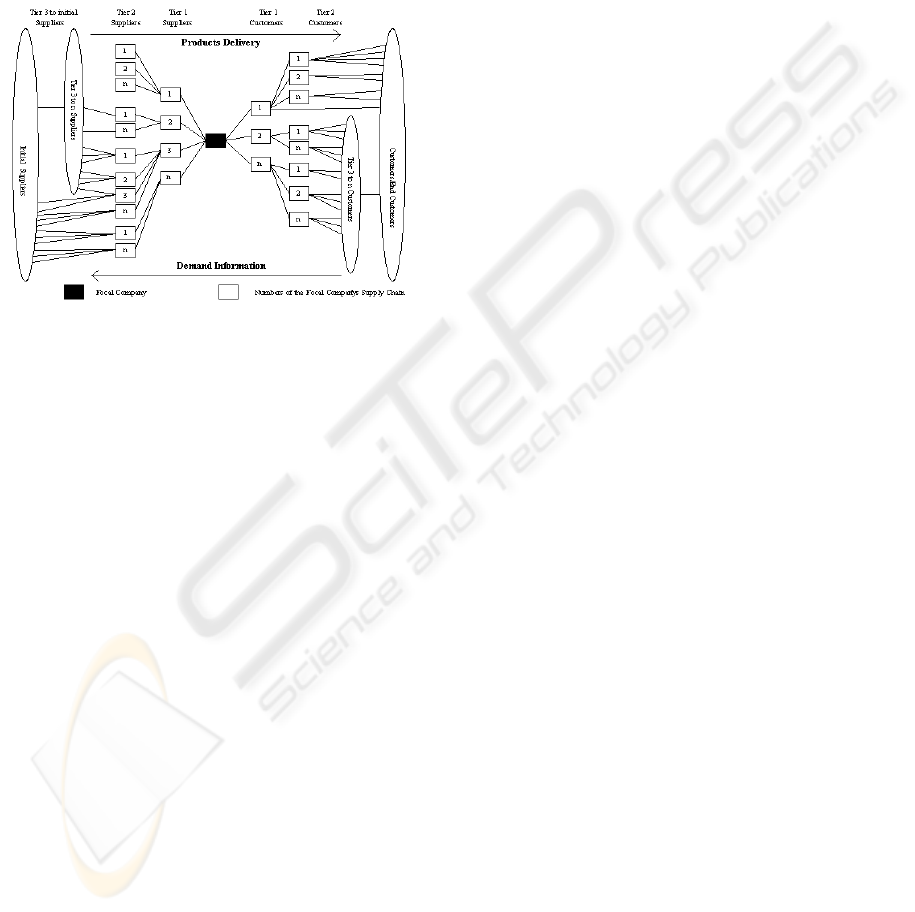
from supplier to customer. Judging the effectiveness
of supply chain management normally includes
monitoring delivery and order fulfillment
performance, production flexibility, warranty and
return’s processing costs, inventory and asset turns,
and other factors in evaluating the overall
performance of a supply chain (Poluha, 2006). To
achieve excellent supply chain management, it is
important to understand the supply network and its
detailed processes.
Figure 1: Structure of Supply Network (Lambert et al.,
1998).
A supply network as shown in Figure 1 consists
of a focal entity of a manufacturing company
networked by downstream entities of customers and
upstream entities of suppliers. In the current
information era, the supply network becomes more
complex and challenging when dealing with the
dynamics of upstream suppliers and highly uncertain
international markets’ demands. Therefore, the
supply chain management is seen as an information-
intensive process, where material/products delivery
and demands have to be effectively managed in
order to maintain supply chain’s visibility.
Because of the large amount of business data in
supply chain management, most companies
implement enterprise information systems such as
ERP, MRP or supply chain management modules to
improve supply chain workflow and efficiency.
However, these systems have not provided sufficient
impact on the effectiveness in the workflow, as two
influential functions, i.e., forecasting and inventory
management, play limited roles in the supply
network.
Forecasting concerns the issues such as how to
project historical data; how to deal with the change
of lead time; and how to recognise different demand
patterns regarding various components (Donald,
2003). Warwick Manufacturing Group (WMG, 2003)
points out that the critical reasons for failing in
getting quality forecasts are:
Fails to have a single formal forecast
process by all of the management and all the
parties;
Fails to monitor forecast accuracy
over different time periods and constantly
review the forecast as it changes from time to
time.
More often than not, in manufacturing business,
an ineffective forecast can cause a production plan
ending up with either pushing too much production
and excessive stock, or totally running out of
products.
Inventory is summarised by Richards (Richards,
1982) that time, discontinuity, uncertainty, and
economy feature in the existence of inventory.
Inventory is expected to work as a buffer between
supply and demand to minimise the risk of
investment. Therefore, there are problems
concerning what to stock, when to stock and how to
stock. It is no doubt that a holistic view over parts’
behaviour and aligning that with an appropriate
supply chain management strategy could take
inventory management into a more strategic level
and thereby enhance the effectiveness in setting
stock policies. However, some companies find that
this process, normally called inventory or stock
management, is complex in terms of the diversity of
parts and the time involved.
These limitations of the current common
approach to supply chain management may hinder a
company’s ability to achieve its business goals.
Consequently, companies may find themselves
losing their competitive advantages. Inspired by its
various experiences in tackling supply chain
management difficulties and issues, Orchestr8
realises that the traditional supply network needs to
be driven by real-time demand.
3 DEMAND DRIVEN SUPPLY
CHAIN MANAGEMENT
ARCHITECTURE
Demand driven supply network (DDSN) is a system
of coordinated technologies and processes that
senses and reacts to real-time demand signals across
a network of customers, suppliers, and employees. It
enables organisational efficiency, streamline new
product development and launch, and maximise
A DESIGN FOR BUSINESS INTELLIGENCE SERVICE IN DEMAND DRIVEN SUPPLY CHAIN MANAGEMENT
21