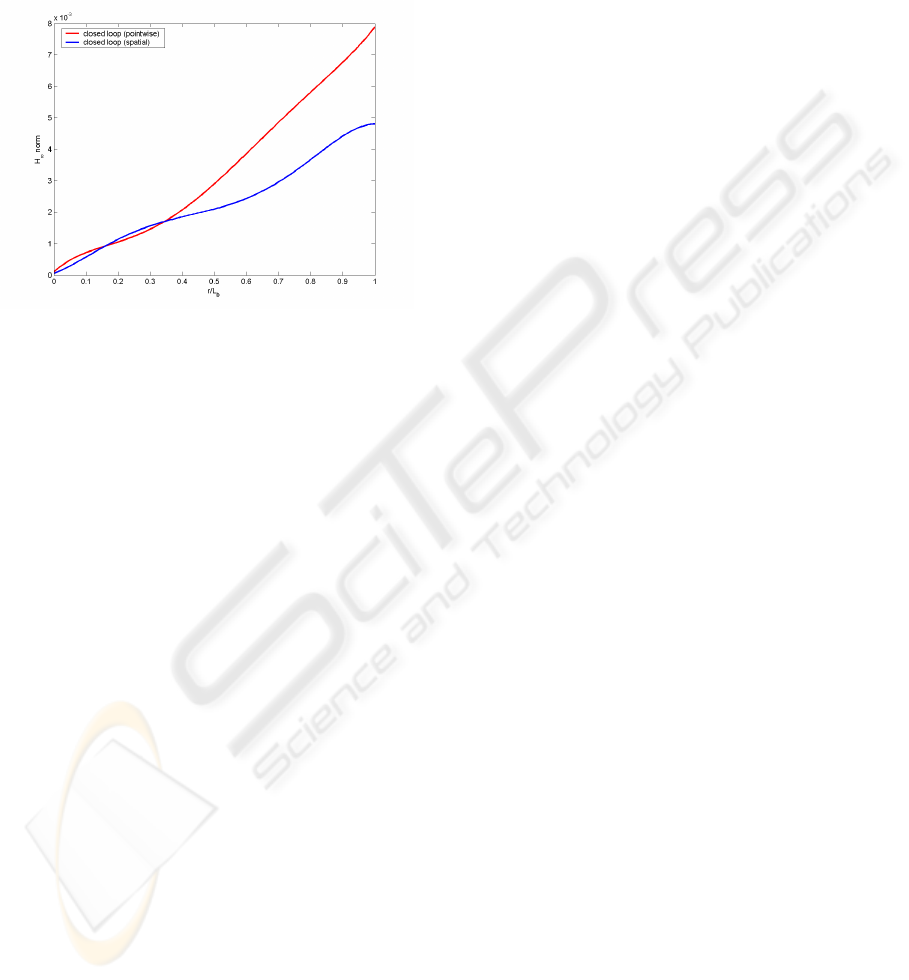
its first two flexural modes in comparable efficiency
(Kırcalı, 2006). On the other hand, the simulated
H
∞
norms of the smart beam as a function of r,
shown in Figure 10, showed that the spatial
H
controller has a slight superiority on suppressing the
vibration levels over entire beam.
Figure 10: Simulated H
∞
norm plots of closed loop
systems under the effect of controllers.
4 CONCLUSION
This study presented the active vibration control of a
cantilevered smart beam. A spatial
H
∞
controller
was designed for suppressing the first two flexural
vibrations of the smart beam. The efficiency of the
controller was demonstrated both by simulation and
experimental implementations. The effectiveness of
the spatial controller on suppressing the vibrations of
the smart beam over its entire body was also
compared with a pointwise controller.
REFERENCES
Çalışkan T., 2002. Smart Materials and Their Applications
in Aerospace Structures. Ph.D. Thesis. Middle East
Technical University, Ankara, Turkey.
Meirovitch L., 1986. Elements of Vibration Analysis. The
McGraw-Hill Company.
Nalbantoğlu V., 1998. Robust Control and System
Identification for Flexible Structures. Ph.D. Thesis,
University of Minnesota, USA.
Hughes P.C., Skelton R.E., 1981. Modal Truncation for
Flexible Spacecraft, Journal of Guidance and Control,
vol.4, no.3.
Moheimani S.O.R., Pota H.R., Petersen I.R., 1997. Spatial
Balanced Model Reduction for Flexible Structures.
Proceedings of the American Control Conference,
3098-3102. Albuquerque, New Mexico.
Clark R.L., 1997. Accounting for Out-Of-Bandwidth
Modes in the Assumed Modes Approach: Implications
on Colocated Output Feedback Control. Transactions
of the ASME, Journal of Dynamic Systems,
Measurement, and Control, vol.119, 390-395.
Yaman Y., Çalışkan T., Nalbantoğlu V., Prasad E.,
Waechter D., Yan B., 2001. Active Vibration Control
of a Smart Beam, Canada-US CanSmart Workshop on
Smart Materials and Structures. 137-147, Montreal,
Canada.
Yaman Y., Ülker F. D., Nalbantoğlu V., Çalışkan T.,
Prasad E., Waechter D., Yan B., 2003. Application of
H
∞
Active Vibration Control Strategy in Smart
Structures. 3rd International Conference on Advanced
Engineering Design. Paper A5.3, Prague, Czech
Republic.
Yaman Y., Çalışkan T., Nalbantoğlu V., Ülker F. D.,
Prasad E., Waechter D., Yan B., 2002. Active
Vibration Control of Smart Plates by Using
Piezoelectric Actuators, 6th Biennial Conference on
Engineering Systems Design and Analysis, Paper
APM-018. Istanbul, Turkey.
Moheimani S.O.R, Fu M., 1998. Spatial H
2
Norm of
Flexible Structures and its Application in Model Order
Selection. International Proceedings of 37th IEEE
Conference on Decision and Control, Tampa Florida,
USA.
Moheimani S.O.R., Pota H.R., Petersen I.R., 1997. Spatial
Balanced Model Reduction for Flexible Structures,
Proceedings of the American Control Conference, pp.
3098-3102, Albuquerque, New Mexico.
Moheimani S.O.R., Petersen I.R., Pota H.R., 1999.
Broadband Disturbance Attenuation over an Entire
Beam, Journal of Sound and Vibration, 227(4): 807-
832.
Halim D., Moheimani S.O.R., 2002. Experimental
Implementation of Spatial H
∞
Control on a
Piezoelectric Laminate Beam. IEEE/ASME
Transactions on Mechatronics, vol.7, no: 3.
Kırcalı Ö.F., Yaman Y., Nalbantoğlu V., Şahin M.,
Karadal F.M., 2005. Spatial System Identification of a
Smart Beam by Assumed-Modes Method and Model
Correction. Kayseri VI Aeronautics Symposium.
Nevsehir, Turkey (in Turkish).
Halim D., 2002. Vibration Analysis and Control of Smart
Structures, PhD. Thesis,. School of Electrical
Engineering and Computer Science, University of
Newcastle, Australia.
Kırcalı Ö.F., 2006. Active Vibration Control of a Smart
Beam: a Spatial Approach, M.S. Thesis, Middle East
Technical University, Ankara, Turkey.
Moheimani S.O.R., Halim D., Fleming A.J., 2003. Spatial
Control of Vibration. Theory and Experiments, World
Scientific Publishing Co. Pte. Ltd.
ICINCO 2007 - International Conference on Informatics in Control, Automation and Robotics
328