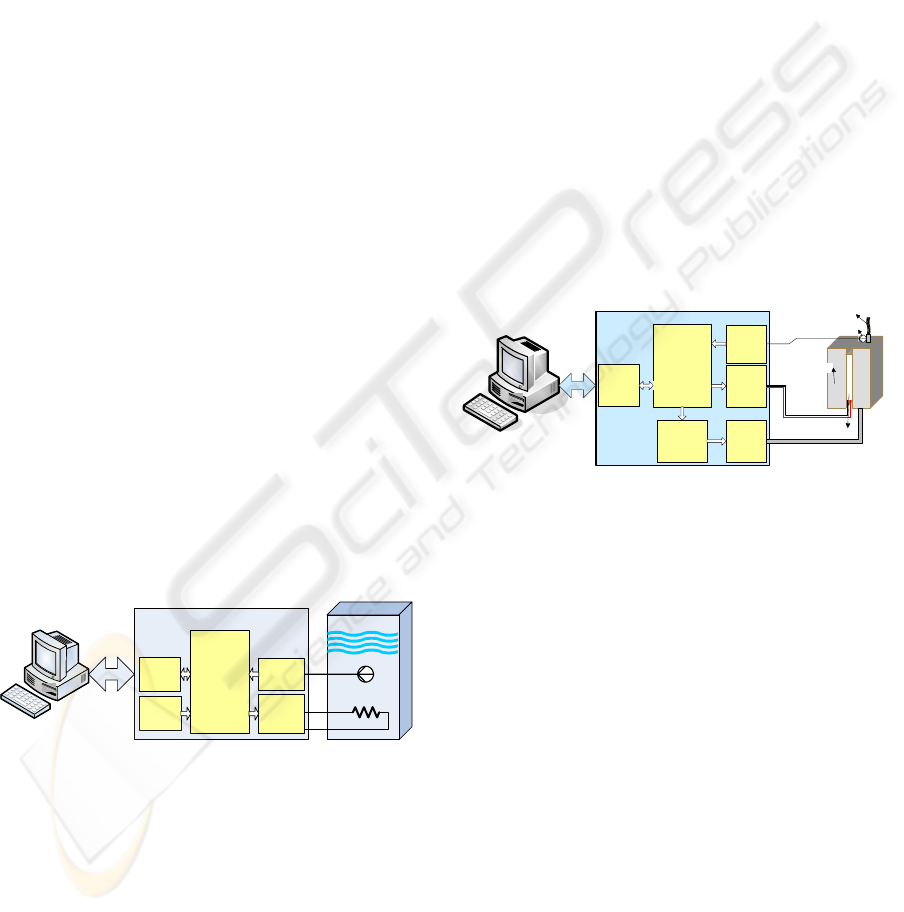
different tuning parameters can be chosen and
different cascade controllers can be appended.
PACD current available controllers include lead, lag,
lead-lag, double-lead, double-lag, PI and PID. The
internal structure of PACD uses negative unitary
feedback, and it allows to cascade up to 10
controllers of each type. This feature makes it
possible to accomplish many different
configurations to analyze in different operation
essays, so that the controller designer can choose the
configuration that gives the best results in terms of
the desired plant operation requirements.
2.2 Water Test Setup
A testing setup was assembled, whose main parts are
shown in the block diagram shown in Figure 5. The
setup is composed by a printed circuit board from
E96 equipment, a water container with a heater
resistance inside and an additional serial
communication interface. The used microcontroller
is the Intel’s N87C196KB running at 12 MHz. The
temperature sensor is LM35DZ (National),
accompanied by an amplifier and adjustment
trimmer, allowing an adjusted error of 0.2 ºC in the
whole temperature range, from 0 ºC to 50 ºC. A
special version of the E96 embedded software was
created (C language, IAR compiler), so the equipment is
commanded through serial communication by PACD
software in the external PC. The power control variable
is delivered to a heater resistance of 700 W (220 V), and
variable percent power is determined by PWM (Pulse
Width Modulation) using integral cycle technique, in
order to avoid harmonic frequencies in the mains. The
PWM period corresponds to 50 cycles of the 60 Hz
electric network, so the power driver has 2% resolution.
Figure 5: Water caloric setup block diagram.
2.3 Air Test Hardware and Software
Air stimulator E107AR was used with a modified
protocol to facilitate the tests, and its basic block
diagram is shown in Figure 6. The main parts of the
system are composed by: an ADuC841
microcontroller (Analog Devices) running at 20
MHz; a precision resistive NTC sensor used to
measure the temperature of the heated or cooled air
flow, that after being adjusted by software, provides
0.2 ºC error in the whole temperature range (12 ºC to
50 ºC); an air pump that provides air flow from 4 to
12 liters/minute; and an air heater/cooler module
formed by refrigeration sink, a Peltier effect device
and a heater/cooler sink.
The internal E107AR software was modified to
inhibit the original temperature controller and the
periodic temperature sampling. It makes possible to
PC software setting the sampling frequency as
desired, and also, letting the PC software to control
the output air flow and the amount of power to heat
or to cool the air. The air pump power interface uses
an AC current control technique that delivers AC
voltage to the pump according to the
microcontroller's D/A converter. The Peltier effect
device is driven by an H-Bridge DC power interface,
which is controlled by the ADuC841 pulse width
modulation (PWM) output. The E107AR also has a
built-in RS232 level converter to translate the
microcontroller's TTL serial signals to ± 12 V levels
on the PC serial port.
Figure 6: Air caloric setup block diagram.
3 RESULTS
Several tests were accomplished for PACD software
validation and to find the best controller for each
setup.
3.1 Results from Water Test Setup
For modeling the water temperature system to be
controlled, a 25 % power step response was applied
and three PACD available model methods where
used. Figure 7 shows setup real step response
pointed as “A”. The letters B, C and D indicate
respectively the responses from Hägglund, Ziegler-
Nichols and Mollenkamp models. Carrying out a
manual adjustment in Ziegler-Nichols obtained
model, it was possible to arrive to the time response
indicated by “E”, which is even closer to the real
plant time response. Equation 1 shows this model.
Air flow
E107AR PCB
SRL
TTL to
RS232
Adapter
Opto-
isolated
Power
Interface
Adjust
and
amplifier
PWM
ADC0
UART
ADuC841
DAC
AC Control
Power
Interface
Air
pump
Refrigeration
Temperature sensor
Peltier effect
device
SERIAL
E96 PCB
TTL to
RS232
Adapter
EPROM
memory
80C196
ADC0
PWM
Opto-
isolated
Power
interface
Water container
Adjust
and
amplifier
resistance
temperature
sensor
UART
Controllers in software
BIODEVICES 2008 - International Conference on Biomedical Electronics and Devices
226