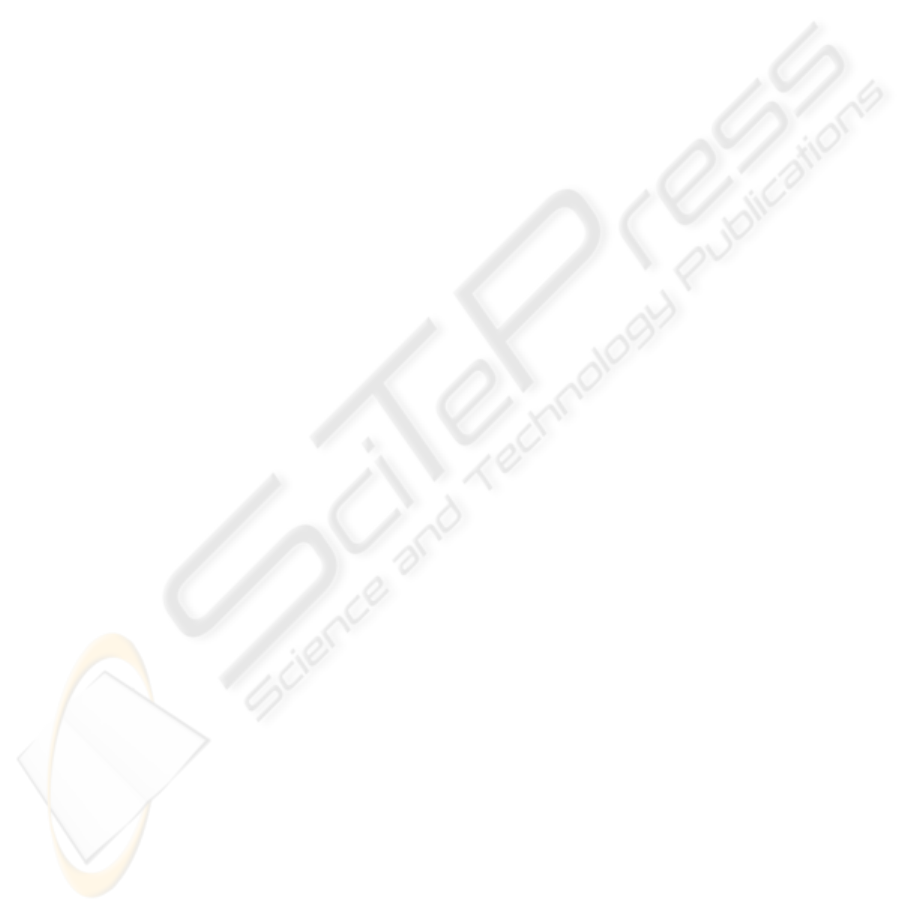
a well-characterized biocompatible material that is
used ubiquitously in cell culture applications. In
addition, it is well know that the stiffness of the
substrate can significantly affect the mechanical
behaviour of cells (Lo et al., 2000, Choquet et al.,
1997). Most devices to date have been fabricated
from relatively flexible (silicone rubber) or
relatively stiff (silicon) materials. In this case we use
a materials with intermediate stiffness.
The device consists of a four or eight probe
cantilever array fixed to a glass substrate at the base
of the beams. The ends of the beams were designed
to provide adequate surface area for cell spreading.
The fixed post at the center of the device was
included to provide a location for initial cell
attachment as well as provide a fixed reference point
for probe deflection analysis. As the cell attaches to
the beams and exerts forces, the deflection of each
cantilever is measured optically over time to give
spatially and temporally resolved measurement
capabilities.
2 MATERIALS AND METHODS
2.1
Device Fabrication and
Characterization
Devices were fabricated using sacrificial layer
micromolding as described in (Ferrell et al., 2007).
A water-soluble sacrificial layer was first patterned
by photolithography and reactive ion etching. A
layer of poly(vinyl alcohol) (PVA) was dissolved in
water to a final concentration of 10% (wt/wt). The
PVA solution was spin coated on 18 mm glass
coverslips at 1000 rpm. A protective layer of
poly(methyl methacrylate) (PMMA) was then spin
coated on top of the PVA. The PMMA layer
protected the PVA from the developer in the
upcoming photolithography process.
Photolithography was then used to pattern an etch
mask on the PVA/PMMA films. Reactive ion
etching in an O
2
plasma was used to removed both
the PVA and PMMA in the unmasked regions. The
remaining photoresist and PMMA layers were then
removed by sonication in acetone, leaving only the
patterned PVA.
A PDMS mold of the device was fabricated by
replica molding (Xia and Whitesides, 1998) of a
photolithographically patterned master. The PDMS
mold was spin coated with a solution of polystyrene
in anisole (7.5% wt/wt). The polystyrene was
removed from the raised portions of the mold by
contact with a glass slide heated to 200 ºC. The
remaining polystyrene was left in the recessed
portion of the mold. The mold was aligned with the
sacrificial layer and heat (120 ºC) and pressure (75
psi) were used to transfer the device onto the
sacrificial layer. The device was then annealed at
115 ºC for 15 minutes to improve adhesion of the
anchor regions and remove any residual stress in the
beams.
The thickness of each device was characterized
using a stylus profilometer. The thickness range for
the above processing parameters was 1.31-1.75 µm.
2.2 Design and Simulations
Finite element simulations (ANSYS) were used to
guide the design of the cantilever beam. The beam
was designed to give reasonable x,y deflection
response while still conforming to the geometrical
constraints of the devices circular configuration. The
deflection plot for a 5 nN force applied to an area at
the end of the cantilever beam at 10º increments
from 0º to 360º is shown in Figure 1.
An ideal beam response would be a circular
deflection profile with no offset between the
direction of the beam deflection and the force
direction. The plot shows a slight offset. The plot
also shows that the beam is stiffer in the 90º and
270º directions compared to the 0º and 180º
directions. This leads to slightly less sensitivity to
forces in those general directions, but the overall
response of the beam is adequate for the application
described here.
2.3 Cell Culture and Image Acquisition
The cells used in this study were WS1 human skin
fibroblasts (ATCC). Cells were cultured in
Minimum Essential Medium, Eagle (ATCC)
supplemented with 10% fetal bovine serum and 1%
penicillin-streptomycin. Cells were cultured at 37ºC
in a 5% CO
2
atmosphere. To obtain cells for
measurements, cells were detached from T75 tissue
culture flasks using .25% trypsin-EDTA.
Prior to performing measurements, the devices
were modified by a brief exposure to O
2
plasma in a
reactive ion etcher to make the surface more
hydrophilic and improve cell attachment. Devices
were fixed to a PDMS coated petri dish. The PDMS
coated dish allowed fixation of the device without
the use of a chemical adhesive. The devices were
placed in cell culture medium to dissolve the
sacrificial layer. After complete dissolution of the
BIODEVICES 2008 - International Conference on Biomedical Electronics and Devices
152