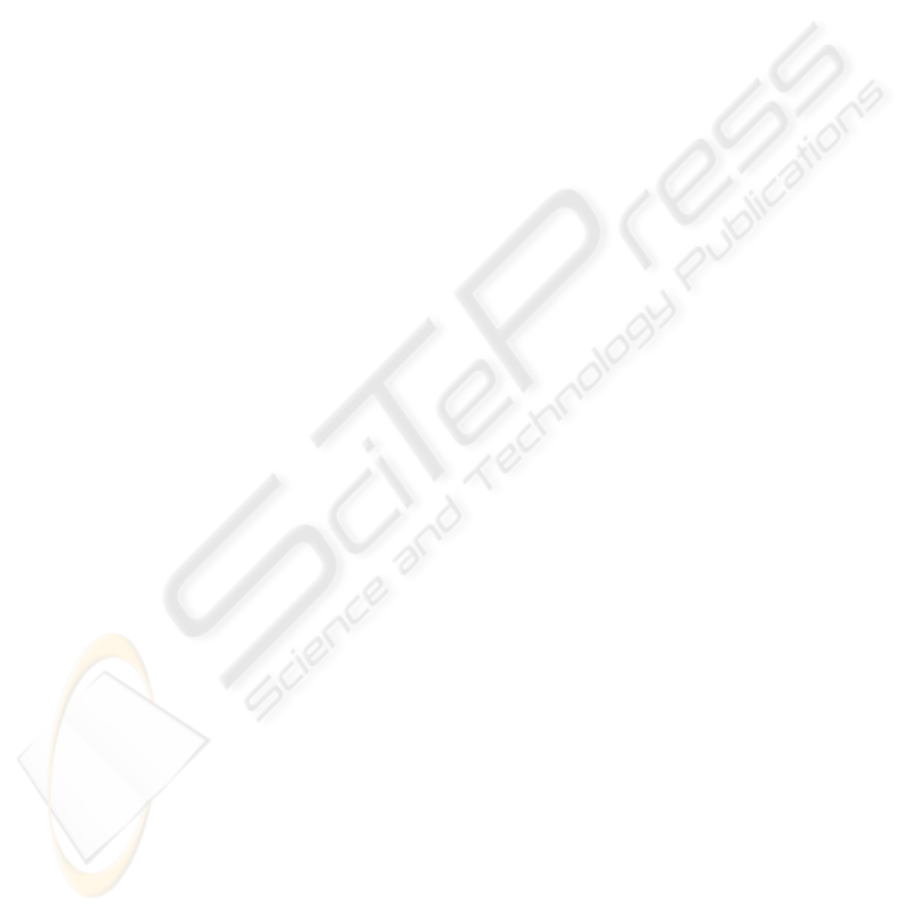
to cause failure. This paper also fails to recognise if a particular combination of
factors led to the ERP failure, for example, if the non achievement of two CSFs
together signifies failure.
This research would be validated further if the same conclusions were made by
considering the subject from a different perspective; possibly looking at the ERP
implementation from a user perspective, the Managing Director’s perspective or the
ERP vendor’s perspective.
References
1. Buckhout S, Frey E and Nemec J, ‘Making ERP Succeed: Turning Fear into Promise’,
IEEE Engineering Management Review, Second Quarter, 1999, pp116-123.
2. Davenport T H, ‘Putting the Enterprise Back into the Enterprise System’, Harvard Business
Review, July-August 1998, pp121-131.
3. Gargeya V B and Brady C, ‘Success and Failure factors of adopting SAP in ERP System
Implementation’, Business Process Management Journal, Volume 11, No 5, 2005, pp 501-
516.
4. Ho C F, Wu W H and Tai Y M, ‘Strategies for the Adaptation of ERP systems’, Industrial
Management and Data Systems, Vol 104, No 3, 2004, pp 234-251.
5. Holland C P and Light B, ‘A Critical Success Factors Model for ERP Implementation’,
IEEE Software, May-June 1999, pp 30-36.
6. Kansel V, ‘Enterprise Resource Planning Implementation: A Case Study’, The Journal of
American Academy of Business, Cambridge, Vol 9, No 1, March 2006, pp165-170.
7. Kim Y, Lee Z and Gosain S, ‘Impediments to successful ERP implementation process’,
Business Process Management Journal, Vol 11, No 2, 2005, pp 158-170.
8. Laudon KC and Laudon J P, ‘Management Information Systems’, Pearson Education, New
Jersey, 2006.
9. Loh T C and Koh S C L, ‘Critical Elements for a Successful Enterprise Resource Planning
Implementation in Small and Medium Sized Enterprises, International Journal of
Production Research, Volume 4, 17 September 2004, pp 3433-3455.
10. Markus M L and Tanis C, ‘The Enterprise System Enterprise – From Adoption to Success’,
in R W Zmund, ‘Framing the Domains of IT Research’, Pinnaflex Educational Resources,
2000, pp173-207.
11. Nah F F and Lau J L S, ‘Critical Factors for Successful Implementation of Enterprise
Systems’, Business Process Management Journal, Vol 7, no 3, 2001 pp 285-296.
12. Parr A and Shanks G, ‘A Model ERP project Implementation’, Journal of Information
Technology, Vol 15, 200, pp289-303.
13. Ross J W, ‘Surprising Facts about implementing ERP’, IT Professional, Vol 1, No 4, 1999,
pp 65-68.
14. Soh C, Kien S S and Tay-Yap, ‘Cultural Fits and Misfits: Is ERP a Universal Solution’,
Communications of the ACM, Vol 41, No 4, April 2000, pp 47-51.
15. Somers T M and Nelson K, ‘ The Impact of Critical Success Factors across the Stages of
Enterprise Resource Planning Implementations’, Proceedings of the 34
th
Hawaii
International Conference on System Sciences, January 3-6 2001.
16. Taube L R and Gargeya V B, ‘An Analysis of ERP System Implementation’, The Business
Review Cambridge, Vol 4, No 1, Summer 2005, pp 1-6.
17. Umble E J, Haft R R, Umble M M, ‘Enterprise Resource Planning: Implementation
Procedures and Critical Success Factors’, European Journal of Operational Research,
Volume 146, 2003, pp 241-257.
63