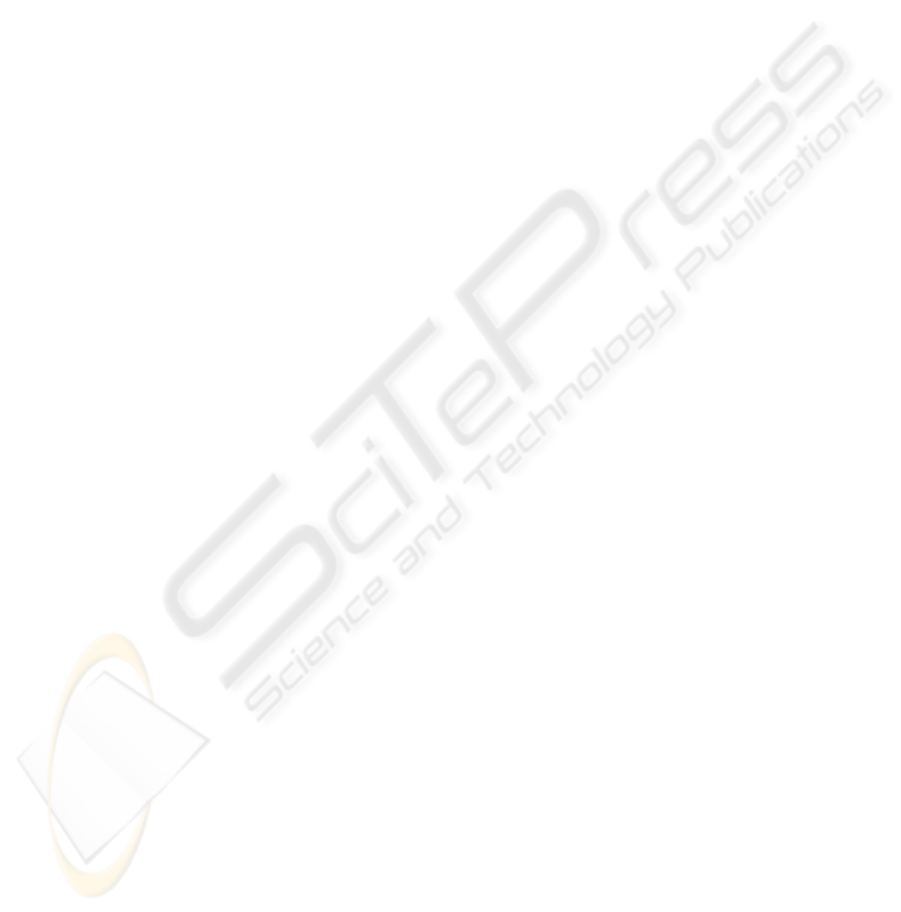
Eberhart, R. C. and Kennedy, J. (1995). A new optimizer
using particle swarm theory. In Proceedings of the
Sixth International Symposium on Micromachine and
Human Science., pages 39–43, Nagoya, Japan.
Faigl, J., Klacnar, G., Matko, D., and Kulich, M. (2006).
Path planning for multi-robot inspection task consid-
ering acceleration limits. In Proceedings of the four-
teenth International Electrotechnical and Computer
Science Conference ERK 2005, pages 138–141.
Franklin, W. R., Akman, V., and Verrilli, C. (1985). Voronoi
diagrams with barriers and on polyhedra for minimal
path planning. In Journal The Visual Computer, vol-
ume 1(4), pages 133–150. Springer Berlin.
Hess, M., Saska, M., and Schilling, K. (2006). Formation
driving using particle swarm optimization and reactive
obstacle avoidance. In Proceedings First IFAC Work-
shop on Multivehicle Systems (MVS’06), Salvador,
Brazil.
Janabi-Sharifi, F. and Vinke, D. (1993). Integration of the
artificial potential field approach with simulated an-
nealing for robot path planning. In Proceedings of 8th
IEEE International Symposium on Intelligent Control,
pages 536–41, Chicago, IL, USA.
Kennedy, J. and Eberhart, R. (1995). Particle swarm opti-
mization. In Proceedings International Conference on
Neural Networks IEEE, volume 4, pages 1942–1948.
Khatib, O. (1986). Real-time obstacle avoidance for manip-
ulators and mobile robots. In The International Jour-
nal of Robotics Research, volume 5, pages 90–98.
Kunigahalli, R. and Russell, J. (1994). Visibility graph ap-
proach to detailed path planning in cnc concrete place-
ment. In Automation and Robotics in Construction XI.
Elsevier.
Latombe, J.-C. (1996). Robot motion planning. KluverAca-
demic Publishers, fourth edition.
Liu, S., Mao, L., and Yu, J. (2006). Path planning based on
ant colony algorithm and distributed local navigation
for multi-robot systems. In Proceedings of IEEE In-
ternational Conference on Mechatronics and Automa-
tion, pages 1733–8, Luoyang, Henan, China.
Macas, M., Novak, D., and Lhotska, L. (2006). Particle
swarm optimization for hidden markov models with
application to intracranial pressure analysis. In Biosig-
nal 2006.
Martinez-Alfaro, H. and Gomez-Garcia, S. (1998). Mobile
robot path planning and tracking using simulated an-
nealing and fuzzy logic control. In Expert Systems
with Applications, volume 15, pages 421–9, Monter-
rey, Mexico. Elsevier Science Publishers.
Nearchou, A. (1998). Solving the inverse kinematics prob-
lem of redundant robots operating in complex envi-
ronments via a modified genetic algorithm. Journal of
Mechanism and Machine Theory, 33/3:273–292.
Parsopoulos, K. E. and Vrahatis, M. N. (2006). Parti-
cle swarm optimization method for constrained op-
timization problems. In Proceedings of the Euro-
International Symposium on Computational Intelli-
gence.
Saska, M., Kulich, M., Klan
ˇ
car, G., and Faigl, J. (2006a).
Transformed net - collision avoidance algorithm for
robotic soccer. In Proceedings 5th MATHMOD
Vienna- 5th Vienna Symposium on Mathematical
Modelling. Vienna: ARGESIM.
Saska, M., Macas, M., Preucil, L., and Lhotska, L. (2006b).
Robot path planning using partical swarm optimiza-
tion of ferguson splines. In Proc. of the 11th IEEE
International Conference on Emerging Technologies
and Factory Automation. ETFA 2006.
Tu, J., Yang, S., Elbs, M., and Hampel, S. (2003). Genetic
algorithm based path planning for a mobile robot.
In Proc. of the 2003 IEEE Intern. Conference on
Robotics and Automation, pages 1221–1226.
Vaz, A. I. F. and Fernandes, E. M. G. P. (2006). Optimiza-
tion of nonlinear constrained particle swarm. In Re-
search Journal of Vilnius Gediminas Technical Uni-
versity, volume 12(1), pages 30–36. Vilnius: Tech-
nika.
Ye, J. and Qu, R. (1999). Fairing of parametric cubic
splines. In Mathematical and Computer Modelling,
volume 30, pages 121–31. Elseviers.
HIERARCHICAL SPLINE PATH PLANNING METHOD FOR COMPLEX ENVIRONMENTS
123