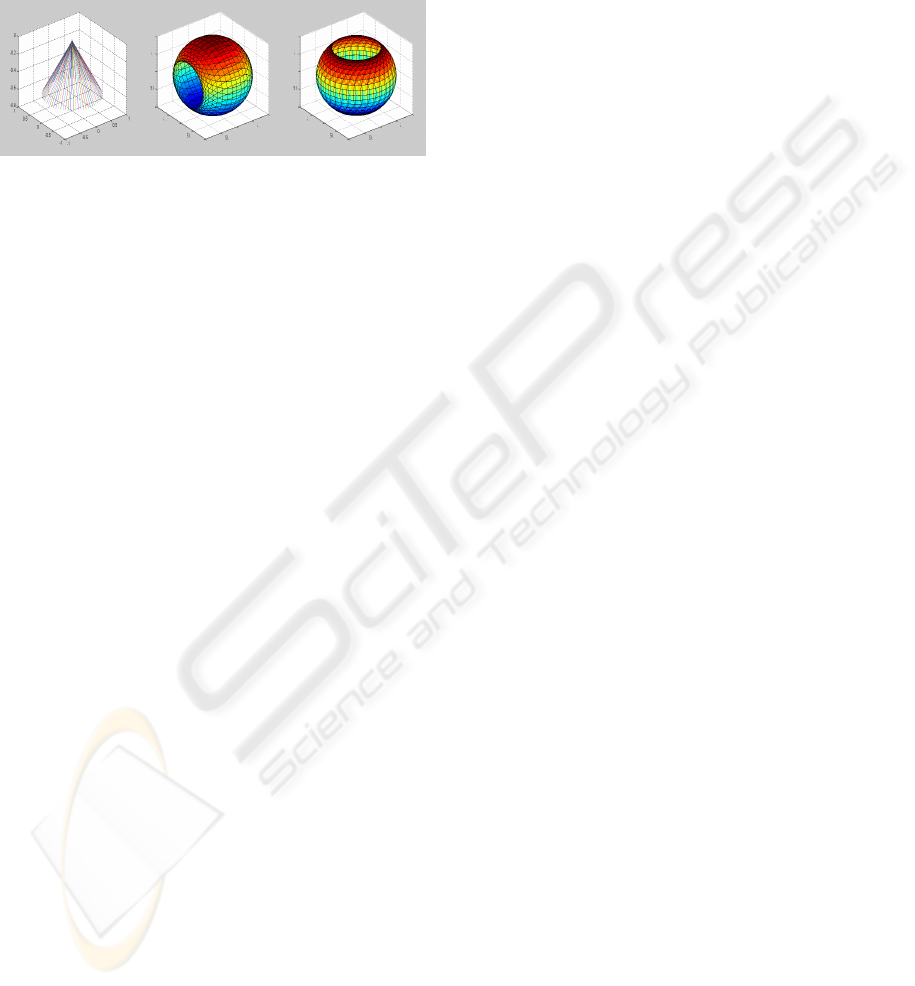
Indeed, a given orientation has several solutions for
joint variables. Fig. 14 illustrates these points by
defining the reachable workspace. The method we
propose consists in considering θ
4
as a constant
parameter in order to work out joint variables θ
5
and
θ
6
according to θ
4
. The choice of θ
4
is motivated by
optimization method.
Figure 14: Reachable workspace.
5.2 Control Strategy
The controller must satisfy real time requirements.
The sampling frequency is 20 Hz. Moreover, several
applications such as artificial vision and data
processing take place simultaneously. The controller
inputs are :
• Data from artificial vision and image
superimposition,
• Desired drill orientation,
• Actual angular values returned by digital
encoders.
The algorithm determines the values of V
xo
, V
yo
,
and V
zo
that are vector components in the flag
reference scorers of the robot. It determines θ
5
and
θ
6
with respect to θ
4
and verifies that solutions are in
the reachable workspace. If solutions are outside the
reachable workspace, the algorithm increments θ
4
with 1° and recalculates θ
5
and θ
6
. Incrementation is
repeated until a solution is found in the reachable
workspace.
6 FURTHER WORKS
The protocol used for identification will be applied
in a generic way on the other axes in order to obtain
a dynamic model of the robot. As a consequence, we
will be able to simulate the robot’s dynamic
behaviour and to develop safe and efficient control
design. On the other hand, our work will concern the
following points :
• Accuracy, wrist calibration,
• Study of position / orientation decoupling,
• Trajectory planning, ergonomics.
This medical robot is an invasive and semi-active
system. Therefore, an exhaustive study on reliability
will also be necessary (Dombre, 2001) before
starting clinical simulations and experimentations.
ACKNOWLEDGEMENTS
Authors thank the Doctor DERYCKE, a dental
surgeon specialized in implantology, CHIEF
EXECUTIVE OFFICER of DENTAL VIEW.
REFERENCES
Langlotz F, Berlemann U, Ganz R, Nolte LP., 2000.
Computer-Assisted Periacetabular Osteotomy. Oper.
Techniques in Orthop, vol 10, N° 1, pp. 14-19
Nikou C, Di Gioia A, Blackwell M, Jaramaz B, Kanade
T., 2000. Augmented Reality Imaging Technology for
Orthopaedic Surgery. Oper. Techniques in Orthop, vol
10, N° 1, pp. 82-86.
Taylor R.,1994. An Image Directed Robotic System for
Precise Orthopaedic Surgery. IEEE Trans Robot, 10,
pp. 261-275.
Lavallee S, Sautot P, Traccaz J, P. Cinquin P, Merloz P.,
1995. Computer Assisted Spine Surgery : a technique
for accurate transpedicular screw fixation using CT
data and a 3D optical localizer. Journal of Image
Guided Surgery.
Dutreuil J., 2001. Modélisation 3D et robotique médicale
pour la chirurgie. Thèse, Ecole des Mines de Paris.
Etienne D, Stankoff A, Pennnec X, Granger S, Lacan A,
Derycke R., 2000. A new approach for dental implant
aided surgery. The 4
th
Congresso Panamericano de
Periodontologia, Santiago, Chili.
Granger S., 2003. Une approche statistique multi-échelle
au recalage rigide de surfaces : Application à
l’implantologie dentaire. Thèse, Ecole des Mines de
Paris.
Chaumont R, Vasselin E, Gorka M, Lefebvre D., 2005.
Robot médical pour l’implantologie dentaire :
identification d’un axe, JNRR05. Guidel, pp 304-305.
Richalet J., 1998. Pratique de l’identification. Ed. Hermes.
Dombre E., 2001. Intrinsically safe active robotic systems
for medical applications. 1st IARP/IEEE-RAS Joint
Workshop on Technical Challenge for Dependable
Robots in Human Environments, Seoul, Korea.
B
FORWARD KINEMATICS AND GEOMETRIC CONTROL OF A MEDICAL ROBOT - Application to Dental
Implantation
115