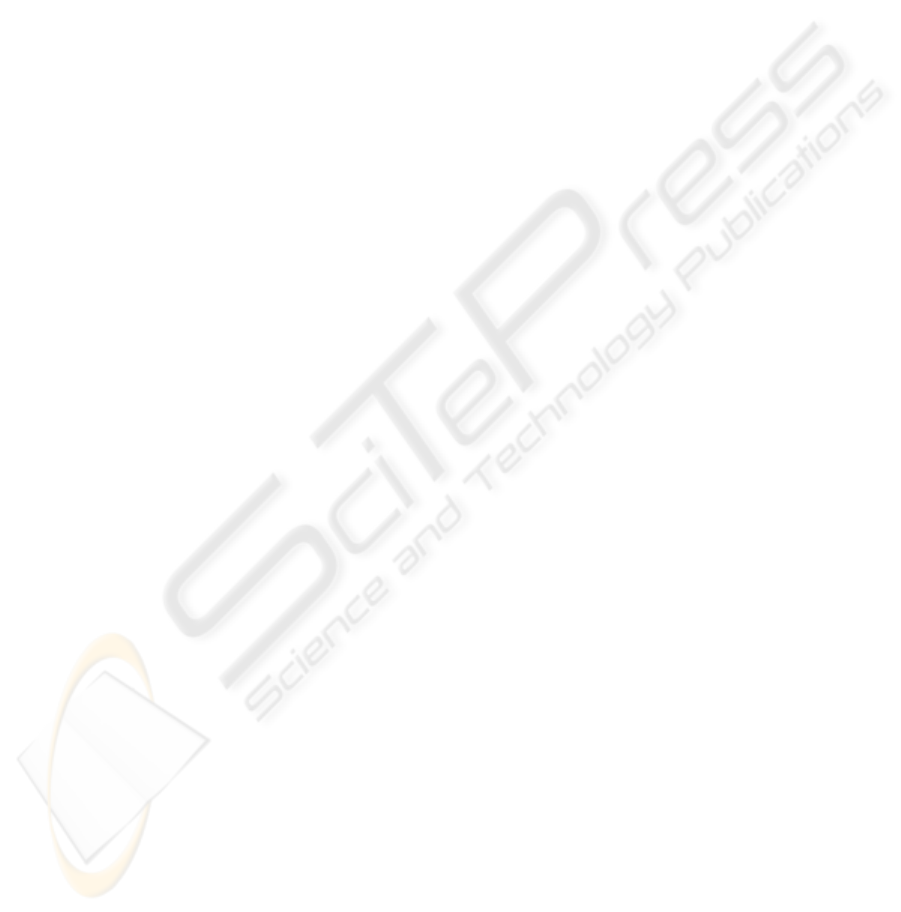
The number of platform trajectory graining points is
reduced and, for the most part, the platform moves
forward.
Work in progress is focusing on the inclusion of
obstacle avoidance in the control scheme in order to
improve coordination between the two subsystems.
Another work relates to the development of a control
strategy for seizure. This strategy takes into account
both of human-machine cooperation and the
presence of obstacles in the environment.
REFERENCES
P. Baerlocher, “Inverse kinematics techniques for the
interactive posture control of articulated figures,” PhD
thesis, Lausanne, EPFL 2001.
B. Bayle, J.Y. Fourquet, M. Renaud, “Manipulability
Analysis for Mobile Manipulators,” In ICRA’2001,
Seoul, South Korea, pp. 1251-1256, May 2001.
B. Bayle, J. Y. Fourquet, M. Renaud. Using
Manipulability with Nonholonomic Mobile
Manipulators, 3rd International Conference on Field
and Service Robotics (FSR'2001), Helsinki (Finlande),
11-13 Juin 2001, pp.343-348
M. Busnel, R. Gelin and B. Lesigne, “Evaluation of a
robotized MASTER/RAID workstation at home:
Protocol and first results”, Proc. ICORR 2001, Vol. 9,
pp. 299-305, 2001.
G. Campion, G. Bastin and B. D’Andréa-Novel,
“Structural proprieties and classification of kinematic
and dynamic models of wheeled mobile robots,” IEEE
Transaction on Robotics and Automation, Vol. 12, no.
1, pp. 47-62, February 1996.
P. Dario, E. Guglielmelli, B. Allotta, “MOVAID: a
personal robot in everyday life of disabled and elderly
people,” Technology and Disability Journal, no 10,
IOS Press, 1999, pp. 77-93.
H. G. Evers, E. Beugels and G. Peters, “MANUS toward
new decade”, Proc. ICORR 2001, Vol. 9, pp. 155-161,
2001.
P. Hoppenot, E. Colle, “Mobile robot command by man-
machine co- operation - Application to disabled and
elderly people assistance,” Journal of Intelligent and
Robotic Systems, Vol. 34, no 3, pp 235-252, July
2002.
S. Kang, K. Komoriya, K. Yokoi, T. Koutoku, K. Tanie,
“Utilization of Inertial Effect in Damping-based
Posture Control of Mobile Manipulator,” International
Conference on Robotic and Automation, pp. 1277-
1282, Seoul, South Korea, May 2001.
O. Khatib, “Inertial properties in robotic manipulation: an
object-level framework,” Int J. Robotics Research,
Vol. 13, No. 1, pp. 19-36, 1995.
H. Kwee, C.A. Stanger, “The Manus robot arm”,
Rehabilitation Robotics News letter, Vol. 5, No 2,
1993.
K. Nagatani, T. Hirayama, A. Gofuku, Y. Tanaka,
“Motion planning for Mobile Manipulator with
keeping Manipulability,” IROS 2002, , pp 1663-1668,
Lausane, Switzerland, October 2002.
Y. Nakamura, “Advanced robotics, redundancy and
optimization,” Addison Wesley Publishing, 1991.
J. K. Salisbury and J.J. Craig, “Articulated hands: Force
Control and Kinematic Issues,” Intl. J. Robotics
Research, Vol. 1, no. 1, pp. 4-17, 1982.
L. Sciavicco and B. Siciliano, “Modeling and control of
robot manipulators,” The McGraw-Hill companies,
Inc., 1996.
H. Seraji, “An on-line approach to coordinated mobility
and manipulation,” In ICRA'1993, Atlanta, USA, May
1993, pp. 28-35.
D.E Whitney, “Resolved Motion Rate Control of
Manipulators and Human Prosthetics,” IEEE Trans on
Man Machine Systems, Vol 10, pp. 47-53, 1969.
Y. Yamamoto and X. Yun, “Coordinating locomotion and
manipulation of mobile manipulator,” Recent Trends
in Mobile Robots Zheng Y. Ed., 1987.
Y. Yamamoto and X. Yun, “Unified analysis an mobility
and manipulability of mobile manipulators,” IEEE Int.
Conf. Robotics and Automation, Detroit, pp. 1200-
1206, USA, 1999.
T. Yoshikawa, “Manipulability of Robotic Mechanisms,”
International Journal of Robotics Research, 1985, Vol.
4, no. 2, pp. 3-9.
Yoshikawa, T.: Foundation of robotics: Analysis and
control, The MIT Press, 1990.
T. Yoshikawa, “Analysis and control of Robot
manipulators with redundancy,” In M. Brady & R.
Paul, editors, Robotics Research: The First
International Symposium, MIT Press, pp. 735-747,
1984.
H.F.M. Van der Loos, “VA/Stanford Rehabilitation
Robotics Research and Development Program:
Lessons Learned in the Application of Robotics
Technology to the Field of Rehabilitation,” IEEE
Trans. Pn Rehabilitation Engineering, Vol. 3, n°1, pp.
46-55, March 1995.
ICINCO 2007 - International Conference on Informatics in Control, Automation and Robotics
208