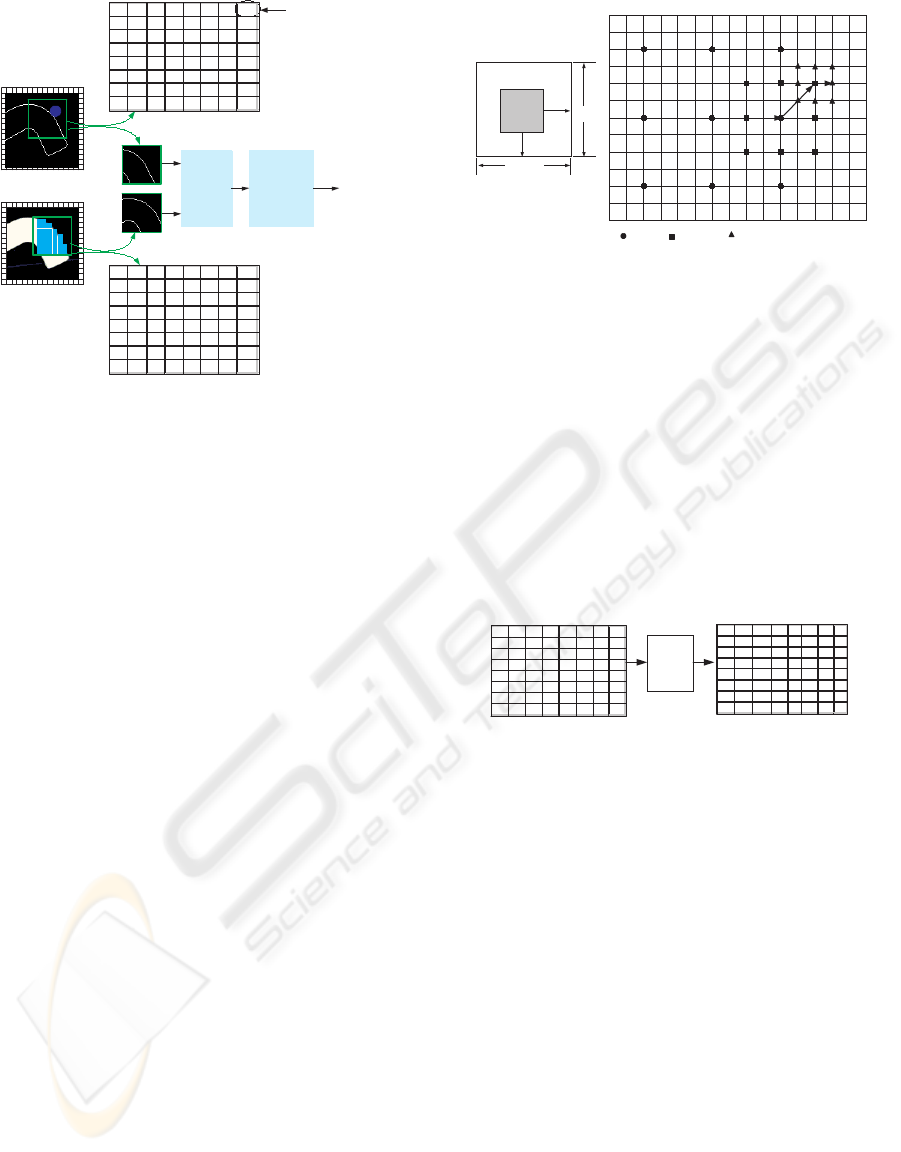
Reference
Target
Mean
Absolute
Difference
(MAD)
Image
Difference
Coding (IDC)
2
)00011000(24
Pixels valaues (0~255)
12 14 27 35 19 14 24 10
9 4 45 28 49 20 24 30
1 35 15 42 49 20 24 42
16 30 17 44 35 28 28 21
20 26 13 14 16 25 35 14
26 20 18 18 17 17 15 21
40 49 19 35 28 15 15 10
20 18 19 21 18 44 10 5
42 14 27 35 49 44 30 24
49 49 35 28 49 20 24 30
21 35 35 42 42 28 28 42
56 70 77 84 95 28 28 21
70 26 13 14 16 95 35 14
26 20 18 18 17 17 35 21
40 49 49 35 28 35 35 35
20 18 24 21 18 84 21 21
Pixels valaues (0~255)
Bitstream output
Figure 7: Block matching algorithm.
search area. For our application the search area is
specified by dx = (−p, p) and dy = (−p, p) where
p = 6 and N = 16.
The matching of a macroblock with another is
based on the output of a cost function (9). The mac-
roblock that results in the least cost is the one that
matches the closest to current macroblock, Figure 7.
For each fingertip that gets in touch with the object,
the tactile features are matched to those of visual fea-
tures inside a predefined searching area. A motion
vector is then applied to search the features correspon-
dence between blocks in the target frame and those in
the reference frame. Figure 8 illustrates the searching
method that evaluates the MAD cost function within
the search area. Many other search methods can be
found in (Furht, 1995).
5.3 Image Difference Coding
In order to control the grasping position, the result of
the matching algorithm can be defined as error posi-
tion or that so called error grasp, is then calculated
using the following expression:
G
e
(i, j) = V(i, j) − S(i+ dx, j + dy) (10)
Since we want to guide the robot hand towards
these grasping references G
ref
, the solution consists
of reducing the grasp error G
e
by moving the tactile
sensors towards the set of corresponding positions
of grasping references. The cost of a solution is
expressed as the total sum of contact displacements
over the surface of the object from an initial contact
configuration. If the result of matching is outside a
given margin, then the grasp controller should launch
a new measurement via joint angle and position
First step
second step
third step
v
Searching vector
v
Searching area (2p+N)x(2p+N)
Current
MacroBlock
16
16
Searching area (2p+N)x(2p+N)
p=6
p=6
2p + N
2p + N
Figure 8: Searching area.
sensors.
The result of block matching algorithm (see
Figure 8) is a two-dimensional vector called motion
vector, v(l, m). The Image Difference Coding (IDC)
processes these measurements and produces as output
a vector image containing the parameters of grasping
positions, which are compressed in a suitable format
to reduce the data transmission bandwidth. The
digital cosine transform (DCT) is used due to its
capability of removing spatial redundancy to achieve
low bit rates.
42 28 20 35 49 24 24 30
49 49 35 28 49 20 24 30
21 35 35 42 42 28 28 42
56 70 77 84 95 28 28 21
70 12 33 47 61 95 35 14
26 20 18 18 75 75 35 21
40 49 49 35 28 35 35 35
20 18 45 21 82 84 21 21
DCT
70 24 -28 -4 -2 -10 -1 0
-53 -35 43 13 7 13 1 3
23 9 -10 -8 -7 -6 5 -3
6 2 -2 8 2 -1 0 -1
-10 -2 -1 -12 2 1 -1 4
3 0 0 11 -4 -1 5 6
-3 -5 -5 -4 3 2 -3 5
3 0 4 5 1 2 1 0
),( mlv ),( vug
Figure 9: DCT Image compression.
The DCT transforms each 8x8 block of greyscale
values into a block of 8x8 spectral frequency coeffi-
cients. The energy tends to be concentrated into few
significant coefficients. Other coefficients are close to
zero and insignificant (see Figure 9).
Next step of IDC is to compress the frequency do-
main, by not transmitting (or not coding) the close-
zero coefficient (insignificant coefficients) and by
quantizing and coding the remaining coefficients.
6 EXPERIMENTAL RESULTS
Figure 10 illustrates our experimental system which
consists of a anthropomorphic robot hand equipped
with a tactile array sensor on each fingertip and a
stereo vision system. The spacial resolution of the
tactile sensor has 256 (16x16) sensing cells over an
area of 100 square millimeter. The sensory data pro-
cessing were performed using MCAGUI and SVS
tools for tactile and vision data, respectively, devel-
ICINCO 2007 - International Conference on Informatics in Control, Automation and Robotics
122