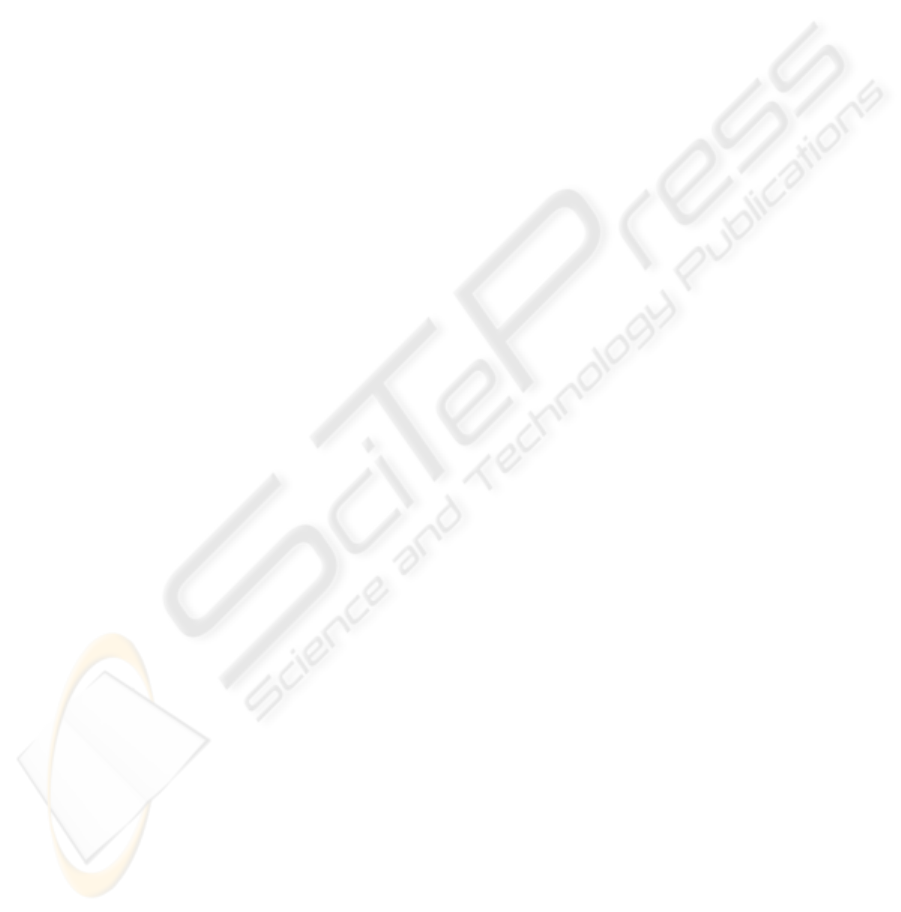
NEW DEVELOPMENT ON SHAPE MEMORY ALLOYS
ACTUATORS
Roberto Romano
Instituto de Pesquisas Tecnológicas do Estado de São Paulo and Telecommunications and Control Department
Escola Politécnica da Universidade de São Paulo, São Paulo, Brazil
Eduardo Aoun Tannuri
Instituto de Pesquisas Tecnológicas do Estado de São Paulo and Mechatronics Engineering Department
Escola Politécnica da Universidade de São Paulo, São Paulo, Brazil
Keywords: Modeling, shape memory alloy, actuator, robotics, sliding mode control.
Abstract: The present paper presents the development of a mechanical actuator using a shape memory alloy with a
novel cooling system based on the thermo-electric effect (Seebeck-Peltier effect). Such a method has the
advantage of reduced weight and requires a simpler control strategy as compared to other forced cooling
systems. A complete mathematical model of the actuator was derived, and an experimental prototype was
implemented. Several experiments are used to validate the model and to identify all parameters. A robust
and nonlinear controller, based on sliding-mode theory, was derived and implemented. Experiments were
used to evaluate the actuator closed-loop performance, stability, and robustness properties. The results
showed that the proposed cooling system is able to improve the dynamic response of the actuator.
1 INTRODUCTION
Shape Memory Alloys (SMAs) consist of a group of
metallic materials that demonstrate the ability to
return to some previously defined shape or size
when subjected to the appropriate thermal
procedure. The shape memory effect occurs due to a
temperature and stress dependent shift in the
materials crystalline structure between two different
phases called Martensite and Austenite. Martensite,
the low temperature phase, is relatively soft whereas
Austenite, the high temperature phase, is relatively
hard. The change that occurs within SMAs
crystalline structure is not a thermodynamically
reversible process and results in temperature
hysteresis. SMAs have been used in a variety of
actuation applications. The key feature of this
material is its ability to undergo large seemingly
strains and subsequently recover these strains when
a load is removed or the material is heated. SMA
actuators have several advantages such as excellent
power to mass ratio, maintainability, reliability, and
clean and silent actuation. The disadvantages are
low energy efficiency due to conversion of heat to
mechanical energy, inaccurate motion control due to
hysteresis, nonlinearities, parameter uncertainties,
difficulty in measuring variables such as temperature
and the slow response due to the thermal process
evolved in the working principle.
To operate quickly, the SMA must be cooled
rapidly. Some researchers have proposed static
methods, in which the SMA wires are continually
cooled by means of an air stream (Tanaka and
Yamada, 1991). In a similar way, Furuya and
Shimada (1990) used a cooling system based on
water immersion. In such case, cooling time was
reduced in 10 times compared to a non-cooled wire.
However, the power consumption of such actuator
has increased by a factor of 20, since in the heating
phase it is necessary much more power to
compensate the heat that is lost by the cooling
system. Golbert and Russel (1995) used a mobile
metallic heat sink and a complex mechanism
guaranteed that the sink was only in contact to the
wire being cooled, which minimizes the power
consumption of the actuator and increases its
dynamic behavior. Asada and Mascaro (2002)
developed an actuator with a cooling system based
on flowing water around the wire. A complex
55
Romano R. and Aoun Tannuri E. (2008).
NEW DEVELOPMENT ON SHAPE MEMORY ALLOYS ACTUATORS.
In Proceedings of the First International Conference on Biomedical Electronics and Devices, pages 55-61
DOI: 10.5220/0001047800550061
Copyright
c
SciTePress