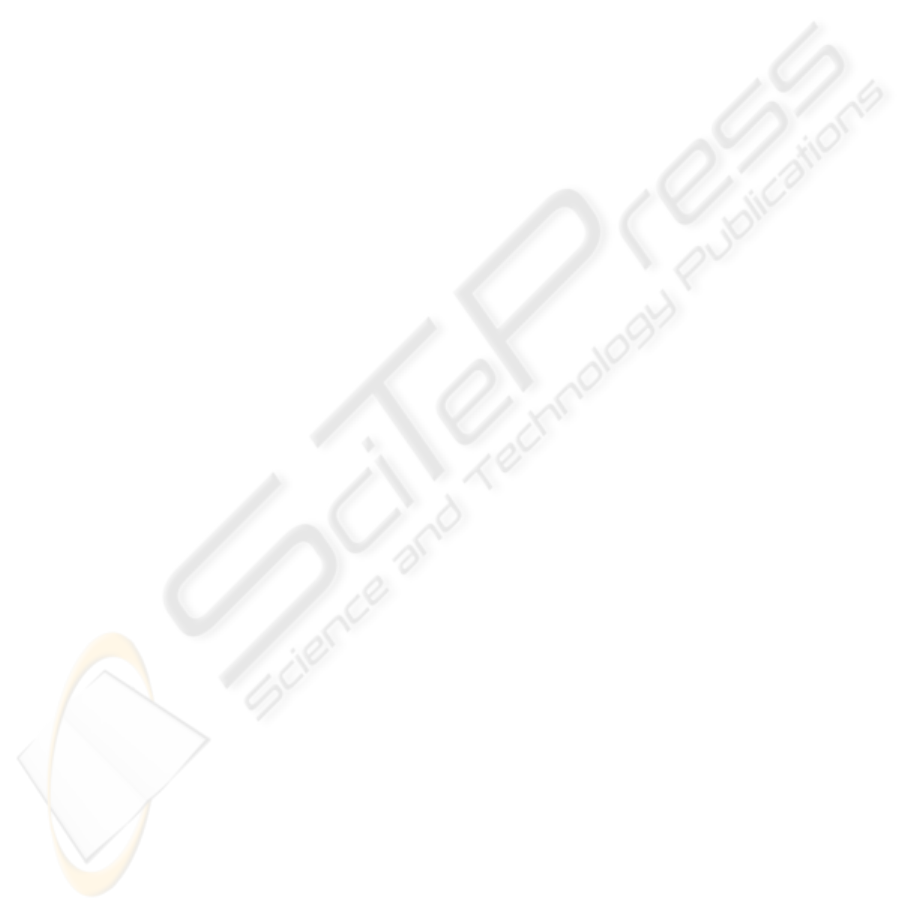
within different car companies and other content
providers. This heterogeneity requires a well-defined,
standardized MYCAREVENT data model that is flex-
ible, adaptable and implemented across the differ-
ent content providers. The data model, developed
within the project, is a meta model; it describes the
data and extends it with uniform properties to make
it accessible and analysable by a wide variety of ad-
vanced search mechanisms, like Ontologies ((Bryan
and Wright, 2005)) or Expert systems. This approach
permits leaving the original content provider/OEM
data largely untouched, having in mind that forcing a
change of existing data provider structures easily can
incur unpredictable costs as it targets related author-
ing systems and processes.
The data model concept described in the previ-
ous paragraph forms the basis for the message for-
mat that is defined to enable standardized communi-
cation between the various components and services.
The flow of information and the order of interaction
between the end-user and the system are laid down
by the generic workflow steps. Communication links
are established over the standard Internet protocol:
SOAP envelopes are used to circulate generic XML
messages over HTTP. Identical web service interfaces
are implemented on top of every component. Using
the Internet for communicating offers advantages re-
garding mobility, adaptivity, ubiquity and extensibil-
ity. Nevertheless the use of an open media requires
a secure and authenticated communication channel,
e.g. via VPN-routers as a cost-efficient and well-
established industrial standard.
The web service interfaces, the standardized mes-
saging and the generic workflow are the three basic
elements for communication between previously iso-
lated entities. Due to these elements, it is clear and
well defined respectively how to communicate, what
to communicate and in which order to communicate.
Three main parts constitute the infrastructure:
Mobile Clients (accessing the information), the Ser-
vice Portal (core of the infrastructure) and the Remote
Services (providing services or information). The Ser-
vice Portal is the core component that channels the
user demand through a single, comprehensive gate-
way. It covers flexible business rules and basic re-
quirements, such as user management, to enable a
wide variety of functionalities such as multi-language
search and diagnosis, information distribution, host-
ing and authoring of repair information. Eventu-
ally it makes centrally accessible the range of MY-
CAREVENT Remote Services.
Examples of services and content in the MY-
CAREVENT Mobile Service World are: Interactive
Circuit Diagrams to repair electronic components in
the car, Technical Tips about generally operated repa-
rations or fixes on specific car models, Electronic
Driver Manuals with animations and graphical data,
Diagnostic Services to analyse vehicle fault codes, an
Expert System to lead the user through the diagno-
sis of a car breakdown, Value Added Services for the
driver (infotainment, news, traffic information, simple
guided car reparations), an Advanced Query Service
for searching repair information by making use of on-
tologies.
The MYCAREVENT infrastructure offers multi-
ple benefits to the aftermarket. Services and content
from different companies and organisations are inte-
grated into a single service portal that is ‘always, ev-
erywhere and uniformly’ accessible on different mo-
bile devices. By its interoperability between different
providers, services that were previously stand-alone
entities can now be combined and amended with the
further information available in the infrastructure. It
brings vehicle information handling, gathering, main-
tenance and repair to a higher level of use; for exam-
ple, in the case of a breakdown, linking the fault code
of the car with simple self-repair instructions (movie,
pictures, etc.) ((Houben et al., 2005b)); or answer-
ing iterative hierarchical questions to an Expert Sys-
tem which eventually provides the most probable er-
ror and an advice whether it is safe to continuing driv-
ing or not.
On the repair level, independent workshops or
roadside assistance companies are able to easily ac-
cess OEM information, which allows them to per-
form even complex repairs. Repair and diagnosis pro-
cedures are speeded up, success rates are enhanced
while sharing infrastructure costs, resulting eventu-
ally in higher customer satisfaction. On the level of
information provision via the infrastructure; by pro-
viding different information from different resources,
it can be easily compared, in content and price.
3 SYSTEM ARCHITECTURE
In this section the architecture of the repair informa-
tion procurement framework is described. The basic
flow of information between mobile clients, the por-
tal and the remote services is defined as follows: the
client requests information from the portal, the portal
routes this request to the appropriate service(s), these
service(s) respond to the portal, which forwards the
response to the client. These workflow steps are elab-
orated in Section 3.2. The communication between
the components is supported by XML-based mes-
sages and corresponding web services. Web services
allow us to use the standard HTTP protocol without
A WEB-BASED CENTRAL GATEWAY INFRASTRUCTURE IN THE AUTOMOTIVE AFTER-SALES MARKET -
Business Interoperability through the Web
47