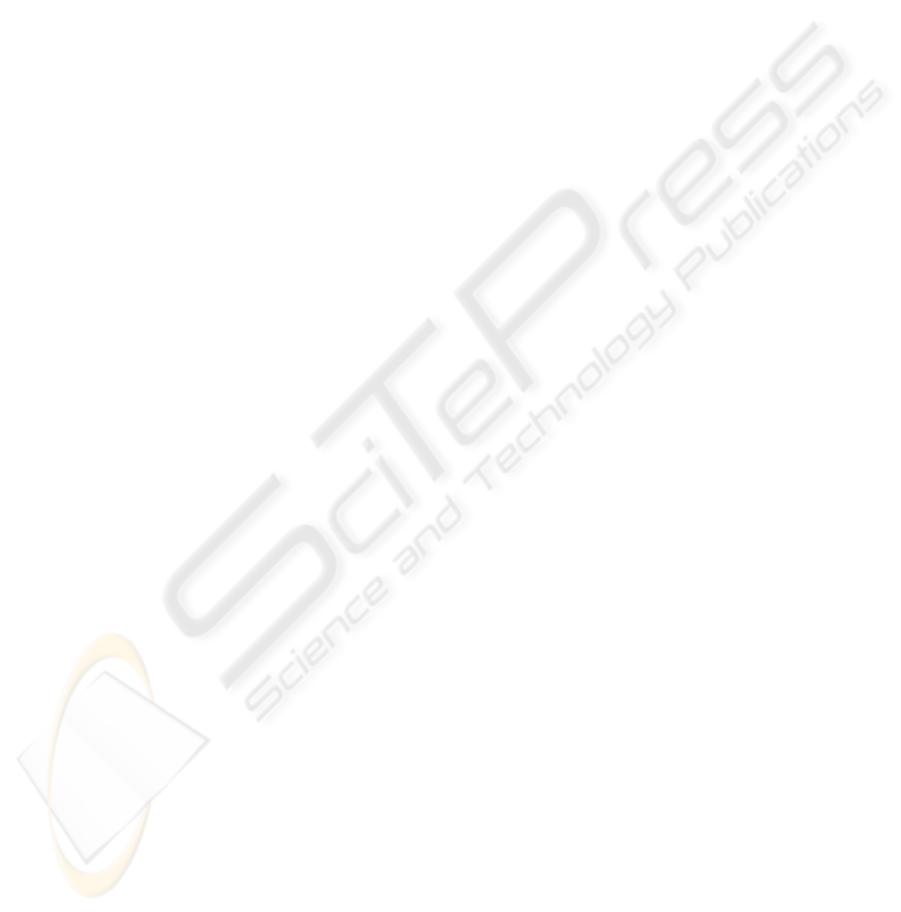
are, like silicone, one of the highest purity coatings
on the market (Licari 2003). Parylene is flexible
coating material just like silicone, but compared to
silicone, parylene has better moisture and chemical
resistance and also extremely thin coatings are tight
enough for insulation and implants (Stieglitz et al.
2002). In addition, parylene has excellent adhesion
to most surfaces (Licari 2003, p. 157).
2 BACKGROUND
2.1 Parylene
Parylene (poly-para-xylylenes) is a universal term
for members of a unique polymer class (Licari
2003). By using dimer of di-para-xylylene, parylene
has the ability to be deposited by vacuum deposition
onto exposed surfaces at room temperature (Licari
2003). Varying the process parameters of deposition
can control the thickness of parylene and the
thickness may vary from 0,025 µm to several tens of
micrometers. According to Licari (2003), the final
thickness of coating can be controlled to ±10 % of
desired thickness. Nevertheless, our laboratory
results have proven that the thickness variance can
be even greater. The parylene coating is inert and
conformal and hence provides dielectric and
environmental isolation. Parylene coating is used in
many applications like aerospace, automotive and
military industry, and also in medical applications.
Nowadays, the four most frequently used
commercially available parylene variations are
parylene N, C, D, and HT. The two first have the
longest history of use and are most commonly used
in medical coating applications. This paper
concentrates on coating with the polymer parylene
C. (Specialty Coating System 2007)
Parylene C can provide extremely thin, uniform,
and pinhole-free coating. It has low electrical
dissipation factor, high dielectric and mechanical
strength, and good chemical, electrical, and
biological stability. It also has significantly lower
moisture, chemical, and caustic gas permeability
than parylene N. Above-mentioned reasons make
parylene C very compatible for medical implants. In
addition, parylene C is not cytotoxic and it is proven
to be compatible with body tissue and blood. (Yang
1998)
2.2 Parylene Coating Process
The parylene coating process can be divided into
three stages. The first stage is vaporization, the
second is pyrolysis, and the third stage is deposit. In
the beginning of the coating process, the raw
material, dimer that is white powder, is vaporized
under vacuum (1.0 mbar) and heated to a dimeric
gas at approximately 150 ˚C. During the second
stage, pyrolysis, the gas is pyrolized to cleave the
dimer to its monomeric form under vacuum (0.5
mbar) to approximately 680 ˚C. In deposition stage
the monomer reaches the room temperature
deposition chamber. The monomer gas
simultaneously absorbs and polymerizes on the
substrate as a transparent parylene film. The
substrate temperature never rises more than couple
of degrees above the room temperature. (Specialty
Coating System 2007; Pang et al. 2005, p. 4)
The surface area of substrates in deposition chamber
can vary a lot. The substrates to be coated are
positioned in a stand that spins in a vacuum
chamber. When a small amount of dimer is used, it
does not matter where the substrates are located in a
stand. Also the stand area might vary a lot. The
stand might for example have several levels and the
grid on each level might be tight. The coating
thickness is mainly a function of substrate surface
area in chamber and amount of dimer charge.
Program parameters have also minor importance.
Even 1 μm thick coating is discovered to be tight
enough for implants (Stieglitz et al. 2002). Thus it is
very important to be able to measure the thickness of
the coating accurately. The process is controlled by
the deposition process parameters. The process
parameters for our measurements are found from
known coating process recipes that are used also in
Para Tech Coating, Inc. in Sweden (Para Tech
Coating, Inc. 2006). Recipes determine the amount
of dimer, process temperatures and times, and
approximate final parylene thickness. It has been
proven that when different recipes are used for same
amount of dimer, the final thickness might be
different. Therefore, in addition to the amount of the
dimer, also the process parameters affect the final
thickness of parylene.
After the coating process, the achieved thickness
could be measured by releasing a sample parylene
film from the top of a preparat glass that has been in
vacuum chamber, and then measuring the thickness
of film. This does not give very accurate results,
since the thin film is charged electrically and it
might be creased. Also, after releasign the film from
the top of a preparat glass, the film surface might
already contain some impurities from the air that
affect the result. Moreover, as the parylene thickness
can depend on the location in the camber, the
thickness of the film on the preparate glass can be
METHOD FOR MEASURING PARYLENE THICKNESS USING QUARTZ CRYSTAL MICROBALANCE
223