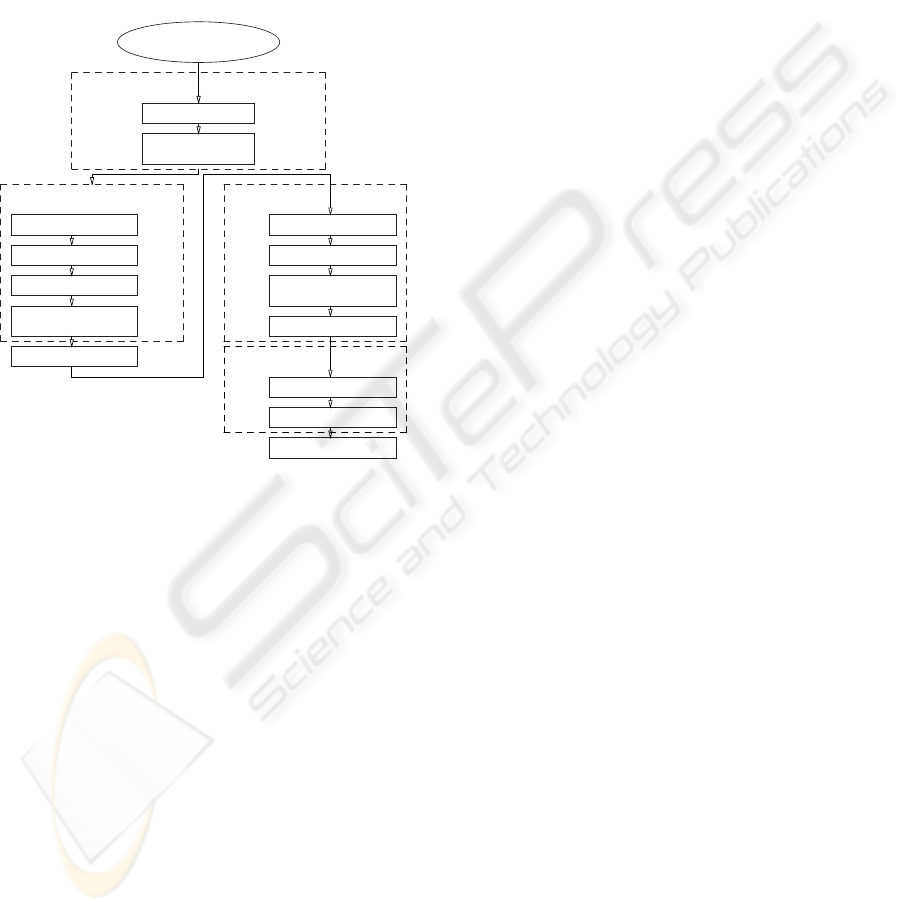
a feature discriminatory that can facilitate both the
weld region and defects segmentation. Finally, fea-
tures obtained are input pattern to artificial neural net-
work (ANN). Previously, principal component anal-
ysis (PCA) is first used to perform simultaneously
a dimensional reduction and redundancy elimination.
Secondly, an ANN is employed for the welding fault
identification task where three regularisation process
are employed in order to obtain a better generalisa-
tion.
Noise reduction
Contrast
enhacement
Preprocessing
Weld segmentation
Labelling
Weld region
Feature extraction
segmentation
ROI
Defect segmentation
Labelling
Defect
segmentation
Feature extraction
ANN
PCA
Regularization
Radiographic Image
Results
Thresholding Otsu Thresholding Otsu
Figure 1: Procedure for the automatic welding defect detec-
tion system.
After digitising the films (Zscherpel, 2000;
Zscherpel, 2002), it is common practice to adopt a
preprocessing stage for the images with the specific
purpose of reducing/eliminating noise and improving
contrast. Two preprocessing steps were carried out
in this work: in the first step, for reducing/eliminating
noise an adaptiveWiener filter (Lim, 1990) and Gaus-
sian low-pass filter were applied, while for adjusting
the image intensity values to a specified range to con-
trast stretch, contrast enhancement was applied in the
second step.
The last stage is the feature extraction in terms of
individual and overall charcateristics of the hetereo-
geneities. The output of this stage is a description of
each defect candidate in the image. This represents a
great reduction in image information from the origi-
nal input image and ensures that the subsequent clas-
sification of defect type and cataloguing of the degree
of acceptance are efficient. In the present work, fea-
tures describing the shape, size, location and intensity
information of defect candidates were extracted.
The dimension of the input feature vector of defect
candidates is large, but the components of the vectors
can be highly correlated and redundant. It is useful in
this situation to reduce the dimension of the input fea-
ture vectors. An effective procedure for performing
this operation is principal component analysis. This
technique has three effects: it orthogonalises the com-
ponents of the input vectors (so that they are uncorre-
lated with each other), it orders the resulting orthogo-
nal components (principal components) so that those
with the largest variation come first, and it eliminates
those components that contribute the least to the vari-
ation in the data set.
3 MULTI-LAYER
FEED-FORWARD ANN
A multiply-input neuron model is shown on the left
in Figure 2. The topology of the network used in this
work is illustrated on the right in Figure 2. Nonlin-
ear pattern classifiers were implemented using ANNs
of the supervised type using the error backpropaga-
tion algorithm and two layers, one hidden layer (S
1
neurons) using hyperbolic tangent sigmoid transfer
function and one output layer(S
2
= 5 neurons) using
a linear transfer function. In this work, a BFGS algo-
rithm (Dennis and Schnabel, 1983) was used to train
the network. The algorithm requires more computa-
tion in each iteration and more storage than the con-
jugate gradient methods, although it generally con-
verges in fewer iterations. The approximate Hessian
must be stored, and its dimension is n × n, where n
is equal to the number of weights and biases in the
network, therefore for smaller networks can be an ef-
ficient training function.
One of the problems that occur during neural net-
work training is called overfitting. The error on the
training set is driven to a very small value, but when
new data is presented to the network the error is large.
The network has memorised the training examples,
but it has not learned to generalise to new situations.
In this work, three methods was used in order to im-
prove generalisation. The first method for improving
generalisation is called regularisation with modified
performance function. This involves modifying the
performance function, which is normally chosen to
be the sum of squares of the network errors on the
training set. The second method automatically sets
the regularisation parameters. It is desirable to deter-
mine the optimal regularisation parameters in an au-
tomated fashion. One approach to this process is the
Bayesian regularisation (MacKay, 1992) (Foresee and
Hagan, 1997). The third method for improving gener-
AN AUTOMATIC WELDING DEFECTS CLASSIFIER SYSTEM
261