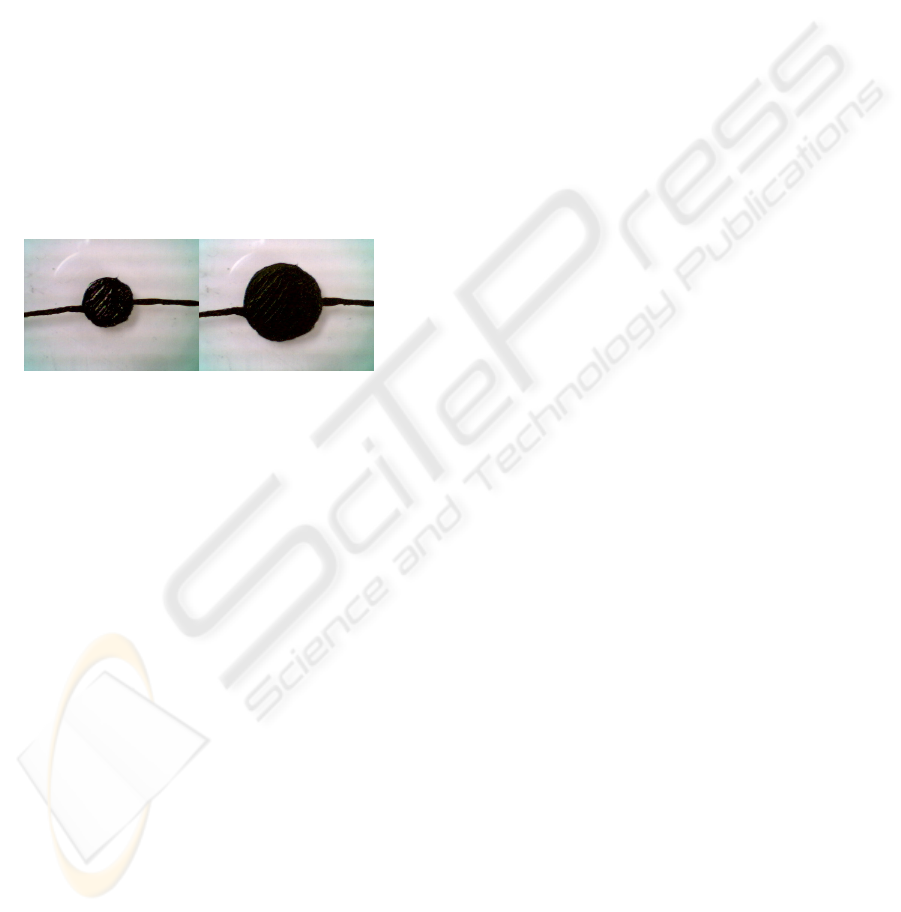
losses and some can operate in temperatures ranging
from -100ºC to 260ºC, making them well suited to
dynamic, high speed applications in harsh
environments. Their availability in monomer form
(e.g. NuSil CF19-2186, Dow Corning Sylgard 184)
enables the tuning of material properties (e.g.
stiffness, elongation at break, and geometry) and
facilitates the creation of silicone based composites
through the incorporation of additional material
prior to polymerization.
3M’s commercially available VHB4905 double-
sided polyacrylate tape has a high degree of
viscoelasticity, but at low speeds is capable of the
highest reported active displacement (380%) and
energy density (3.4MJ/m
3
) of any DE polymer. Fig.
2 illustrates a simple, easily fabricated DE made
from a prestrained, partially electroded VHB
membrane at rest (Fig. 2 left), and activated with an
electric field of 252V/µm (Fig. 2 right). The
electroded area expands by 125% at this field.
Figure 2: A VHB DE actuator at rest (left), and actuated
with an electric field of 252V/µm (right).
While silicone and VHB4905 are popular choices
for DE materials, a wide variety of other materials
can be used and which is appropriate is highly
dependent on the application. It is convenient
therefore to define a relationship between the key
properties of a material that results in an index value
that can then be used to compare materials. The DE
“Figure of Merit” relates a material’s dielectric
constant (ε
r
), the breakdown strength (E
b
), and the
Young’s modulus (Y), using the following formula
(Sommer-Larsen and Larsen, 2004):
Figure of Merit. = 3ε
r
E
b
2
/Y (4)
It is important to note that typical polymers with
suitably low stiffness and high dielectric breakdown
strengths have low dielectric constants (typically
<5). Substituting this value into Equation (1) it is
clear that high electric fields (~50-150V/μm) are
required to generate enough pressure to deform a DE
more than a few percent.
3 DIELECTRIC ELASTOMERS
IN BIODEVICES
DEs acting either in an actuator, sensor, or power
generator mode show great promise for a number of
biomedical applications. The key strength of DE
technology however is the ability for a single
lightweight device to operate in multiple modes.,
thereby reducing device volume, complexity, and
component count. This ability, coupled with their
biocompatibility, opens up a number of possibilities
not only for implantable or prosthetic devices, but
also for tools to assist both surgeons and patients
during operative and post-operative procedures.
3.1 Artificial Muscles
With performance metrics that exceed that of natural
muscle, DEs show great promise as artificial
muscles. Like natural muscle, DEs can be controlled
in terms of position, speed and stiffness. Controlling
the charge stored on a DE results in stable position
control. By controlling the rate of charging the speed
of actuation can be controlled. Similarly, utilising
the geometry of the device and the level of charge
stored on the DE, it is possible to determine the
electroactive forces, which in conjunction with
knowledge of the mechanical behaviour of the DE
itself, can be used to control stiffness.
To achieve accurate control in terms of any these
parameters it is necessary to obtain feedback data
from which a physical aspect of the device can be
inferred. Conventionally an external sensor is
required to obtain this data but applying such an
approach to DEs adds to the complexity, volume,
mass, cost and power requirements of the device.
Instead, self-sensing using inherent characteristics of
the DE eliminates the constraints an external sensor
implies and enables the creation of entirely
compliant smart devices. Such devices, with an
overall texture and consistency comparable to
natural muscle, will have a natural look and feel; a
factor that has been found to have a significant
impact on patient acceptance of such devices
(Popovic et al., 2002).
DE device properties such as electrode resistance
(O'Brien et al., 2007), capacitance (Toth and
Goldenberg, 2002), and electrical current (Bauer and
Paajanen, 2006) have all been used to infer the
physical state of a DE actuator subject to specific
operating conditions. As self-sensing develops
further and the richness of the feedback information
increases, so too will the accuracy with which DE
devices can be made to respond to a control signal.
SMART DIELECTRIC ELASTOMERS AND THEIR POTENTIAL FOR BIODEVICES
287