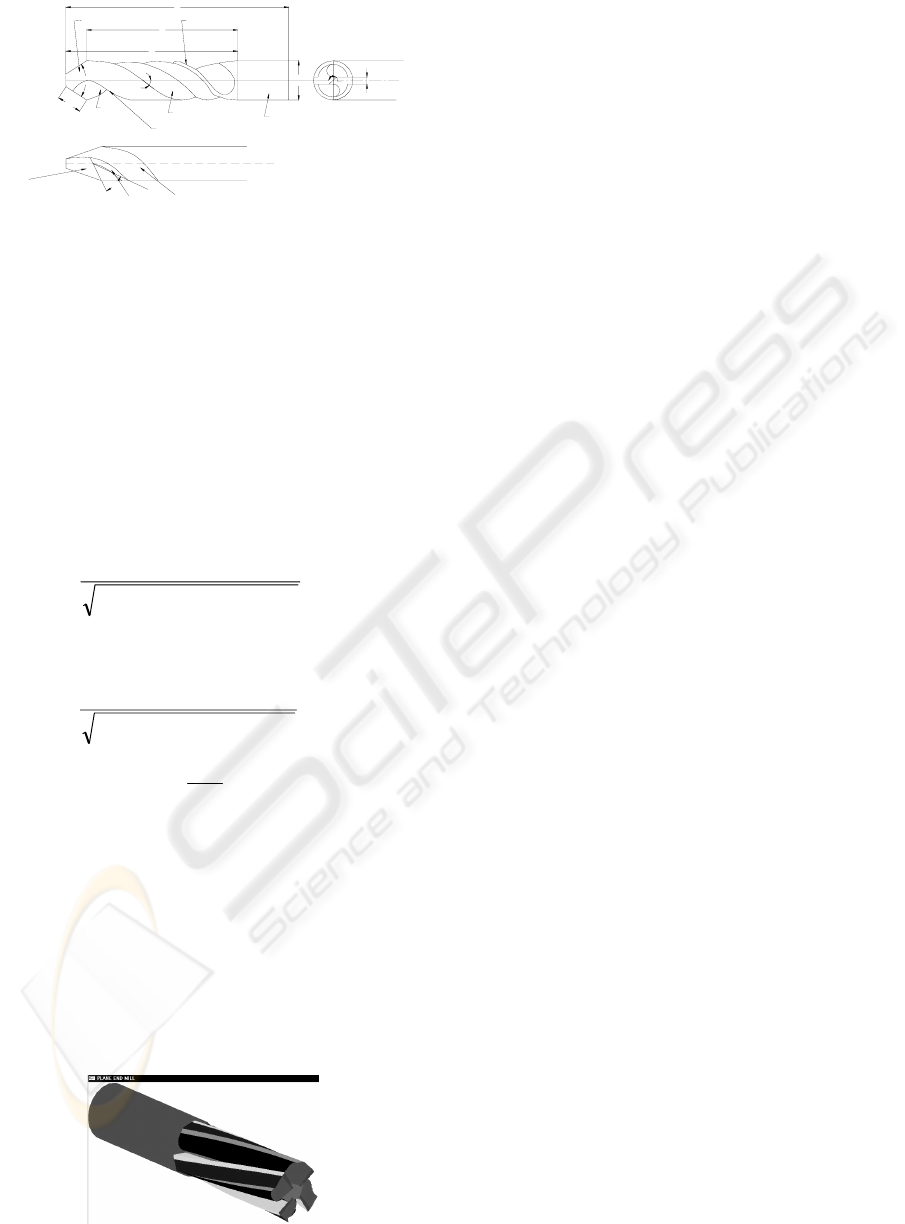
L
L
L
D
S
W
Land
Shank
Flute
Face
Body
2
β
Minor cutting edge
Major flank
λ
ψ
Flute
Land
Lip relief angle
α
4
2
1
Figure 5: 2D Projected Geometry of a Twist Drill.
The sectional geometry of the fluted shank has
three segments, out of which one is a straight line
and forms land (Σ
2
). The other two segments are
circular in geometry and on sweeping form flank
(Σ
3
) and face (Σ
1
) respectively. The drill end is made
of as many surface patches as the number of flutes.
For a two-flute drill, two surface patches form the
drill end. They are labeled as Σ
4
and Σ
5
and known
as lip relief surfaces. The lip relief surfaces can be
planar, cylindrical, conical and helicoidal. For a
drill, the forward mapping relations are:
Half Point Angle,
⎥
⎥
⎦
⎤
⎢
⎢
⎣
⎡
+
=
−
4
2
4
2
4
2
44
1
coscossin
cossin
cos
βγβ
γβ
β
(3)
Chisel Edge Angle, ψ = 90˚ - γ
4
. (4)
Relief Angle,
⎥
⎥
⎦
⎤
⎢
⎢
⎣
⎡
+
=
−
4
2
4
2
4
2
4
1
cossinsin
cos
cos
βγβ
β
α
(5)
Helix Angle,
⎟
⎟
⎠
⎞
⎜
⎜
⎝
⎛
=
−
c
D
P
π
λ
1
tan (6)
Peripheral Relief Angle, α
p
= γ
2
(7)
5 VALIDATION
This section presents an example on 3D modeling of
an end mill. The parameters used to construct the
model of end mill are referred in ANSI/ASME
B94.19-1985 standards. The resultant cutter is
rendered (Figure 6) in OGL environment.
Figure 6: Rendering of an End Mill.
6 CONLUSIONS
The present work has covered the 3D modeling of
the multi-point fluted cutters (slab mills, end mill
and drills) by mathematically expressing the
geometry of the cutting tools in terms of various
biparametric surface patches. Four rotational angles
(γ
1
, γ
2
, γ
3
, γ
4
) are used to define the geometry of a
slab mill along with other dimensional parameters.
Similarly, four rotational angles (γ
1
, γ
2
, γ
3
, α
7
) and
three rotational angles (γ
2
, β
4
, γ
4
) are defined to
model an end mill and drill respectively. The
mathematical definitions of the surfaces have been
used to obtain the standard 2D tool angles from
these proposed rotational angles. The inverse
relationships to obtain the rotational angles from the
conventional angles are also obtained. The entire
exercise attempts to recast the method of defining a
cutting tool in terms of 3D geometric models.
REFERENCES
Armarego, E.J.A., Kang; D.,1998. Computer-Aided
Modeling of the Fluting Process for Twist Drill
Design and Manufacture, Annals of the CIRP, Vol.47,
No.1, pp. 259-264.
Chen, C.-K., Lin, R.-Y., 2001. A Study of Manufacturing
Models for Ball-End Type Rotating Cutters with
Constant Pitch Helical Grooves, International Journal
of Advanced Manufacturing Technology, Vol.18,
No.3, pp. 157-167.
Drodza, T.J., Wick, C., 1983. Tool and Manufacturing
Engineers Handbook, Volume I - Machining, Society
of Manufacturing Engineers, Dearborn, MI.
Hsieh, J.F., Lin, P.D., 2002. Mathematical Model of
Multiflute Drill Point, International Journal of
Machine Tool & Manufacture, Vol.42, pp. 1181-1193.
Sheth, D.S., Malkin, S., 1990. CAD/CAM for Geometry
and Process Analysis of Helical Groove Machining,
Annals of the CIRP, Vol.39, No.1, pp. 129-132.
Tandon Puneet, Gupta P., Dhande S.G., 2004. Geometric
Modeling of Slab Mills, Proceeding of International
CAD conference - CAD'04, Thailand.
Tandon Puneet, Gupta P., Dhande S.G., 2005. Geometric
Modeling of End Mills, Computer Aided Design and
Applications, Vol. 2, Nos. 1-4, pp.57-66.
Wang, G.C., Fuh, K.H., Yan, B.H., 2001. A new
mathematical model for Multifacet Drills derived by
using Angle-Solid Model, International Journal of
Machine Tool & Manufacture, Vol. 41, pp. 103-132.
SURFACE MODELING OF MULTI-POINT, MULTI-FLUTE CUTTING TOOLS
175