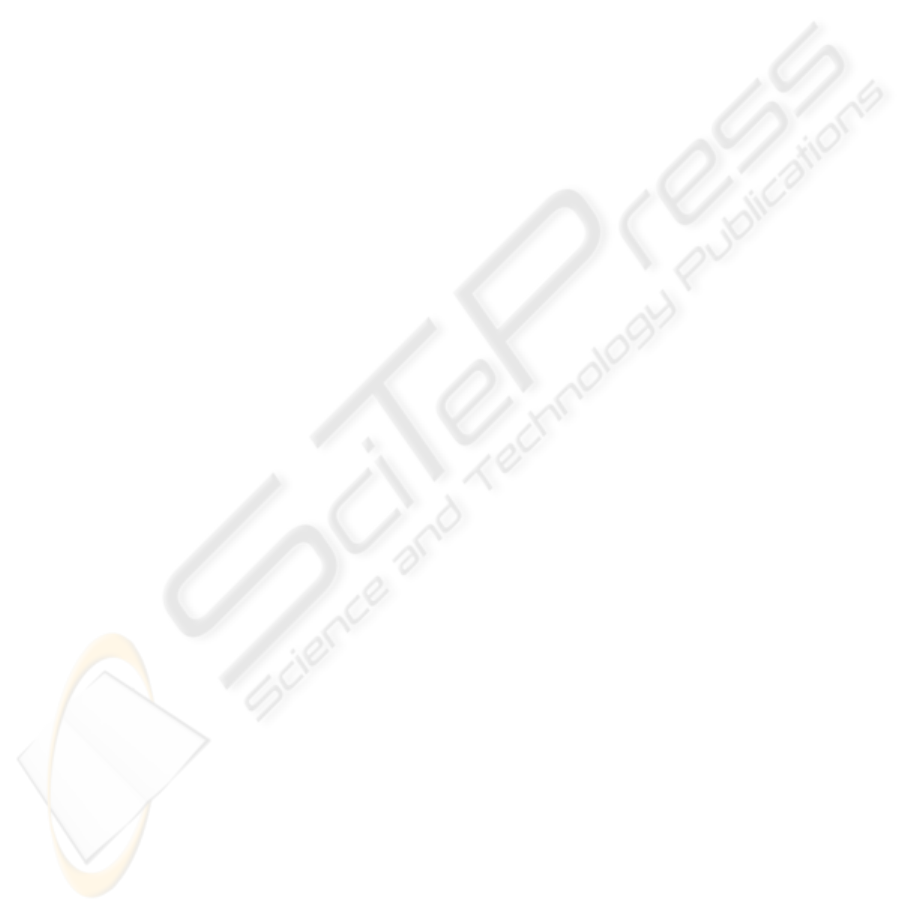
OOPUS generates a proposal of 134 to eliminate the
deficit.
Down in Figure 6 is the result after confirming the
proposal. By creating the new batch there are no
more deficits for the part number in the time from
2006-11-13 till 2006-11-17.
6 CONCLUSION
The software OOPUS, presented in this paper,
is used by an international automobile manufacturer
to plan and control his engine production in two
manufacturing plants. Thereby OOPUS replaced
different isolated applications to unite all aspects
needed for the production planning and control in
one application. Additionally OOPUS automated
many processes which where handled manually and
without IT support before.
OOPUS guarantees a higher planning reliability
by taking every required data into account to create a
production plan that is valid and efficient.
By using two integrated interfaces, the CQT and
the planning table, OOPUS guarantees maximum
information transparency. The user gets a
compressed, but complete overview of all the
relevant data he needs to plan and manipulate the
production plan. The CQT gives an overview of the
situation for the complete planning horizon by
comparing cumulative quantities based on customer
requests with cumulative quantities based on the
already produced parts and the planned parts of the
current plan. The planning table shows this plan and
offers many actions to change it manually, semi-
automatically or automatically. Every change of the
plan leads to a recalculation of the CQT, to ensure
that both interfaces always show the same updated
information.
This maximum information transparency leads to
a big saving of time for the production planner who
no longer needs to change between different
applications to create and control the production
plan.
OOPUS was developed based on the specific
requirements of an automobile manufacturer, so it is
integrated into the system architecture of this
customer. This leads to the idea of developing a
system called OOPUS-WEB which is a platform
independent web application and inherits the main
ideas of OOPUS. Therefore OOPUS-WEB can be
used by smaller companies as well as being
integrated into complex information system
infrastructures at large companies.
REFERENCES
Harjes, I.-M.; Bade, B.; Harzer, F., 2004.
Anlaufmanagement – Das Spannungsfeld im
Produktentstehungsprozess. In: Industrie
Management.
Holland, C., Light, B, 1999. A critical success factors
model for ERP implementation. In: IEEE Software,
vol. 16, no. 3.
Tempelmeier, H., 2006. Inventory Management in Supply
Networks. Problems, Models, Solutions. Books on
Demand GmbH, Norderstedt.
Stammen-Hegener, C., 2002. Simultane Losgrößen- und
Reihenfolgeplanung bei ein- und mehrstufiger
Fertigung. Dt. Univ.-Verl., Wiesbaden.
Katok, E.; Lewis, H. S.; Harrison, T. P., 1998. Lot sizing
in general assembly systems with setup costs, setup
times, and multiple constrained resources.
Management Science, no. 44.
Tempelmeier, H., 2003. Material-Logistik. Springer,
Berlin, 5
th
edition.
Maes, J., McClain, O.J., Van Wassenhove, L.N., 1991.
Multilevel capacitated lotsizing complexity and LP-
based heuristics. European Journal of Operational
Research, no. 53.
Wilson, James M., 2003. Gantt Charts: A Centenary
Appreciation. European Journal of Operational
Research 149, no. 2.
Schönsleben, P., 2004. Integrales Logistikmanagement -
Planung und Steuerung der umfassenden Supply
Chain. Springer, Berlin, 4
th
edition.
Kurbel, K., 2005. Produktionsplanung und -steuerung im
Enterprise Resource Planning und Supply Chain
Management. Oldenbourg Wissenschaftsverlag,
München.
Dangelmaier, W.; Henkel, S.; Holtkamp, R., 1997.
OOPUS - eine objektorientierte PPS-Plattform. In: wt
- Produktion und Management.
Dangelmaier, W.; Brockmann, K.; Hamady, M.;
Holtkamp, R.; Langemann, T., 1999. OOPUS-PSCM -
Ein Werkzeug zum Produktions- und Supply-Chain-
Management. In: Logistik Management: Intelligente I
+ K Technologien. Springer, Berlin.
Dangelmaier, W.; Holtkamp, R.; Hamady, M.;
Langemann, T.; Krebs, W., 1999. Produktions- und
Supply-Chain-Management bei größeren Stückzahlen.
In: PPS-Management.
Dangelmaier, W., Klöpper, B., Timm, T. Brüggemann, D.;
A Modelling Approach for Dynamic and Complex
Capacities in Production Control Systems, BIS 2007,
Lecture Notes of Computer Science 4439, pp. 626-
637, Springer Verlag, Berlin Heidelberg
ICEIS 2007 - International Conference on Enterprise Information Systems
430