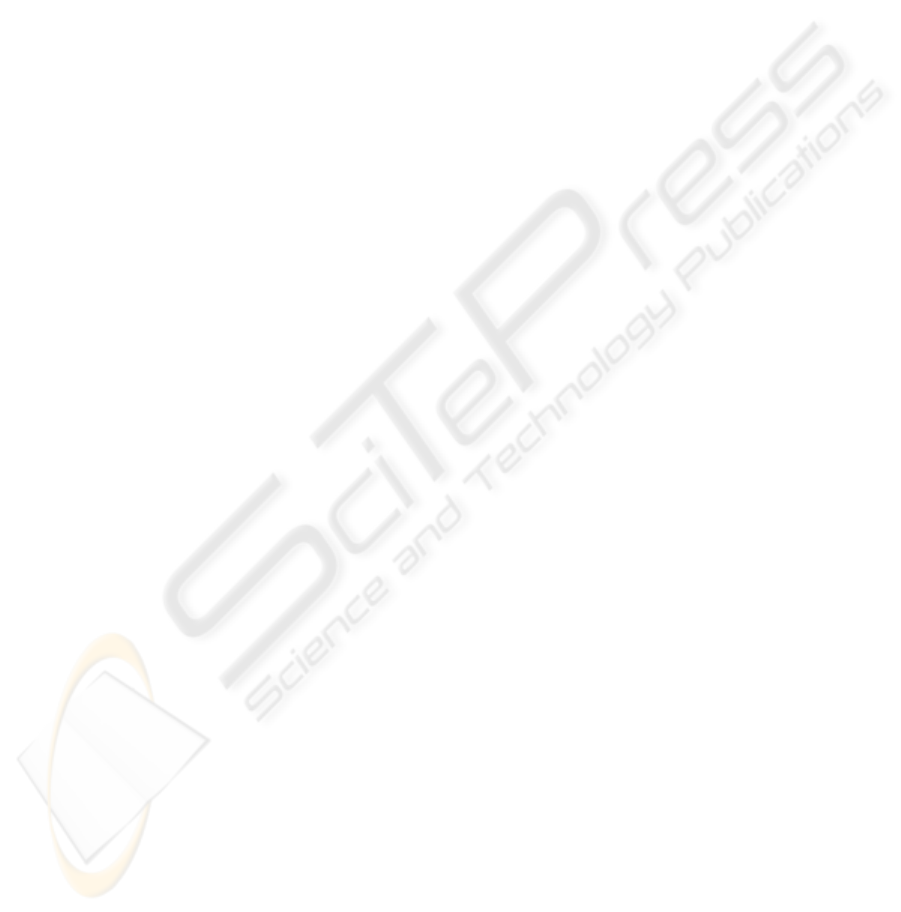
and poly-methylmethacrylate (PMMA) has
increased over the past few years. PDMS has been
widely discussed due to good optical transparency
for detection, to cure at low temperatures, easily
replicates molding and good adhesion. Many PDMS
applications in CE microchip and microfluidic
channel design have been reported. This study
utilized PDMS as a substrate for formulating the
twisted CE microchannel for CE-AD microchip
device. As previously reported, a 3-microelectrode
system was fabricated on a glass substrate using bare
indium tin oxide (ITO) and Prussian blue (PB) as
catalyst on the working electrode.
2 EXPERIMENTAL
2.1 Materials and Chemicals
The chemicals used for PB electroplating solution
were composed of ferric chloride hexahydrate
(97%), potassium ferricyanide (99%), potassium
chloride, and hydrochloride acid (32%). The testing
analyte bisphenol A (BPA) was supplied by Wako.
All of which were diluted to get the desired
concentrations. Reagents used for microchannels
include Sylgard 184 PDMS from Dow Corning
Corp. (Midland, MI, USA). In order to mold PDMS
microchannels, negative photoresist SU-8 and XP
SU-8 developer from MicroChem Company were
used. Throughout the study, deionized water (DIW)
was used.
2.2 Microchip Fabrication
Figure 1 shows the simple process flow diagram for
the fabrication of the CE/ECD microchip. For the
electrodes in CE/ECD system, the ITO layer was
deposited on a glass substrate by R.F. magnetron
sputtering system. The thickness of the ITO film is
3400 Å. The 1.8 µm thick photoresist (AZ1512) was
spin-coated on the ITO-coated glass and patterned
for ITO electrodes. The sputter deposited ITO layer
was etched with FeCl
3
/HCl solution. In order to
avoid the interference of a high electric field with
EC detection, one decoupling-ground electrode as
the cathode of CE electric field was positioned in
front of the three-electrode electrochemical system.
The PB film was electrodeposited on the working
electrode. Electroplating solution is consisted of 20
mM FeCl3, 20 mM K
3
[Fe(CN)
6
], 0.2 M KCl and 0.1
M HCl. All the PB electrode surfaces were cleaned
with acetone and dried with N
2
gas. In order to
fabricate microchannels, 40 µm thick photoresist
(SU-8) was spin-coated and patterned on the silicon
wafer. The height of the positive patterns on the
moulding masters, which is equal to the channels
depth created on the PDMS layer, was 40 µm when
measured with a surface profiler. The PDMS layers
were fabricated by pouring a degassed mixture of
Sylgard 184 silicone elastomer and curing agent
(10:1) onto a molding master, followed by curing for
at least 1 hour at 72 °C. The cured PDMS was
separated from the mold, and reservoirs were made
at the end of each channel using a 3 mm circular
punch. The channel width is 80 µm. The double-T
injector channel had an offset of 170 µm with 5 cm
long separation channels and 1 cm long injection
channel. Also, the channel width is 80 µm. The
twisted injector channel had an offset of 170 µm
with 7 cm long separation channels and 1 cm long
injection channel. Before bonding the PDMS layer
to ITO-coated glass substrate containing the
electrodes, the two components were UV-Ozone
exposed to improve their bonding strengths.
2.3 Microchip Configuration
The microchip consists of four reservoirs and micro-
channels from PDMS (Fig. 2(a)), three electrodes
and electrodes for applying injection / separation
electric field on the glass substrate (Fig. 2(b)). The
width of the working electrode (W) is 100 µm, 50
µm for reference electrode (R) and 200 µm counter
electrode (C). In order to lower noise level, the
working electrode is surrounded by the reference
electrode.
2.4 CE/ECD Procedure
Each microchannel was preconditioned prior to use.
Acetone solution was flushed through the
microchannel for about 40 min to clean the
microchannels. Next, DIW and buffer solution were
flushed through the capillary for an hour
respectively. The running buffer solution was 10
mM 2-(N- morpholino) ethanesulfonic acid (MES)
fixed to pH 6.5 using 10 N NaOH. After
preconditioned, the entire microchannels would be
full of buffer solution. For CE process, no bubbles in
the capillary were permitted. The testing analytes
were injected by applying electric field of + 50 V/cm
from sample reservoir to sample waste reservoir.
With this process, the testing analytes are placed at
the head of the separation channel after about 7 sec
and buffer solution is still inside the microchannels.
Separation of the analytes was performed by
applying electric field of + 60 V/cm between buffer
CAPILLARY ELECTROPHORESIS ELECTROCHEMICAL DETECTOR WITH NOBLE MICROCHANNEL
STRUCTURE FOR MINIATURIZATION - Development of a Capillary Electrophoresis Microchip Format
Electrochemical Detector for Endocrine Disruptors Sensing
131