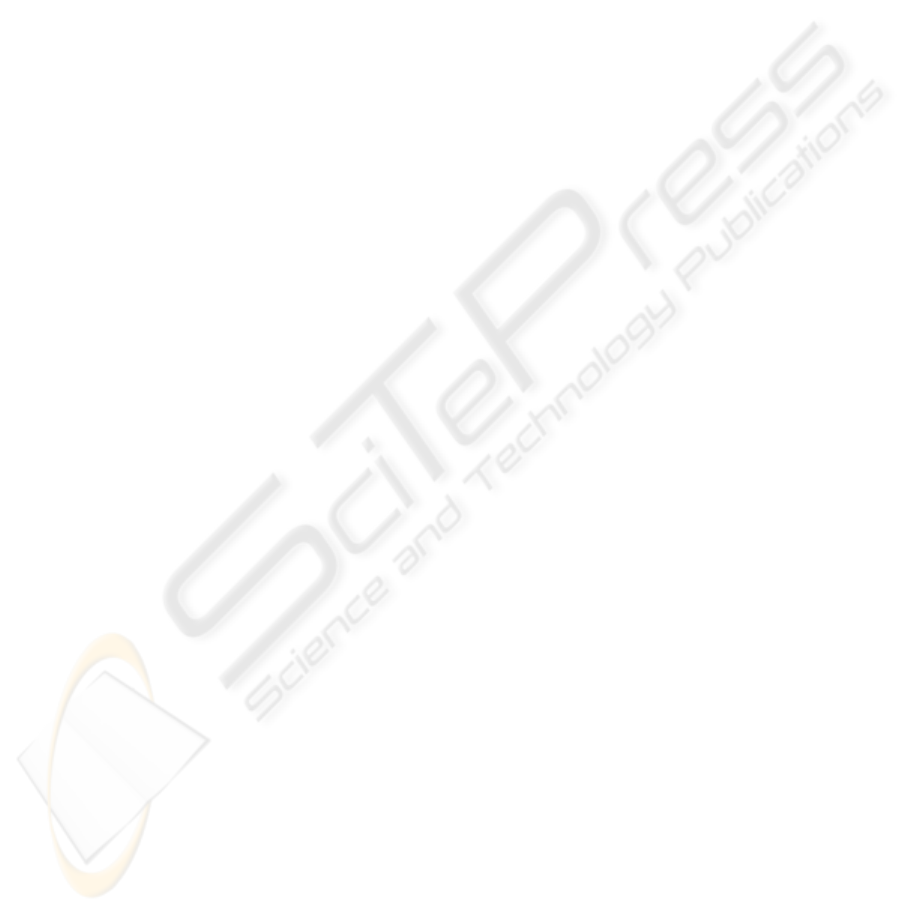
architecture compatible microprocessor and an AD
converter (nordicsemi, 2006).
The transceiver consists of a frequency
synthesizer, power amplifier, modulator and receiver
unit. It operates in the 433/868/915 MHz ISM bands
with adjustable frequency and output power. GFSK
(Gaussian Frequency Shift Keying) modulation is
used for the transmission, featuring a lower
bandwidth than conventional frequency modulation.
The modulation width is ±50 kHz. The data are
internally coded/decoded according to Manchester
code, resulting in 50 kb/s effective transmission
speed. The transceiver communicates with the built
in microprocessor through an internal SPI interface.
Three operating modes are available in the
transceiver: standby, transmission and reception.
The AD converter in this circuit has 4 inputs
and 10 bits. The inputs can be operated as
differential and the supply voltage can be measured
internally. Resolution can be adjusted in 4 steps
from 6 to 12 bits. The internal SPI interface is used
for A/D converter control just like the transceiver.
The circuit also has an input for AD converter
reference voltage. Alternately it is possible to use the
internal 1.22 V reference source. It is further
possible (when the external input is left free) to
measure the circuit supply voltage. In this case,
internal reference is used and 1/3 of the supply
voltage is measured. Conversion time is 8 to 14 μs,
depending on resolution.
As further hardware the circuit contains a single
channel PWM modulator, controlled by PWMCON
and PWMDUTY registers. Further the Watchdog,
Wakeup timer and low power consumption clock
pulse source. The watchdog timer is a 16 bit counter
serving to reset the microprocessor in case of an
error or endless loop in the program. The Wakeup
timer serves for interrupt or finish of some of the
economy modes. It is a 24 bit counter with
automatic fresh value recording, calling the required
operation upon reaching.
The main microprocessor. The microprocessor is
8051 architecture compatible. It includes 4 kB
program memory, 256 bytes of data memory and
special function registers. The upper 128 bits are
accessible by indirect addressing since they are
shared with special function register addresses. The
program memory is a RAM type and the program is
recorded in it by the Bootloader after SPI from the
EEPROM memory after resetting. A header must be
present in front of the program in the memory,
containing the memory speed, crystal frequency and
user data.
An ATMEL 89S8253 type was selected as the
control processor. It is a 8051 architecture
compatible microprocessor, containing additional
2 kB data EEPROM, 12 kB FLASH program
memory, SPI interface and further hardware. Both
the program and data memories are In System
Programmable (ISP), by series programming
through the included SPI interface. Further the
circuit contains a 256 byte ARM memory, whose
upper 128 bits are accessible by indirect addressing
since they are shared with SFR special function
register addresses. The lower 32 bytes of RAM are
four register banks. Instructions are fully compatible
with the 8051 architecture and operate identically
(atmel, 2006). The instruction timing is the same as
in the preceding case.
The sensors. The DS620 sensor as example can be
used for the measurement of temperature. The
circuit contains a temperature sensor, A/D converter,
comparator and a series interface. It does not need
any external components for its operation (
DS620,
2006)
. The temperature measurement range is -55
0
C
to +125
0
C. The A/D converter resolution can be
adjusted from 10 to 13 bits, corresponding to 0.5
0
C
to 0.0625
0
C resolution. The conversion duration
depends on resolution and takes between 25 ms and
200 ms. A twin lead I
2
C bus is used for
communication. The SCL terminal serves for
reception of clock pulses and the SDA terminal for
data reception or transmission. The circuit also
contains an EEPROM memory to which a part of
registers can be copied and so preserve the setting
even when the power supply is disconnected.
The real time circuit. DS1302 is a real time circuit,
counting seconds, minutes, hours, day of the week
and date including the year. For its operation the
circuit needs only an external crystal with 32768 Hz
frequency and an optional battery for continuing
function even when the primary power supply is
switched off. The circuit also contains 31 bytes of
user RAM memory, supported by the secondary
supply voltage (
DS1302, 2006).
3 SENSOR SYSTEM CONCEPT
The suggested wireless thermostat consists of
several parts. The control unit is the basic part,
securing communication with the user by means of
the display and keyboard. The unit communicates
with wireless temperature sensors and wireless
switch units. It is provided with custom-set
programs “temperature intervals”, controlling the
whole system. Second part of the system is
represented by the wireless temperature sensors. The
sensors are placed in required localities. The sensors
WINSYS 2007 - International Conference on Wireless Information Networks and Systems
40