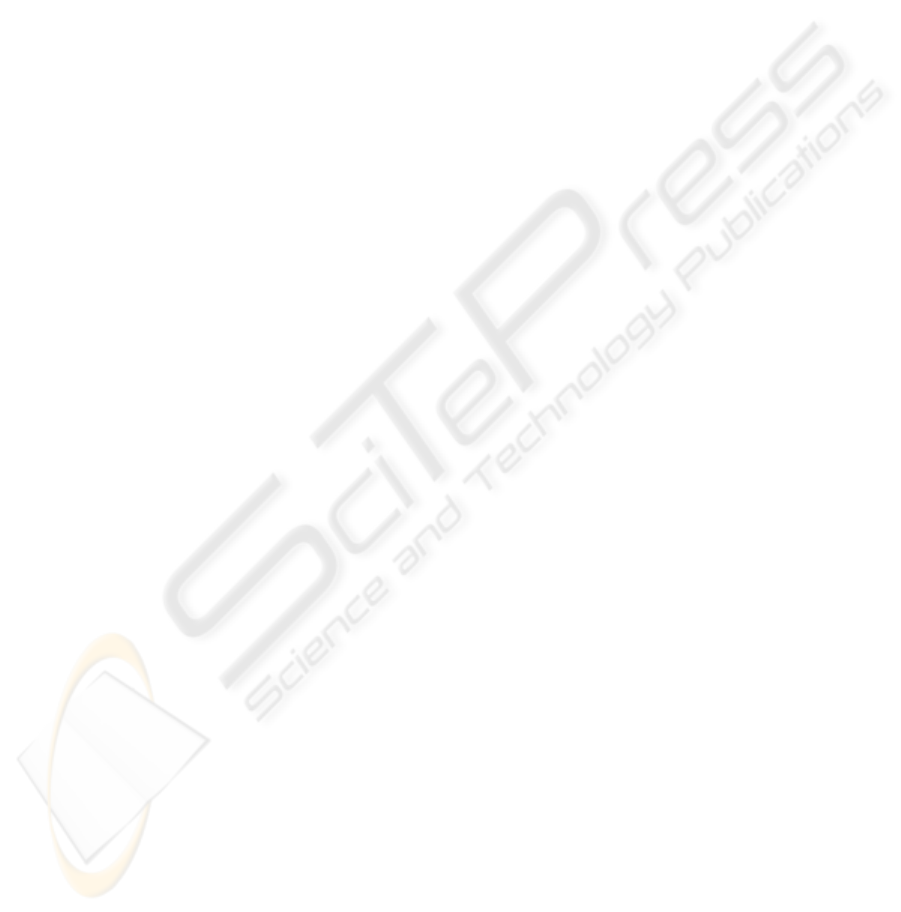
could be made. In Japanese corporate culture a new
proposal must go through multiple levels before
making any decision. Therefore, decision making
process is a slow process. However, once a formal
decision has been made the action are taken very
quickly and collectively without any delay,
objections or hesitations, because all management
levels from bottom to up have been involved from
the beginning. On the other hand, in Western Europe
corporate culture oral discussion is allowed, and
decision-making process does not follow a bottom-
up structure, thus it is made faster.
Moreover, in Japanese culture more commitment
is given for operational excellence where making
mistakes is extremely not acceptable action.
Therefore high-ranking Japanese managers spent too
much time apologizing for service failures and
focused less on planning. On the other hand, in
European corporate culture accept that humans can
make mistakes, thus allowed to argue with
customers. The interviews also revealed that
European managers did not fully understand the
ultimate payoff of the Japanese service strategy.
Hence, applying the Japanese logistics within
Western firms is a difficult task with continues exit
of cultural differences, and absence of compatibility.
In this case corporate culture is mediating the SC’s
performance, thus cultural differences has more
impact than the PeCC case.
4 CONCLUSION
In summary, this research article contends that the
value and relative importance of corporate culture
and strategic alliances have changed, as we migrate
from the traditional SCM approach to the e-SCM
perspective. Hence, this research suggests that
corporate culture is less effective when managing
cultural differences on e-SC environment. The
rationale behind this proposition is that the Internet
and electronic commerce, combined with supply
chain-related opportunities, have given way to an
environment where the benefits of both the dynamic
e-SC structure to form inter-organizational relations
and the traditional SCM philosophy can be jointly
realized. The focus on corporate culture also
provides management with a guideline for assessing
potential cultural changes necessary to reap fully the
benefits of operating in the e-SCM environment.
The proposed structure of e-SC partnerships and
alliances provides a framework for further research
into SC relationships, and ultimately the ever-
changing and dynamic e-SC environment. The next
step in the process of researching partnerships and
alliances, as well as corporate culture, in e-supply
chains is empirically to test the propositions
developed in this article. Such tests will allow for
increased academic knowledge on the impact of the
corporate culture on the management of SC
organizations with a better understanding of the
cultural changes necessary to manage the e-SC
organization effective. Overall, this research
contributes to the understanding of the dynamic and
volatile electronic commerce marketplace by
focusing on the corporate culture differences’
management necessary in this environment
REFERENCES
Bucklin, L. P. and Sengupta, S. (1993), Organizational
Successful Co-Marketing Alliances. Journal of
Marketing, 57, 32-46.
Cooper, M. C., Lambert, D. M. and Pugh, J. D. (1997),
Supply Chain Management: more than a new name for
logistics. The International Journal of Logistics
Management, 8, 1-14.
Ellram, L. M. and Cooper, M. C. (1990), Supply Chain
Management: Partnership and the Shipper-Third Party
relationship. The International Journal of Logistics
Management, 1, 1-10.
Handfield, R. B. and Nicholas, E. L. (1999) Introduction
to supply chain management, Prentice Hall Press.
Lambert, D., Stock, J. R. and Ellram, L. M. (1998)
Fundamentals of Logistics Management, McGraw-
Hill, Boston, MA.
Lee, H. L. and Whang, S. (2000), Information Sharing in
Supply Chain. International Journal of Technology
Management, 20, 373 - 387.
More, E. and McGrath, M. (2002), An Australian Case in
e-Health communication and Change. Journal of
Management Development, 21, 621-632.
Novack, R. A., C. John Langley, J. and Rinehart , L. M., ,
(1995) Creating Logistics Value, Council of Logistics
Management, Oak Brook, IL.
Smagalla, D. (2004), Supply Chain Culture Clash. MIT
Sloan Management Review, 46 (1).
Schein, E. (1990), Organizational Culture. American
Psychologist, 45, 109-119.
Tyndall, G., Gopal, C., Partsch, W. and Kamauff, J.
(1998) Super-charging Supply Chains: New Ways to
Increase Value Through Global Operational
Excellence, John Wiley & Sons, New York, NY.
Williams, L. R., Esper, T. L. and Ozment, J. (2002), The
Electronic Supply Chain: Its impact on the current and
future structure of strategic alliances, partnerships and
logistics leadership. International Journal of Physical
Distribution & Logistics Management, 32 (8), 703-
719.
ICEIS 2007 - International Conference on Enterprise Information Systems
282