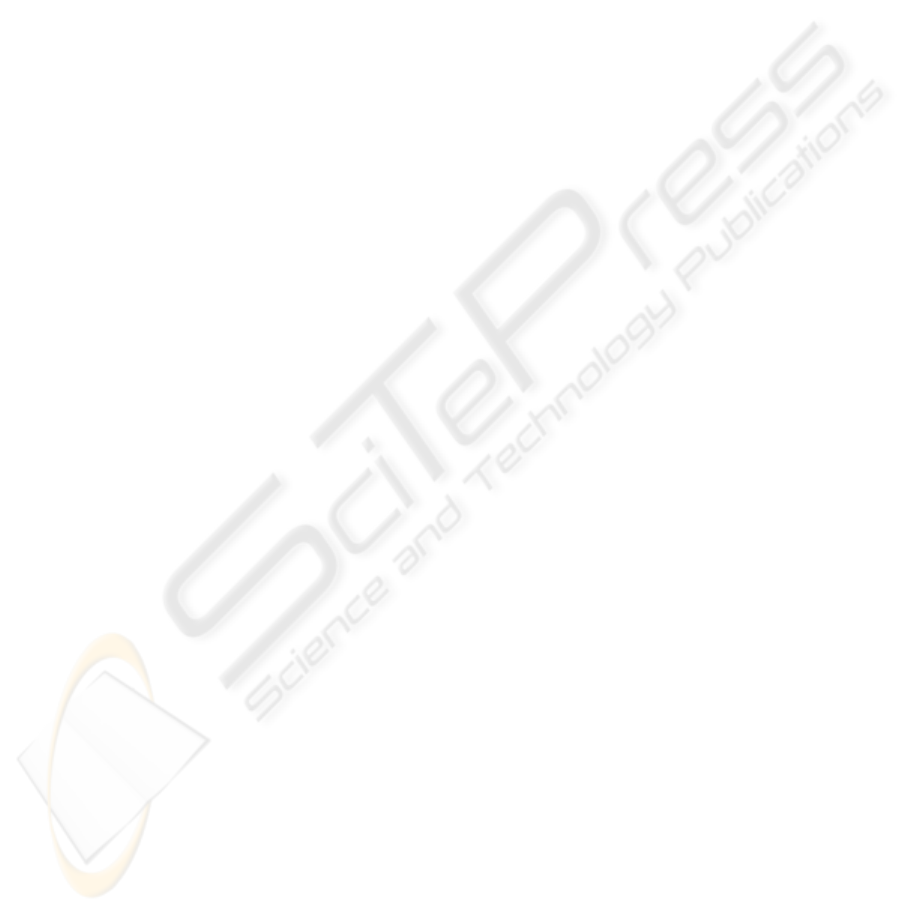
sequential machining order, process parameters,
processing time and maximum power requirements
on the machine tool.
4 CONCLUSION
This paper discusses development of a Decision
Support system required for a generative computer
aided process planning system for axisymmetric
components. A decision support system performs
tasks of input data interpretation, stock
determination, setup planning, sequencing of
operations in each setup, selection of process
parameters, determination of part processing time
and power requirements. Some of the tasks, such as
setup planning and establishing operations sequence,
are semi-structured in nature and can be performed
using rule-based approach of the decision support
system. The proposed system generates and reports
decision support system required for process plan
outlining machining sequence, machining
parameters, machining time, and power required.
REFERENCES
Chang T.C., 1990, Expert Process Planning For
Manufacturing, Prentice Hall , Englewood, N.J.
Chang, T.C., and Wysk, R.A., 1985, An Introduction to
Automated Process Planning Systems, Prentice Hall,
Englewood, N.J
Link, C.H., 1976, “CAPP, CAM-I Automated Process
Planning System”, Proceedings of the 1976 NC
Conference, CAM - I Inc. Arlington, Texas, USA.
Chitta, A.K., Shankar, K., and Jain, V.K., 1990, “A
Decision Support System for Process Planning”,
Computers in Industry, 14, pp. 307 – 318.
Grabowik, C., and Knosals, R., 2003, “The Method of
Knowledge Representation for a CAPP System”,
Journal of Materials Processing Technology, 133, pp.
90-98.
Younis, M.A., and Wahab, Abdel, 1997, “A CAPP Expert
System for Rotational Components”, Computers and
Industrial Engineering, 33(3-4), pp. 509-512.
Mahadevan, K., and Reddy, K.B., 1983, Design Data
Handbook For Mechanical Engineers, CBS Publishers
& Distributors, Delhi.
Jasthi, S.R.K., Rao, P.N., and Tewari, N.K., 1995,
“Studies on Process Plan Representation in CAPP
System”, Computer Integrated Manufacturing
Systems, 8(3), pp. 173–184.
Kovan, V., 1959, Fundamentals of Process Engineering,
Foreign Language Publishing House, Moscow.
Huang, S.H., Zhang, H.C., and Oldham, W.J.B., 1997,
“Tolerance Analysis for Setup Planning: A Graph
Theoretical Approach”, International Journal of
Production Research, 35(4), pp.1107–1124.
Hinduja, S., and Huang, H., 1989, “OP – Plan: An
Automated Operation Planning for Turned
Components”, Proceedings of Institution of
Mechanical Engineers, 203, pp. 145-157.
ASM Metals Handbook – Machining, (1997), 9
th
Edition,
Volume 16, Materials Park, USA.
Metcut Machining Data Handbook, (1980), 3
rd
edition,
Metcut Research Association Inc., Machinability Data
Center, USA.
ICEIS 2007 - International Conference on Enterprise Information Systems
394