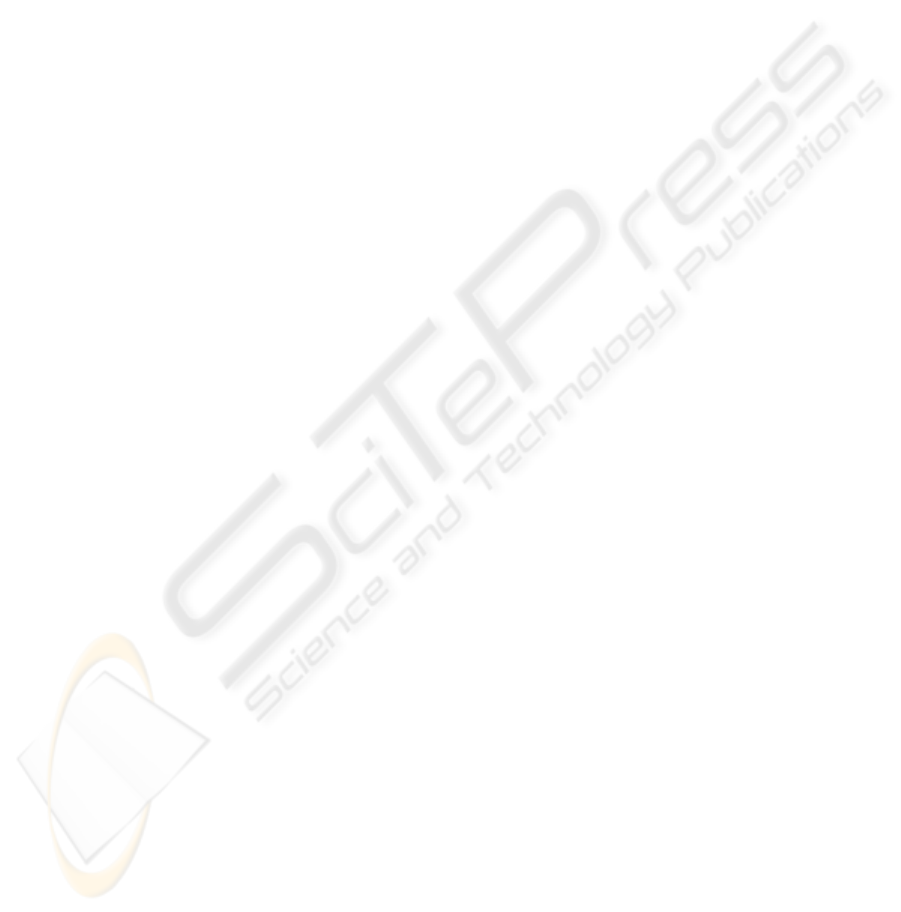
ACKNOWLEDGEMENTS
On this work participated Dipl.-Ing. C. Breuninger
and several students financed by the German
Research Council (DFG).
REFERENCES
Beer, H.J., Bornitz, M., Hardtke, H.J., Schmidt, R.,
Hofmann, G., Vogel, U., Zahnert, T., Huettenbrink,
K.B., 1999. Modelling of Components of the Human
Middle Ear and Simulation of Their Dynamic
Behaviour. Audiology and Neuro-Otology. 4:
156 -162.
Eiber, A., Freitag, H.-G., Burkhardt, C., Hemmert, W.,
Maassen, M., Rodriguez Jorge, J., Zenner, H.-P.,
1999. Dynamics of Middle Ear Prostheses -
Simulations and Measurements. In Audiology and
Neuro-Otology. 4: 178 - 184.
Eiber, A., Breuninger, C., 2004 a. Mechanical Problems in
Human Hearing. Proceedings in Applied Mathematics
and Mechanics, Vol. 4, No. 1, p. 51 - 54.
http://www.wiley-vch.de
Eiber, A., Breuninger, C., 2004 b. Nonlinear Properties of
the Middle Ear: Some Influences on Hearing and
Diagnosis. In: Gyo, K., Wada, H. (eds), Middle ear
Mechanics in Research and Otology, p. 19 - 28 .
World Scientific. Singapore.
Eiber, A., Breuninger, C., Rodriguez Jorge, J., Zenner, H.-
P., Maassen, M., 2007. On the Optimal Coupling of an
Implantable Hearing Aid – Measurements and
Simulations. In: Huber, A., Eiber, A. (eds), Middle ear
Mechanics in Research and Otology, p. 246 - 252.
World Scientific. Singapore.
Gan, R.Z., Feng, B., Sun, Q., 2004. Three-Dimensional
Finite Element Modelling of Human Ear for Sound
Transmission. Annals of Biomedical Engineering. 32,
(6): 847 – 859.
Hudde, H., Weistenhoefer, C., 1997. A Three-
Dimensional Circuit Model of the Middle Ear.
Acustica united with Acta Acustica. 83, (3): 535 – 549.
Hong, E.-P., Kim, M.-K., Park, I.-Y., Lee, S.-H., Choi, J.-
H., 2007. Vibration Modeling and Design of
Piezoelectric Floating Mass Transducer for
Implantable Middle Ear Hearing Devices. IEICE
Transactions on Fundamentals of Electronics,
Communications and Computer Sciences. 90,
(8):1620 - 1627.
OTOlogics LLC, Boulder.
http://www.otologics.com/
Prendergast, P.J., Ferris, P., Rice, R.J., Blayney, A.W.,
1999. Vibro-acoustic modelling of the outer and
middle ear using a finite-elemente method. Audiol
Neurootol, 4, 185 – 191.
Rodriguez Jorge, J., Pfister, M., Zenner, H.-P., Zalaman,
I., Maassen, M., 2006. In Vitro Model for
Intraoperative Adjustments in an Implantable Hearing
Aid (MET). In Laryngoscope, 116, 246 - 252.
Sequeira, D., Breuninger, C., Eiber, A., Huber, A., 2007.
The Effect of Complex Stapes Motion on the Cochlea
in Guinea Pigs. In: Huber, A., Eiber, A. (eds), Middle
ear Mechanics in Research and Otology, p. 130 - 135.
World Scientific. Singapore.
Suzuki, J. I. (ed), 1988. Middle Ear Implant: Implantable
Hearing Aids
, Karger. Basel.
Tjellstroem, A., 1990. Osseointegrated implants for
replacement of absent or defective ears. Clinics in
Plastic Surgery, 17: 355 – 365.
Wada, H., Metoki, T., Kobayashi, T., 1992. Analysis of
dynamic behavior of human middle ear using finite-
elemente-analysis. J Acoust Soc Am. 96: 3157 - 3168.
Waldmann, B., Maier, H.,Leuwer, R., 2004. Nonlinear
Properties of the Middle Ear: Some Influences on
Hearing and Diagnosis. In: Gyo, K., Wada, H. (eds),
Middle ear Mechanics in Research and Otology, p.
377-383. World Scientific. Singapore.
Zwislocki, J., 1963. Analysis of the Middle-Ear Function.
Part II: Guinea Pig Ear. J Acoust Soc Am. 35, (7),
1034 - 1040.
ELECTRONIC DEVICES FOR RECONSTRUCTION OF HEARING
309