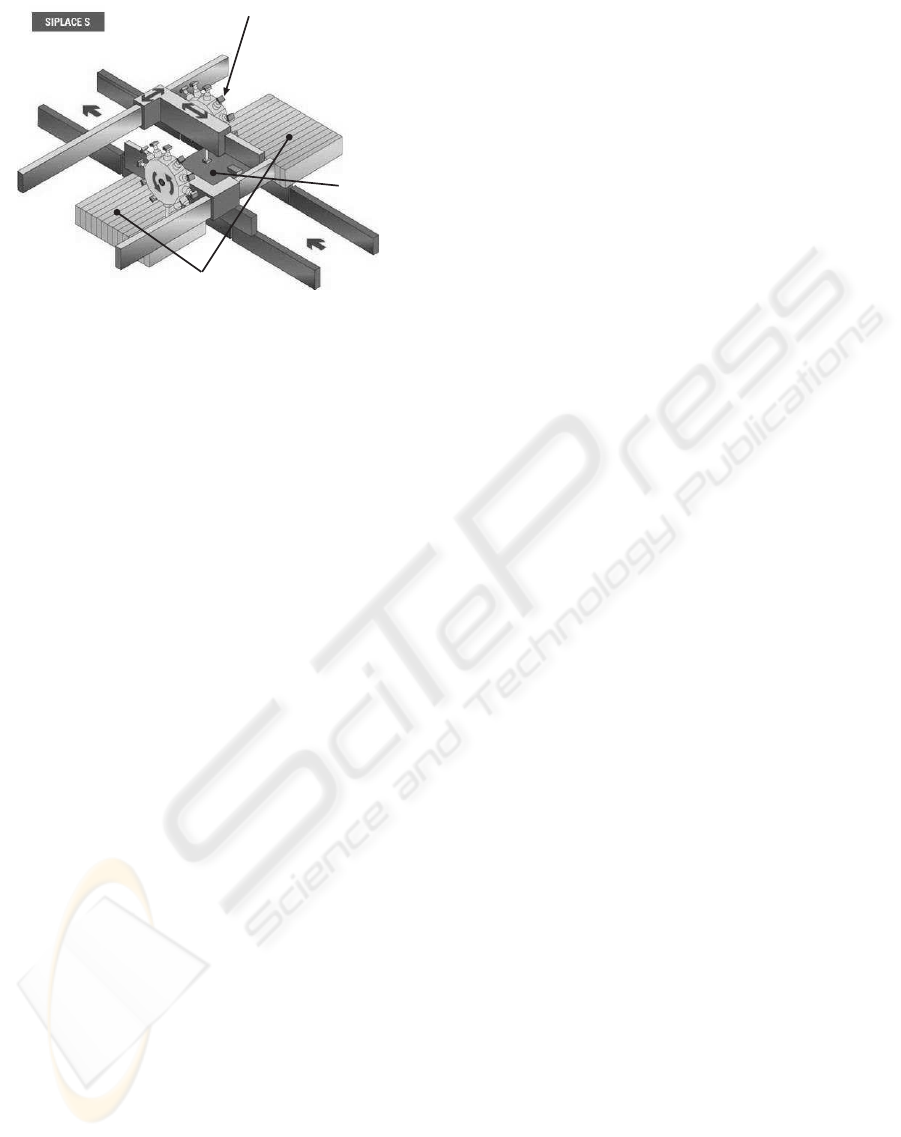
feeders
placementhead
andnozzles
PCB
Figure 1: There are many multi-head gantry machines
in Siplace-series of Siemens. (The image is taken from
Siemens www-page.).
them onto the PCB being manufactured. The determi-
nation of the route the placement head travels during
a placement job can be considered a special asymmet-
ric travelling salesman problem (ATSP) . Solving the
problem requires efficient heuristics that have been
studied in (Ball and Magazine, 1988) (Leip
¨
al
¨
a and
Nevalainen, 1989) for example.
In this article the optimal control of a multi-head
gantry placement machine (Sun et al., 2004) is dis-
cussed. For example Siemens has this type of ma-
chines, see Figure 1 for details. Multi-head gantry
machines have increased their popularity in recent
times due to their flexibility and relatively low acqui-
sition price. In this machine the PCB is positioned
firmly on the stationary table. The machine has a
placement arm with a placement head at one end. The
placement head moves above the PCB and the com-
ponent feeders in (x, y)-plane parallel to the PCB. The
feeders are stationary and arranged as a linear array
along the x-coordinate-side of the PCB fixation table.
There are several (1-30 pieces) spindles (nozzle hold-
ers) in a placement head and each spindle can hold
any type of nozzle. A nozzle can grab a single compo-
nent at a time and different components may require
certain nozzle. Every nozzle of the placement head
can hold a component simultaneously. The placement
head can place one component at a time onto a PCB
and it must then move to the position required by the
next component. While performing a placement job
the machine will retrieve multiple components at a
time from the feeders into the nozzles of the place-
ment head and place them to predetermined positions
on the PCB. This process will be repeated as many
times as necessary. See (Py
¨
otti
¨
al
¨
a et al., 2005) for
more details on the design of the multi-head gantry
machine.
The controlling of a multi-head gantry machine
can be seen as a sequence of multiple decisions.
These include among others the selection of nozzles,
the feeder arrangement, the component pick-up and
placement sequencing. When the decisions are done
consecutively, each of them depends on the previous
ones. For instance the optimal component pick-up se-
quence depends on the beforehand selected nozzles
and the order in which the components are in feeder.
In this hierarchical way it is possible to find a suffi-
ciently efficient solution for manufacturing a certain
PCB but it will not guarantee a globally optimal solu-
tion in a sence of assembly time of a single job. Even
though the hierarchical method is complicated it has
led to some good results (Kumar and Li, 1995; Crama
et al., 1990; Lee et al., 1999) whereas the joint mod-
elling of this machine type leads to a mathematical
model of impractically high complexity.
The approach used in this article is slightly differ-
ent from previous studies. Our aim is not to solve the
whole control problem but instead to consider a par-
ticular subproblem in greater detail. The subproblem
can be chosen because it is a part of the overall manu-
facturing problem. All subproblems have to be solved
in order to solve the entire problem. In this work, it
is especially asked in which order the multi-head arm
should pick up the components to be placed so that
the movements of the arm are minimized for a certain
printed circuit board (PCB). Two cases are discussed
here. In the first case the sequence for performing the
placements, the nozzles in the placement arm and the
order of component reels in the feeder are predeter-
mined and a pick-up sequence of the components and
its cost shall be computed. This is called the single
pick-up event problem (SPE). In the second case the
assumptions are as above, but the computed pick-up
sequence should be the one with a minimal cost (i.e.
time). This is called the minimal pick-up sequence
problem, MPS. Here again, the optimal machine con-
trol depends on both the placement sequence and the
feeder assignment at the same time, see (Leip
¨
al
¨
a and
Nevalainen, 1989) for discussion of the special case
with a single nozzle in the pick-up-placement head.
In this paper, there are multiple nozzles in the place-
ment head and the arm may contain multiple copies of
the same nozzle type as it is presently common due to
the very skewed distribution of different component
types on PCBs.
The rest of the work is organized as follows. The
notation and terminology are presented in section 2,
as well as the actual research problems. Then in sec-
tion 3 the problems are solved and possible algorithms
are proposed. The best proposed algorithm is tested
and the results introduced in section 4. The final sec-
tion consists of the concluding remarks.
MINIMIZING THE ARM MOVEMENTS OF A MULTI-HEAD GANTRY MACHINE
327