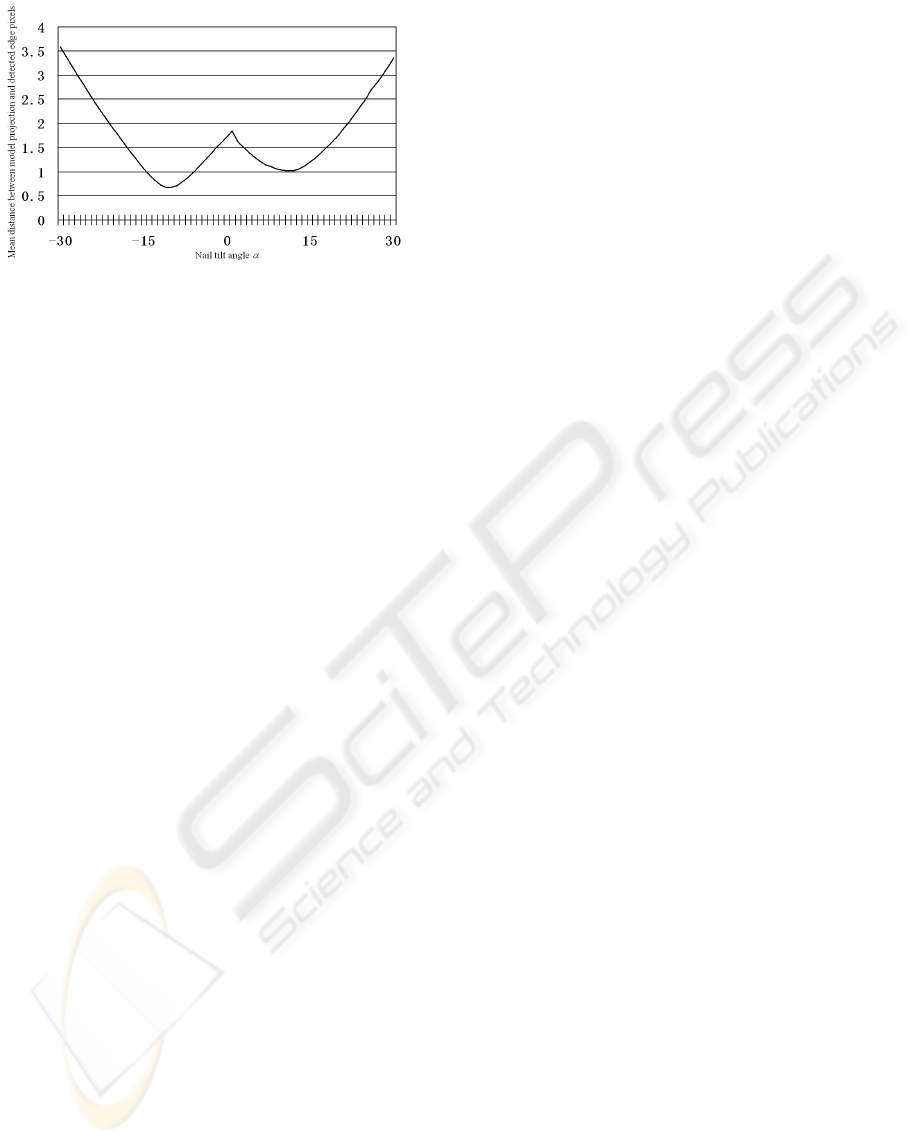
Figure 5: Optimization space of the nail tilt angle
α
.
3.2.4 Optimization of Parameter
α
We now convert a multiple-dimensional
optimization problem to a one-dimensional one,
where the parameter
α
can be optimized by a search
along a finite interval [-30
o
, +30
o
] (due to the
acquisition constraint that we put). A typical
optimization space of this parameter is shown in
Figure 5. It has a symmetrical shape and a clear
global optimum around the ground truth
α
=10.4
o
.
We could separate the optimization space into two
sub-intervals, i.e. [-30
o
, 0) and [0, 30
o
]. In each sub-
interval, the optimum of that sub-interval could be
easily found by a local search algorithm starting
from any initialization value. Actually, in all
experiments, we have simply initialized
α
by the
middle value of each sub-interval. The global
minimum is then found by taking the better one of
the two optima.
4 EXPERIMENTAL RESULTS
We designed and conducted two experiments to
analyze the accuracy and robustness of the proposed
approach. A SYNTHES® (STRATEC Medical,
Oberdorf, Switzerland) 9 mm solid titanium femoral
nail was used in our study. A Siemens ISO-C
3D
C-
arm (Siemens AG, Erlangen, Germany) was used to
acquire fluoroscopic images for our experiments.
In the first experiment, the nail was inserted into
a cadaveric human femur and was locked
proximally. The ground truth of the positions of the
DLHs was obtained after image acquisition by
inserting a custom-made steel rod through the hole
and then digitizing both top and bottom centers of
the rod using an optically trackable sharp pointer
(OPTOTRAK 3020, Northern Digital Inc, Waterloo,
Canada).
Three images acquired from different view
directions were used in our experiments, as shown in
Figure 6. For each image, we applied the proposed
approach ten times to estimate the poses of the
DLHs. The estimated results were compared to the
ground truth to compute the errors for each DLH,
which were defined as the angular difference
between the estimated hole axis and the one
obtained through pointer-based digitization, and the
positional difference of the entry point and its
ground truth along the plane perpendicular to the
hole axis (obtained by projecting the difference
vector into the plane perpendicular to the hole axis),
because the positional deviation along the hole axis
is not important for the task of insertion of distal
locking screw
In all studies, the poses of DLHs could be
automatically recovered. The angular and positional
errors are shown in Table I. Compared to ground
truths, the average angular error was found to be 1.0
o
(std=0.4
o
) and the average positional error along the
plane perpendicular to the hole axis was found to be
0.6 mm (std=0.4 mm).
In the second experiment, a test bench was
designed and implemented, which allowed rotation
and tilt of the test subject, as shown in Figure 7. The
nail was inserted tightly into the plastic bone and
was locked proximally. The plastic bone together
with the nail was then fixed to the test bench. A
dynamic reference base was fixed to the bone to
establish a local coordinate system. The ground
truths of the direction of the nail axis as well as the
positions of the centers of the DLHs and the
directions of the axes of the DLHs were obtained
from a registration-free 3D-navigation system [4]
using the SIREMOBIL ISO-C
3D
Carm.
The reference position (rotation = 0
o
, tilt = 0
o
)
was obtained using a try-and-move method until the
projections of both holes appeared perfectly circular.
We then tilted the test subject with an interval of 5
o
until 25
o
. At each tilted position, we rotated the test
subject with an interval of 5
o
until 25
o
, which results
in totally 6x6 = 36 configurations. For each
configuration (tilt, rotation), a lateral-medial image
was acquired.
We applied the present approach to these 36
images. For each image, we compared the estimated
results to the ground truths. We computed the
angular error of the estimated nail axis and the
angular errors of the estimated axes of the DLHs.
And to get a clear idea how the positional errors
were distributed, we decomposed the positional
errors along the three orthogonal directions, i.e., the
nail axis direction, the distal locking hole axis
PRECISE APPROACH FOR RECOVERING POSES OF DISTAL LOCKING HOLES FROM SINGLE CALIBRATED
X-RAY IMAGE FOR COMPUTER-ASSISTED INTRAMEDULLARY NAILING OF FEMORAL SHAFT FRACTURES
125