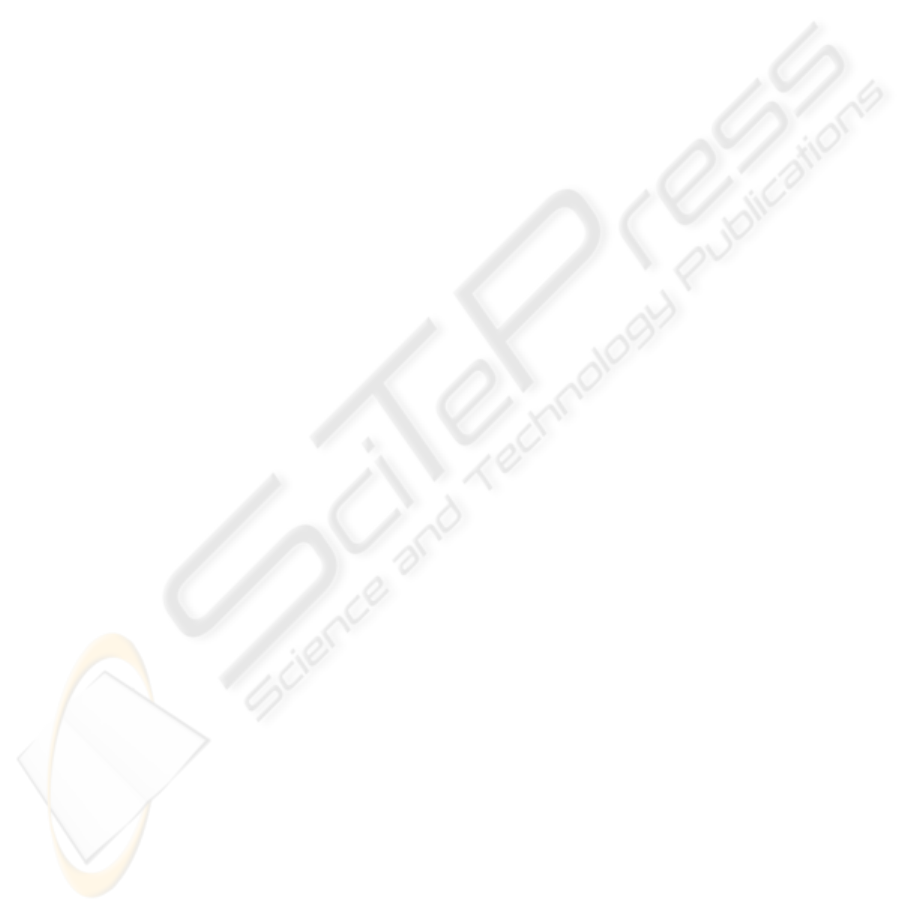
Gathering of vegetable material: collection of
vegetable material is a fundamental activity for
phytochemistry. Every pharmaceutical preparation
that uses as raw material plant parts such as leaves,
stems, roots, flowers, and seeds, with known
pharmacological effect is considered phytotherapic
(extracts, dyes, ointments and capsules). Thus, just
as in botanical collection, this is an activity that can
be accomplished by a robot operating in large-sized
trees, therefore minimizing risk for the humans
involved in the collection.
Gathering of Insect Specimens: usually, for
collecting insects in higher levels, nets spread
around the tree and a source of smoke below it are
used. The great discussion about this technique is
that one not only captures the desired insects, but
one ends up killing most of the insects that inhabit
that tree as well. Thus, one proposes to use a trap,
positioned in the robot, containing a pheromone or
equivalent substance as bait, specific for the insect
species one wants to capture. One can even adapt
cameras and sensors in the trap to gather images of
the moment of capture. With a trap thus
implemented, one reduces the negative
environmental impact of the capture. Another
relevant issue would be the possibility that the robot
moves along the day to capture varied insect
specimens at different heights in different hours, to
check for variations in insect populations according
to the height, and the hour of the day.
Climatic studies: climatic or microclimatic studies
refer to works on microenvironments in native
vegetation and/or reforested areas. It is important to
study the different energy flows:
horizontal and
vertical. The vertical directly reflects the results of
solar radiation, which decisively influences the
horizontal energy flows: air masses, hot and cold
fronts, action centers. Solar radiation determines the
whole system, and may be analized according to its
elements: temperature, pressure, and humidity,
greatly influencing biogeographic characteristics,
geomorphologic and hydrologic phenomena etc.
Thus, the robot can be equipped with sensors for
such measures, to collect data on the desired
elements.
Studies on biosphere/atmosphere interaction:
biosphere environments are the group of biotic or
abiotic factors that interfere in the life conditions on
a certain region of the biosphere. In the case of
forests the aerial environment is studied, and the
most important elements to consider are: light,
oxygen, ice formation, winds, humidity and carbon
gas. In order to register all this information, the
robot can be endowed with specific sensors for each
kind of required measure, to collect data regarding
the elements at hand, and to provide information on
them regarding both height and time variations.
Studies on arboreal fauna: fauna studies are
hampered by the existence of many leaves, or very
dense treetops, as the lack of existing natural light
hinders the observation of the species. Other usually
relevant points are the difficulty to obtain a proper
angle due to the great heights involved, and the very
presence of human beings in that specific
environment, easily detected by their movements,
noise and odors. For this type of task, the robot can
be fitted with cameras to capture both static and
dynamic images. These can then be stored locally in
some type of memory card, or transmitted via
communication interface to a base station.
Sensors Network: robots carrying a group of
sensors and fitted with a communication interface,
for instance Wi-fi or other similar technology can be
dispersed in the forest to capture data regarding the
ecological behavior in the area at hand.
Measurements such as the ones already mentioned in
climatic studies and biosphere/atmosphere
interaction can be shared among robots or even
retransmitted among robots to reach the base station,
without the need for the researcher to “pay visits” to
the reading points.
2 GOAL AND PURPOSE
Thus, considering this poorly explored area, one
proposes the Kamanbaré robotics platform.
Kamanbaré is a biomimetic robot, i.e., inspired in
nature, with the purpose of climbing trees for
environmental research applications. The proposed
work represents a progress in robot applications,
both for the fact of environmental research
applications, and for its tree-climbing ability, with
computer-controlled devices configured to be used
as paws.
The project’s main application is climbing trees
for non-invasive search purposes, reaching points (at
high altitudes) that may offer risk to humans.
The development was driven mainly to seek for
robot stability and efficiency regarding the paws.
The adopted line of research is an implementation
inspired in nature. One must stress here that the
system doesn't mimic nature, by copying an animal
or insect to accomplish the desired work, but rather,
a robot development project that combines the
climbers' best characteristics (insects and lizards)
considering the available technologies and the
associated cost/benefit ratio, in other words, some
parts were inspired in certain solutions found in
nature, while other parts were inspired in different
elements.
KAMANBARÉ - A Tree-climbing Biomimetic Robotic Platform for Environmental Research
479