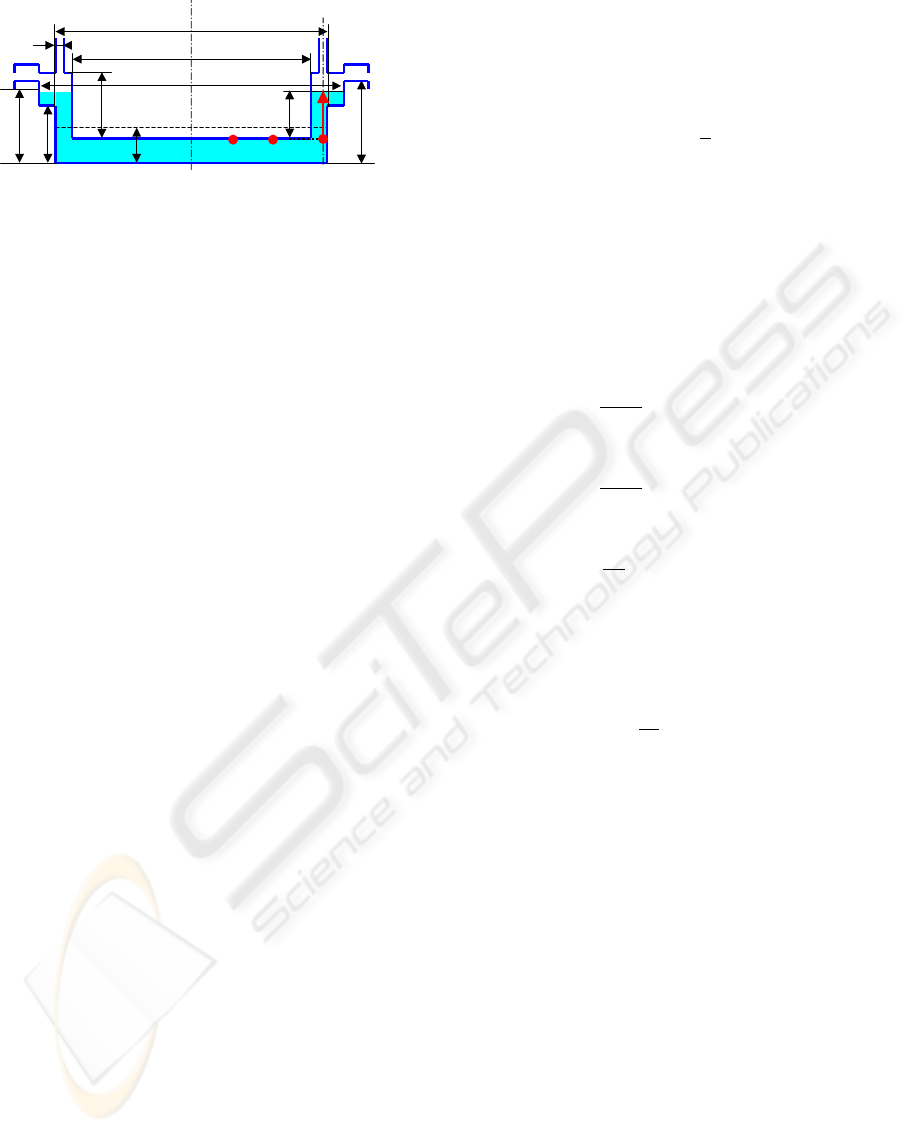
h(t)
d
1
d
3
d
2
b
1
b
2
b
3
4
P
1
d
1
= 0.1970, b
1
= 0.0485,
d
2
= 0.2200, b
2
= 0.0400,
d
3
= 0.2550, b
3
= 0.0590,
d
4
= 0.0080, b
4
= 0.0520. [m]
d
4
P
2
M
h(t)i
(i=1,2,3,4)
h
0
Figure 8: Shape of simplified casting mold shape.
reliability. However, press behavior cannot be calcu-
lated in real-time by the CFD analysis. The online
estimation of pressure in the mold is required in the
press casting system. The CFD is very effective to
analyze the fluid behavior in off-line, and hence it is
useful to predict the behavior and also optimize a cast-
ing plan. However, it is not enough for control design
in real-time, because of calculation time. Therefore,
we need to build a brief model for control design by
using CFD simulation and experiment.
The estimation of the pouring volume is available
by using the position data of the upper mold and es-
timating the contact time between under surface of
the upper mold and the molten metal. They are mea-
sured respectively using the encoder and the load-cell.
Then, to suitably realize the press velocity control
without the excessive pressure, the estimation of pres-
sure behavior is done by using the estimated data of
pouring volume. From this reason, we build a mathe-
matical model of molten metal pressure for the press
velocity.
The mold shape used in authors study has a large
convex parts with cross section of A as shown in Fig-
ure 6. To examine the pressure behavior for the gen-
esis part of defect, a simplified mold shape plumbed
the parts of curve, slope and draft angle for the pri-
mary mold shape. The simplified mold shape is
shown in Figure 8, where b and d mean the height and
the diameter respectively. P
j
(j=1,2) are genesis parts
of defect. The pressure fluctuation in press is repre-
sented by using a pressure model for the ideal fluid
such that the incompressible and nonviscous fluid is
assumed. Here, h(t) in Figure 8 means the fluid level
from under surface of upper mold. The head pressure
P
j
is directly derived from h(t). The press distance
z(t) of upper mold is a downward distance from the
position at the contact time of the poured fluid and
the upper mold. As the press velocity increases, the
dynamical pressure is varied by the effect of the liq-
uidity pressure. Then, the hydrodynamic pressure for
peak fluid height area is involved in P
j
. Therefore,
pressure P
b
in P
j
is consisted of head and hydrody-
namic pressure, and is represented by Eq.(2).
P
b
(t) = ρgh(t) +
ρ
2
˙
h(t)
2
(2)
The flow passage areas have three situations,
case 1: π(d
2
− d
1
)
2
/4, case 2: π(d
3
− d
1
)
2
/4 and
case 3: nπd
2
4
/4, where the number n of the over-flow
as diameter d
4
is equal to twelve. Figure 8 represents
case 2. The following equations represent the fluid
level variation in the each situation, and they are sim-
ply derived by assuming the incompressible fluid.
h(t) =
case 1 : h(t) < h
sw1
,
d
2
2
d
2
2
−d
2
1
z(t)
case 2 : h
sw1
≤ h(t) < b
1
,
1
d
2
3
−d
2
1
(d
2
3
z(t) + d
2
1
h
sw1
)
case 3 : b
1
≤ h(t),
1
nd
2
4
{d
2
3
z(t) + (nd
2
4
− d
2
3
)b
1
}
(3)
, where h
sw1
and b
1
represent the threshold fluid level
of h(t) on case 1case 2, case 2case 3 respectively.
h
sw1
is expressed as follows. And,
h
sw1
=
d
2
2
d
2
1
(b
2
− h
0
) (4)
, where h
0
means the initial fluid height before the
upper mold touches to the molten metal. When the
fluid height h(t) equals to h
sw1
, the equation of h(t)
changes from case 1 to case 2. Then, when h(t)
reaches to the height of b
1
, h(t) of Eq.(3) is changed
from case 2 to case 3. As described the above, the
pressure response for press velocity is determined
from the both of initial fluid height and mold shape.
Eq.(2) or the mathematical pressure model of the
molten metal in a mold is validated from the fluid be-
havior analysis by FLOW-3D on the filling in a press.
Comparison of ideal fluid height h(t) in a simplified
mold and h(t) in CFD simulation, is shown in Fig-
ure 9. As the CFD analysis results, height behavior of
M
h(t)
i
(: the measurement points of the over-flow) in
Figure 8. The fluid height h(t) for the parts of over-
flow is obtained. The press velocity is set as 5[mm/s].
When the ideal(incompressible and nonviscous)
fluid height becomes steady-state response, the height
in CFD results show the lower value of h(z) due to
the compression of the fluid by a gravity force. Next,
MODELING ON MOLTEN METAL’S PRESSURE IN AN INNOVATIVE PRESS CASTING PROCESS USING
GREENSAND MOLDING AND SWITCHING CONTROL OF PRESS VELOCITY
501