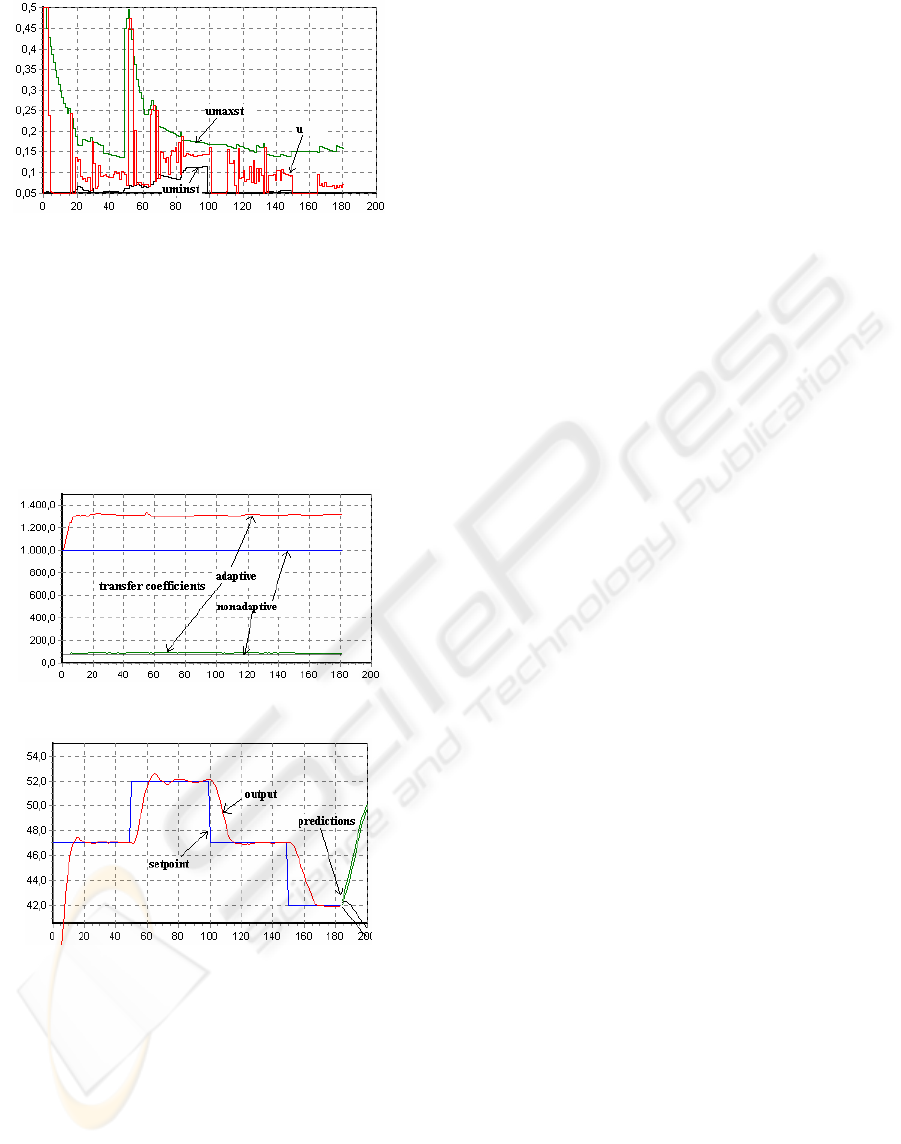
Figure 12: Controller output (adaptive case).
Initial the temperature of cold and hot fluids
is
°20 . The evolution of the estimations of heat
transfer coefficients is presented in figure 13. To
obtain these estimations, both rotations and
translations of temperature distributions and rule
based correction of heat transfer coefficients are
used. In figure 14 it is used the same conditions for
heat transfer coefficients, but it is not used this
approach.
Figure 13: Parameters identification.
Figure 14: Setpoint, output (adaptive case).
As a result, the quality of control algorithm
decreases.
5 CONCLUSION
The paper presents a simple and intuitive algorithm
applied in the case of a non linear process: heat
exchanger. A non-linear model of the process, based
on finite difference method, is used. This approach
is a numerical alternative to usual criteria equations;
offer a way to ensure the accuracy of a best-fit heat
exchanger selection, and point out that the fluids
properties must not be mathematically emphases.
Using the process model and a reduce number of the
sequences control, it is simulated the future
behaviour of the process and based on a set of rules
it is chosen the signal control considered optimum at
the actual moment. Of course there are some
difficulties such as the proof of the stability, the way
of choosing of the control sequences and the set of
rules which will lead to a better result, choosing
some parameters etc. Although, taking into account
the simplicity of this algorithm the obtained results
in the case of the presented examples by nonlinear
systems are remarkable. A demo application that
implements the proposed algorithm can be
downloaded (see web link). In the future, starting
from the proposed algorithm, the work will focus on:
the optimal chosen of the control parameters, the
study of other set of control sequences, the study of
other set of control rules, adaptive case and practical
implementation.
REFERENCES
Camacho E., Bordons C. (1999), “Model Predictive
Control” Spriger-Verlag
Radu Balan: “Adaptive control systems applied to
technological processes”, Ph.D. Thesis 2001,
Technical University of Cluj-Napoca Romania.
Dougherty, D., Cooper, D., “A practical multiple model
adaptive strategy for a single loop”, Control
Engineering Practice 11 (2003) pp. 141-159
Fischer M., Nelles O., Fink A., “Adaptive Fuzzy Model
Based Control” Journal a, 39(3), Pp22-28, 1998
Fink A., Topfer S., Isermann O., “Neuro and Neuro-Fuzzy
Identification for Model-based Control”, IFAC
Workshop on Advanced Fuzzy/Neural Control,
Valencia, Spain, Pages 111-116, 2001
Ozisik M. N., “Heat Transfer - A Basic Approach”,
McGraw-Hill Book Comp. 1985.
Douglas I.M., “Process dynamics and control”, Prentice
Hall Inc. 1972
Bălan, Radu, Vistrian Maties, Olimpiu Hancu, Sergiu
Stan, A Predictive Control Approach for the Inverse
Pendulum on a Cart Problem, IEEE-ICMA 2005 pag.
2026-2031 July 29 - August 1, 2005 Niagara Falls,
Ontario, Canada.
Available online, accessed in March, 2007:
http://zeus.east.utcluj.ro/mec/mmfm/download.htm
APPLICATIONS OF A MODEL BASED PREDICTIVE CONTROL TO HEAT-EXCHANGERS
301