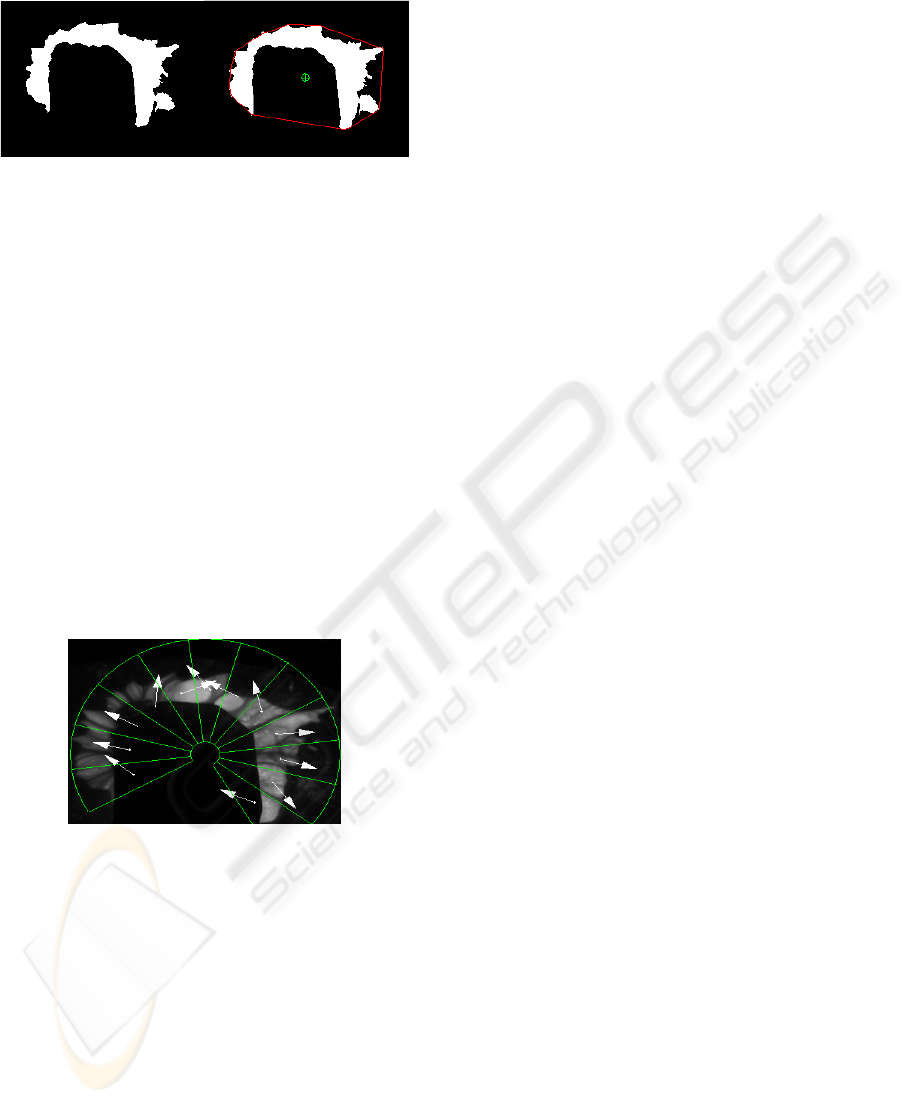
the direction of the tracking vectors for analysing the
slag motion.
Figure 4: The electrode centre as the convex hull centroid.
3.4 Direction of the Slag Flow
To determine the overall slag motion, the region of
active slag motion is divided into sectors of a circle
centred at the approximated electrode centre (Figure
5). The number of sectors and the distance between
them is user dependant. Experiments showed that in
combination with 600 to 1000 tracking points, 12
sectors delivered good results.
Within each sector the tracking vectors are
accumulated into a histogram of directions. To
improve robustness in detecting the main direction
in each sector we do not take into account vectors
whose length do not exceed 3 pixels. Finding the
maximum in the directional histogram provides the
preferred direction of the slag motion of the
considered sector. Figure 5 displays the main
directions found for each sector.
Figure 5: Sectors of active slag areas and detected flow.
For the final quantification of the slag motion,
we have to determine if most of the slag is moving
towards the electrode or in the opposite direction.
For this purpose each vector direction is compared
to the direction of the sector they belong to. The
direction of a sector is simply the direction of the
line bisecting the sector towards the centre of the
electrode. If the absolute angular difference between
a vector direction and the direction of its sector lays
within a range of 0-60° the slag motion for this
vector is “good”, if the absolute difference is
between 60° and 120° the slag motion is
“undetermined” and otherwise the slag motion is
“bad”. For quantifying the overall slag motion in a
given sector a majority voting is performed among
the slag motion vectors belonging to the same sector.
4 CONCLUSIONS
We presented an experimental industrial vision
system capable of measuring the slag temperature in
a contactless manner with an accuracy of ± 5° C. By
tracking the flow patterns of the slag, that system
can also monitor and help assessing the quality of
the produced steel. As future development we plan
on investigating the relationship between the slag
motion flow and its temperature in order to give the
operator a better insight about the produced steel.
ACKNOWLEDGEMENTS
This work has been carried out within the K plus
Competence Centre Advanced Computer Vision.
This work was funded from the K plus Program.
REFERENCES
Bouguet, J.-Y. (2000) ‘Pyramidal Implementation of the
Lucas Kanade Feature Tracker: Description of the
Algorithm’, OpenCV Documents, Intel Corporation,
Microprocessor Research Labs.
Campbell, N. R.; Gardiner, H. W. B. (1925) ‘Photo-
electric colour-matching’, Journal of Scientific
Instruments, Vol. 2, Issue 6, pp. 177-187.
Lucas, B.D.; Kanade, T. (1981) ‘An Iterative Image
Registration Technique with an Application to Stereo
Vision’, Proceedings of the 7th International Joint
Conference on Artificial Intelligence, pp. 674-679.
Meriaudeau, F.; Legrand, A.C.; Gorria, P. (2003) ‘Real-
time multispectral high-temperature measurement:
application to control in the industry’, Proceedings of
the SPIE, Vol. 5011, pp. 234-242.
Otsu, N. (1979); ‘A threshold selection method from gray-
level histograms’, IEEE Transactions on Systems,
Man and Cybernetics, Vol. 9, pp. 62-66.
Urban, H.; Sidla, O. (2005); ‘Online Temperature
Measurement and Flow Analysis of Hot Dross in a
Steel Plant’, Proceedings of the SPIE, Vol. 6000, pp.
66-74.
Shi, J.; Tomasi C. (1994); ‘Good Features to Track’,
Proceedings of the IEEE Conference on Computer
Vision and Pattern Recognition, Vol. 1, pp593-600.
Simoncelli, E.P. (1994); ‘Design of multi-dimensional
derivative filters’, Proceedings of the IEEE Int.
Conference on Image Processing, Vol. 1, pp790-793.
A SLAG TEMPERATURE AND FLOW MONITORING SYSTEM
507