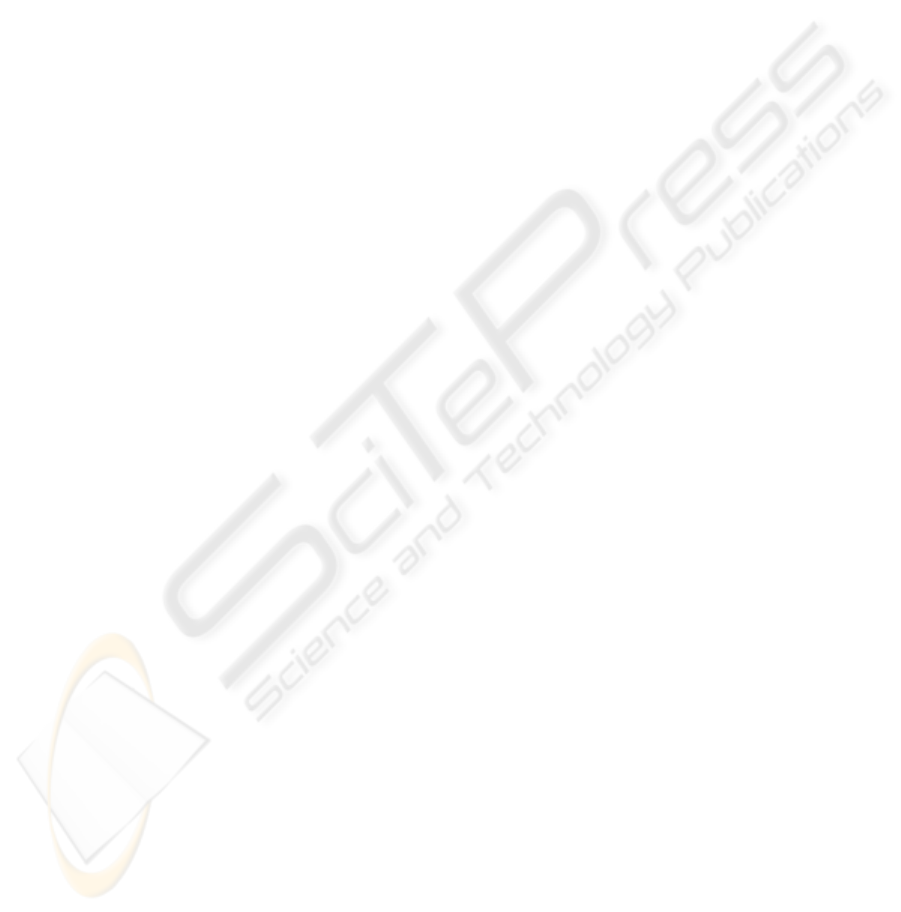
allow the patients to perform more complex ADL
tasks. Note that this current hand device is being
used with C5 quadriplegic patients to complete their
ADL tasks such as picking up bottle etc. (Broadened
Horizons). We are also aware that a PUMA 560
robotic manipulator might not be ideal for
rehabilitation applications. However the use of
safety mechanisms, both in hardware (e.g.,
emergency button, quick arm release mechanism
etc.) and in software (e.g., within the design of the
high-level controller) will minimize the scope of
injuries. Note that the proposed control architecture
is not specific to the presented assistive devices but
can also be integrated with other assistive devices.
We believe that such a robot-assisted
rehabilitation system with capabilities of
coordination of both arm and hand movement is
likely to combine the advantages of robot-assisted
rehabilitation systems with the task-oriented therapy.
In this paper, the efficacy of the proposed intelligent
controller is demonstrated with healthy human
subject. We are aware that a stroke patient with a
spastic arm is much more different from a healthy
subject following the robotic moves. In that respect,
more functional assistive devices and their
corresponding low-level controllers can be
integrated inside the proposed intelligent controller
to allow stroke patients to take part in task-oriented
therapy. As a future work, it is possible to use
intelligent robot-assisted rehabilitation systems in
clinical trials to understand on how impairment
changes carryover of gained functional abilities to
real living environments and how robot-assisted
environments influence these changes.
ACKNOWLEDGEMENTS
We gratefully acknowledge the help of Dr. Thomas
E. Groomes and Sheila Davy of Vanderbilt
University's Stallworth Rehabilitation Hospital for
their feedback about task design and Mark Felling
who is C5 quadriplegic patient for his feedback
about the hand assistive device.
REFERENCES
Ada, L., Canning, C. G., Carr, J. H., Kilbreath, S. L. &
Shepherd, R. B. (1994). Task-specific training of
reaching and manipulation. In Insights into Reach to
Grasp movement, 105, 239-265.
Broadened Horizons, http://www.broadenedhorizons.com/
Cauraugh J. H., Summers, J.J. (2005). Neural plasticity
and bilateral movements: A rehabilitation approach for
chronic stroke. Prog Neurobiol., 75, 309-320.
Erol, D. & Sarkar, N. (2007), Design and Implementation
of an Assistive Controller for Rehabilitation Robotic
Systems. Inter. J. of Adv. Rob. Sys, 4(3), 271-278.
Immersion Corporation, http://www.immersion.com/.
Jack, D., Boian, R., Merians, A. S., Tremaine, M., Burdea,
G. C., Adamovich, S. V., Recce, M. & Poizner, H.
(2001). Virtual reality-enhanced stroke rehabilitation.
IEEE Transactions on Neural Systems and
Rehabilitation Engineering, 9, 308–318.
Jeannerod, M., (1981). ‘Intersegmental coordination
during reaching at natural visual objects’. In
Attention and performance IX, J. L. a. A. Baddeley,
Ed. New Jersey, (pp. 153-168).
Kahn, L. E., Zygman, M. L., Rymer, W. Z. &
Reinkensmeyer, D. J. (2006). Robot-assisted reaching
exercise promotes arm movement recovery in chronic
hemiparetic stroke: a randomized controlled pilot
study. J. Neuroengineering Rehabil, 3,1-13.
Kline, T., Kamper, D. & Schmit, B. (2005). Control
system for pneumatically controlled glove to assist in
grasp activities. IEEE 9th International Conference on
Rehabilitation Robotics, pp. 78 - 81.
Krebs, H. I., Ferraro, M., Buerger, S. P., Newbery, M. J.,
Makiyama, A., Sandmann, M., Lynch, D., Volpe, B.
T. & Hogan, N. (2004). Rehabilitation robotics: pilot
trial of a spatial extension for MIT-Manus. J
Neuroengineering Rehabil, 1, 1-15.
Koutsoukos, X. D., Antsaklis, P. J., Stiver, J. A. &
Lemmon, M.D. (2000). Supervisory control of hybrid
systems. IEEE on Special Issue on Hybrid Systems:
Theory and Applications, 88, 1026-1049.
Matchar D. B., Duncan, P. W. (1994). Cost of Stroke,
Stroke Clin. Updates. 5, 9-12.
Murphy, M. A., Sunnerhagen, K. S., Johnels, B. & Willen,
C. (2006). Three-dimensional kinematic motion
analysis of a daily activity drinking from a glass: a
pilot study. J. Neuroengineering Rehabil., 16, 3-18.
Loureiro, R., Amirabdollahian, F., Topping, M., Driessen,
B. & Harwin, W. (2003). ‘Upper limb mediated stroke
therapy - GENTLE/s approach. Autonomous Robots,
15, 35-51.
Lum, P. S., Burgar, C. G., Van der Loos, H. F. M., Shor,
P. C., Majmundar, M. & Yap, R. (2006). MIME
robotic device for upper-limb neurorehabilitation in
subacute stroke subjects: A follow-up study. J. of
Rehab. Res. & Dev., 43, 631-642.
Takahashi, C. D., Der-Yeghiaian, L., Le, V. H. & Cramer,
S. C. (2005). A robotic device for hand motor therapy
after stroke. IEEE 9th International Conference on
Rehabilitation Robotics, pp. 17 – 20.
Wood, S. R., Murillo, N., Bach-y-Rita, P., Leder, R. S.,
Marks, J. T. & Page, S. J. (2003).Motivating, game-
based stroke rehabilitation: a brief report. Top Stroke
Rehabil, 10, 134-140.
ICINCO 2008 - International Conference on Informatics in Control, Automation and Robotics
12