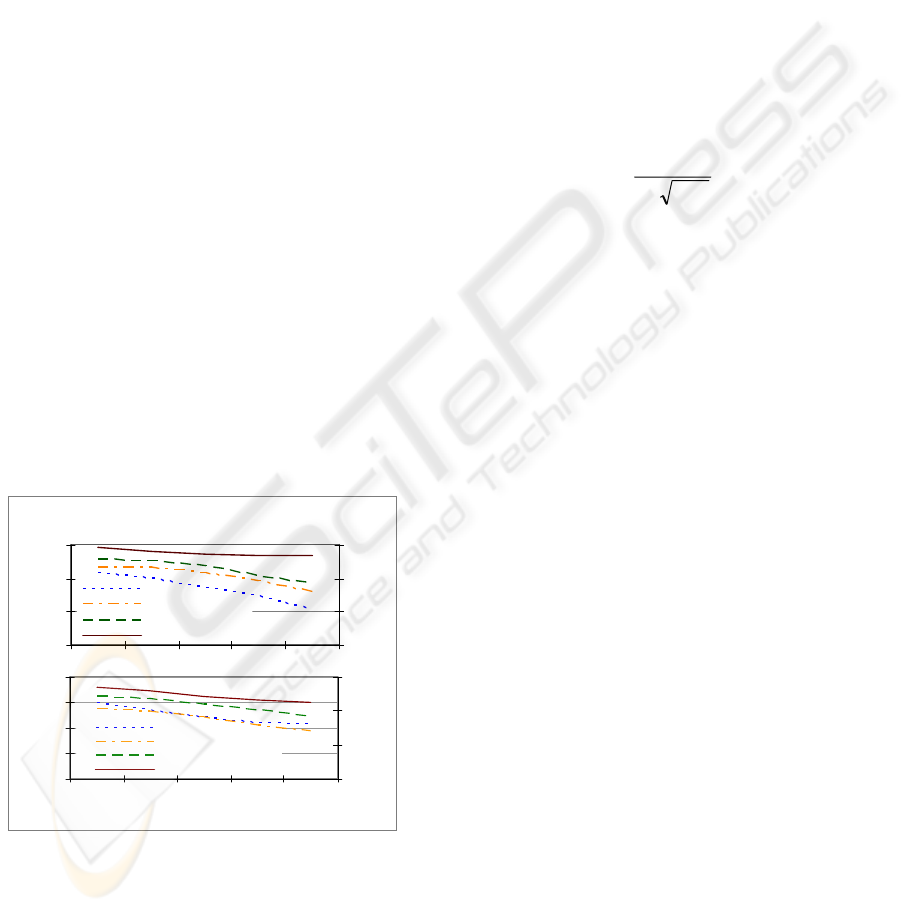
The three methods of evaluating the coupling
coefficient were implemented using genuine
physical parameters, and the results are shown in
figure 9. With the coils aligned axially, the coupling
coefficient decreases as the separation increases. The
simulated coupling coefficients have a mean
deviation of 16% from the experimental results.
However, the analytical results are far away. This is
illustrating the effects of the physical bulk of the
coils. The efficiency of the power transfer is also
shown in figure 9. The coupling coefficient drops at
a greater rate than the efficiency. This is illustrating
that, although the coupling coefficient may be low,
good power efficiency can still be achieved.
Figure 10 illustrates the effects of displacement
on coupling and efficiency when the coils are
separated by 10mm and 20mm. Again, the simulated
and practical coupling coefficients are fairly similar
(with a mean deviation of 9.5%), while the
analytical model significantly under estimates the
practical result at 10mm separation. However at
20mm separation, the analytical coupling coefficient
is in much better agreement with the simulated
results. This suggests that for lateral displacement at
larger separations, the magnetic coupling for the
physical coils is reasonably well represented by
idealised coils. The effect of lateral displacement on
efficiency was very small (efficiency dropped from
79% to 77% for 20mm lateral displacement) at
10mm separation. Efficiency drops more rapidly
down to 72% at 20mm separation.
Effect of lateral displacement on coupling
and efficiency
0
0.1
0.2
0.3
05101520
Displacement (mm)
Coefficienct of coupling
50%
60%
70%
80%
Efficiency
ka_10 mm
ks _10 mm
kp_10 mm
Efficiency_10 mm
Figure 10: Effects of displacement on coupling and
efficiency for coil separations of 10mm and 20mm.
The impact of rotational misalignment on
coupling was similar to the lateral displacement
case. The simulation result underestimated the
practical coupling for both 10mm and 20mm
separation however it was within a mean deviation
of 14.76% of the experimental measurements.
4 DISCUSSION
The maximum power transfer of a TET system
refers to the maximum power that can be transferred
from primary to secondary coil disregarding the
losses associated with the components in the circuit.
The maximum power that can be transferred by a
current-fed push-pull resonant converter TET system
has been derived by Si et. al. (Ping Si 2007) using
mutual inductance between the primary and
secondary coils. This relationship is shown in
equation 16 as a function of the coupling coefficient.
in
sp
dc
V
LLf
kV
P
8
max
π
=
(16)
Where L
p
and L
s
are the primary and secondary
coil inductances, k is the coupling coefficient, P
max
is
the maximum power transfer, V
in
is the DC input
voltage, V
dc
is the output voltage at the load and f is
the system resonant operating frequency.
Equation 16 is based on the assumption that high
order harmonic components are negligible and the
dc current is continuous at the pickup. These
assumptions are reasonable for practical circuits.
Equation 16 shows that for given primary and
secondary circuits, the maximum power transfer
capacity of a TET system is proportional to the
coupling coefficient. Good coupling can increase the
maximum possible power transfer from primary to
secondary coils. However, in terms of the power
efficiency, from the previous results shown in
section 3, it is clear that coupling does not have a
dramatic effect. This is a very important feature of
the system, meaning it is possible to achieve high
power efficiency for a loosely coupled TET system.
During the power transfer process, there is little
power loss in the air gap between the primary and
the second coils. Therefore the coupling coefficient
is not sensitive to the overall power efficiency of the
system. However with low coupling, high magnetic
strength is required to deliver the same amount of
power, so the required current and/or voltage use to
generate the field needs to be higher, resulting in a
higher loss in the drive circuits. To further
understand the power efficiency issue, the power
losses in each component of the TET system was
identified.
The loss components were measured from the
TET system and are presented in figure 11. The total
power loss between the input and output of the
system was also measured, and the difference
0
0.05
0.1
0.15
0.2
0 5 10 15 20
50%
60%
70%
80%
ka_20 mm
ks_20 mm
kp_20 mm
Efficiency_20 mm
BIODEVICES 2008 - International Conference on Biomedical Electronics and Devices
174