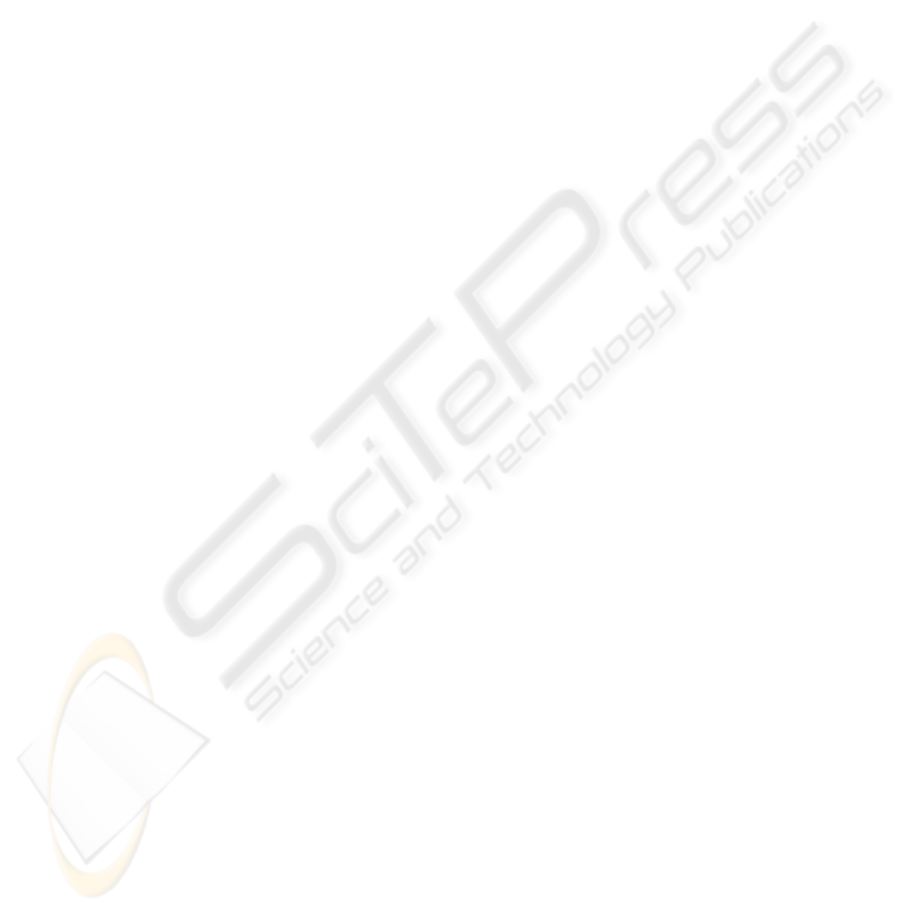
TASK PLANNER FOR HUMAN-ROBOT INTERACTION INSIDE
A COOPERATIVE DISASSEMBLY ROBOTIC SYSTEM
Carolina Díaz, Santiago Puente and Fernando Torres
University of Alicante
Crta San Vicente del Raspeig s/n
PO Box 03080, San Vicente del Raspeig- Spain
Keywords: Human-robot interaction, cooperative, disassembly, task planner.
Abstract: This paper develops a task planner that allows including a human operator which works cooperatively with
robots inside an automatic disassembling cell. This method gives the necessary information to the system
and the steps to be followed by the manipulator and the human, in order to obtain an optimal disassembly
and a free-shock task assignation that guarantees the safety of the human operator.
1 INTRODUCTION
Disassembly is defined as the process of separating
pieces that compose an object (Torres and Puente,
2006). In this process it is very useful to consider
the advantages of cooperative tasks, in which two or
more robots take part, or tasks in which the
intervention of a human being is required (Adams
and Skubic, 2005). Some of those advantages are:
making tasks that a single robot can not do; sharing
information and resources; greater tolerance to
failures; and attending between manipulators and
humans for different tasks. Working in a coordinated
way also provides the system a faster and an
effective disassembly, which allows a consequent
saving of money to the industries that apply it.
The value of a group of entities collaborating
among them, working in group as a team has been
proven many times in many domains. For example,
in nature a group of animals working cooperatively
as a team, can manage to hunt a stronger and bigger
animal. Also in the military service a group of men
with limited resources and specific abilities are
united to create groups with an incredible capacity.
These examples illustrate that a group of entities
with similar or different abilities joined to work in a
team, can produces a work unit with abilities and
capacities greater than the sum of its parts (Navarro-
Serment, et al., 2002). Including two or more agents
working in a cooperative way increases the
performance of the disassembly system, because of
the synergy produces a group of units working
together as a team.
Two groups can be distinguished in cooperative
robots work field:
• Two or more robots working cooperatively to
solve different tasks. This group is called robot-
robot application for forward examples (Tinós and
Terra, 2002; Fonseca and Tenreiro, 2003).
• Cooperative tasks in which robots manipulators
and humans interact, named in this paper robot-
human application (Kumar et al., 2000; Hägele et
al., 2002).
The remarkable issue that differences these two
groups is that when humans and robots interact, the
system must consider more external and internal
sensors in order to avoid humans suffering any
physical damage.
It is important to highlight that this work tries to
use the intervention of a human in task in which the
person has more abilities and general comprehension
than a robot. Robot manipulators transform in
intelligent agents that assist humans in all kind of
task and activities, taking advantages of the
resources and characteristic of each agent and
minimizing the negative properties collaborating
between them.
In the present paper it is observed the advantages
that bring to include a person working in a
cooperative way inside a disassembling cell. Until
recently in most of industrial environments the robot
manipulator was isolated through securities fences,
19
Díaz C., Puente S. and Torres F. (2007).
TASK PLANNER FOR HUMAN-ROBOT INTERACTION INSIDE A COOPERATIVE DISASSEMBLY ROBOTIC SYSTEM.
In Proceedings of the Fourth International Conference on Informatics in Control, Automation and Robotics, pages 19-24
DOI: 10.5220/0001645100190024
Copyright
c
SciTePress