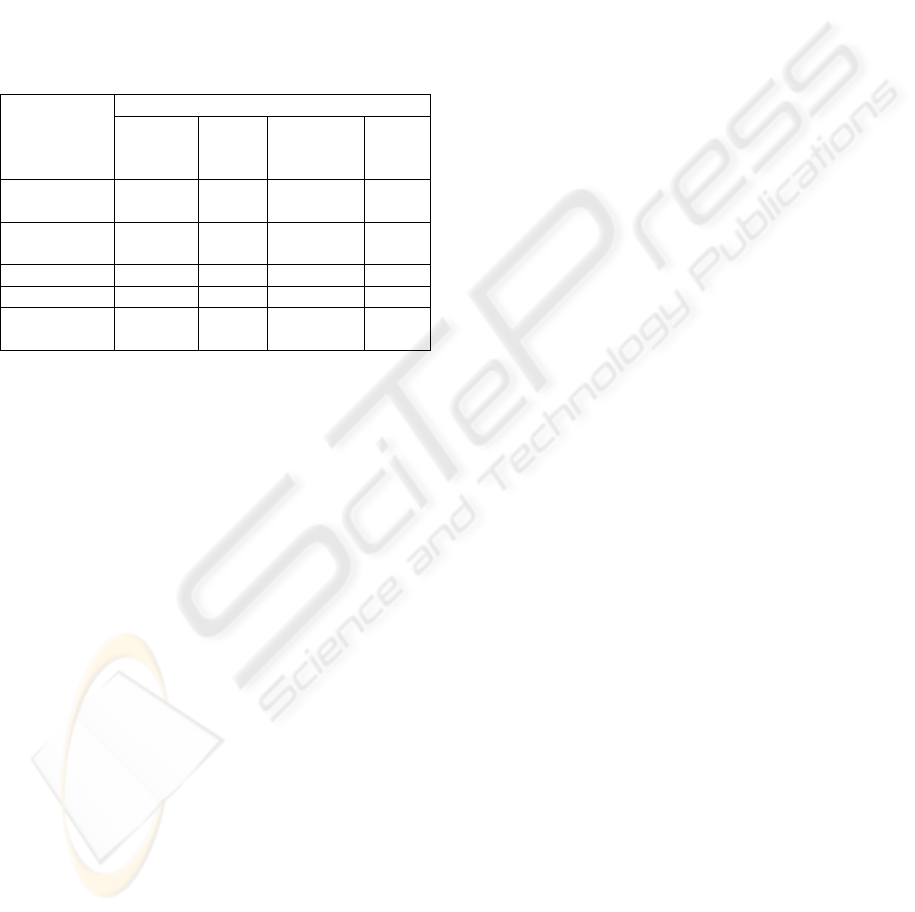
a) controlled electrical drive with rotating motor;
b) controlled electrical drive with linear motor;
c) controlled pneumatic actuator;
d) controlled Shape Memory Alloy (SMA)
actuator.
These solutions were thoroughly analysed and
compared evidencing for each advantages and weak
points in view of the specific application. The main
results of this comparison are summarized in Table
3.
Table 3: Comparison among main possible solution for the
actuators of device.
Solution
Requirement
Rotating
motor
Linear
motor
Pneumatic
actuator
SMA
actuat
or
Max.
Torque
Good
Very
good
Very
good
Poor
Dynamical
response
Very
good
Very
good
Good Poor
Wearability Good Good Short Fair
Cost Good Fair Fair Fair
Weight and
dimensions
Very
good
Very
good
Poor Good
The electrical drive with a rotating motor (DC or AC
brushless) satisfies all main requirements: it has low
weight and appropriate dimensions, affordable cost
and simple structure which allows to build a device
with a good wearability. Finally, a quite wide variety
of solutions (in terms of size and specific features) is
available on the market, allowing to tailor the choice
in view of the requirements of the specific
application. The drawback of this solution is the
need of using an epicycloidal gear reducer, because
rotating motors present high speed and low torque,
while for ankle actuation, mechanical power is
needed in the form of a relatively high torque acting
at relatively low speed. The use of a gear reducer
implies an increase in the weight of the device,
which can be however kept within reasonable limits.
The linear motor mainly has the same advantages
of the rotating motor and does not bear the drawback
of using a gear reducer, because linear motors
provide relatively high force at low speed, but is
much more expensive than rotating motors, requires
a more complicate mechanical design of the system
and less alternatives are offered on the market.
Pneumatic actuation was considered also
referring to previous applications to ankle actuation:
(Sawicki, 2005) and (Ferris, 2005) showed that this
kind of actuation is able to reproduce with good
accuracy the features of actual ankle motion. In view
of the aims of this project however, this solution
compared to electromechanical solution provides
lower actuation speed, lower maximum control force
and requires auxiliary systems of relatively large
size and potentially disturbing, like the air
compressor.
The SMA actuator solution was also considered
based on some tentative applications in the bio-
medical field, including a parallel project within the
HINT research project. However, besides some
practical disadvantages like the need for a rather
complicated cooling system, present SMA actuation
technology appears to suffer from an insufficient
dynamical response which is not able to ensure the
required actuation speed to implement ankle motion
control.
Based on the analysis summarized above, the
solution based on rotating electric motor was
identified as the most appropriate in terms of
technical requirement and related costs and was
chosen for development. In particular, a 150 W DC
motor (MAXON RE40 150W), driven by a 4-Q-DC
servoamplifier (MAXON ADS 50/10) and coupled
with an epicycloidal gear reducer with a gear ratio of
1:113 (MAXON GP 52C) was chosen.
The second stage of the concept development
consisted in the design of the interface between the
actuator and the leg. The basic idea underlying this
activity was to implement a configuration similar to
the one used in the Lokomat machine. On that
device, the feet are restrained by a sling held by an
arm rigidly connected to the exoskeleton (Figure 4).
The concept for interfacing active ankle actuation
with the patient’s leg was then based on the idea of
replacing the passive arm with an articulated
mechanical system, properly connected with the
motor, so that ankle actuation may be obtained by an
appropriate movement of the final link in the
articulated system. The functional scheme of the
solution identified is reported in Figure 5a: a support
is fixed over the Lokomat exoskeleton, and
connected by a hinge with a link which is actuated
by a crank fitted on the gear output shaft. The
rotation of the link produces a vertical motion of the
sling holding patient’s foot, which can be suitably
controlled by the electric motor. Figure 5b shows a
3D rendering of the ankle actuator, including
motor+gear, crank, link and connection to the
Lokomat exoskeleton.
As shown in Figure 6, the mechanism has a gear
ratio between the rotation of the gear output shaft
and the rotation of the link which is almost constant
and equal to 1:2.5. Figure 7 shows a picture of the
developed device.
A MECHATRONIC DEVICE FOR THE REHABILITATION OF ANKLE MOTION
59