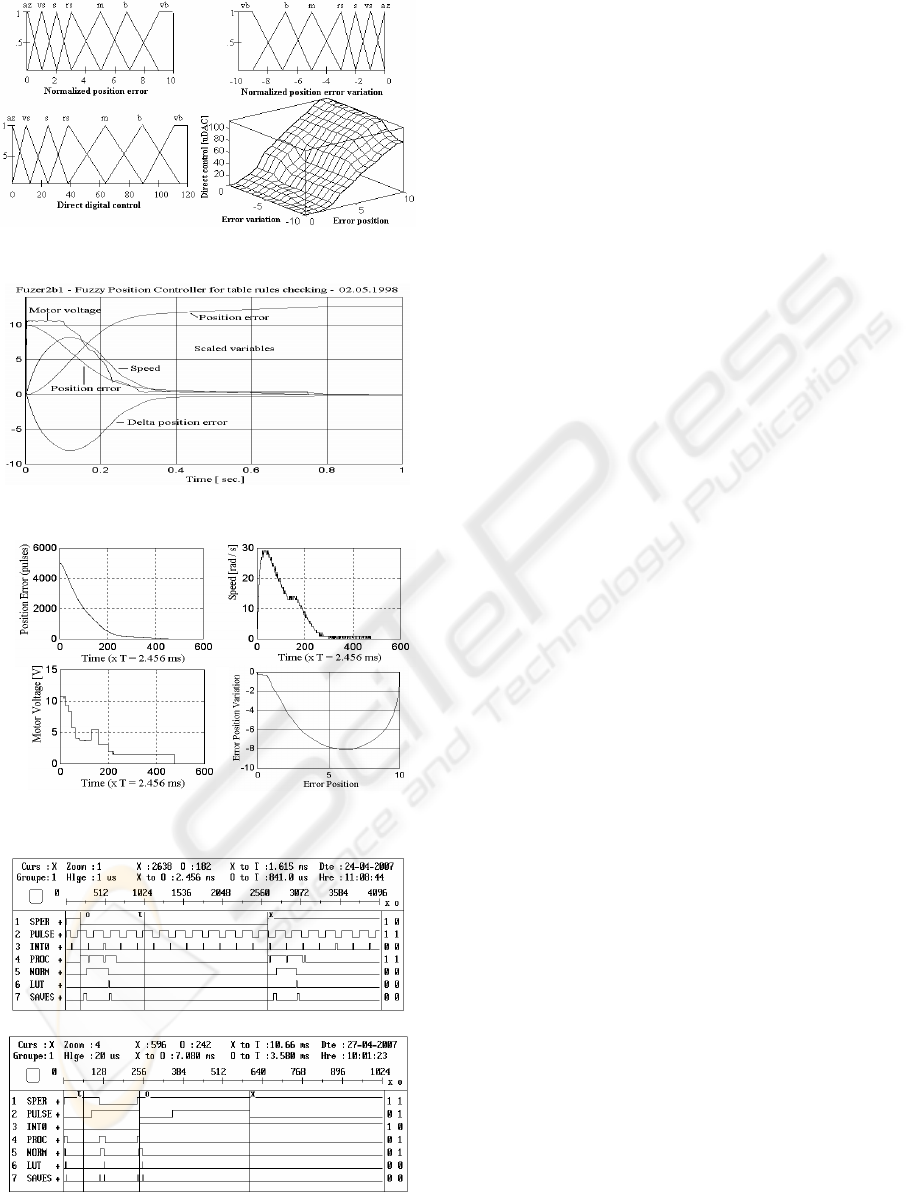
Figure 11: The basic elements for a LUT - FLC.
Figure 12: Results for a FLC in simulation.
Figure 13: On-line results for a LUT based FLC.
a
b
Figure 14: The on-line recordings for a LUT FLC.
on-line results, both for the standard algorithm and
the fuzzy control, are very good in terms of the
macroscopic variables and for the timing revealed by
on-line recordings with a logic analyzer. Some
experiments proved that a good choice for the
sampling control period is not necessarily related
with a high end control processor but is the result for
all correlations previously mentioned.
REFERENCES
Astrom, K.J., Wittenmark, B., 1997. Computer-controlled
systems: theory and design, Prentice Hall, USA.
Coleman C. P., Godbole D., 1994. A Comparison of
Robustness: Fuzzy Logic, PID and Sliding Mode
Control, Proc. of the American Control Conference,
pp. 1654-1659.
Do Wan, K., Jin Bae, P., Young Hoon, J., 2007. Effective
digital implementation of fuzzy control systems based
on approximate discrete-time models, Automatica
(IFAC Jour.), Volume 43 , Issue 10, pp. 1671-1683.
Ibbini, M.S., Jafar, A.S., 2002. Self-Tuning Fuzzy Logic
Controller for a Series DC Motor, Proc. (369) Power
and Energy Systems, Acta Press.
Kozek, M., Lorenz, A., Kampas, Ph., 2007. Modeling and
control of an electric servo drive with strong
restrictions in the control variable, Int. Journal of
Applied Electromagnetics and Mechanics, Vol. 25,
Number 1-4, pp. 521 – 527.
Mihai, D., Constantinescu C., 1999. Fuzzy Versus
Standard Digital Control for a Precise Positioning
System with Low-Cost Microcontroller, PCIM99,
Nurnberg, Proceedings, pp. 249-255.
Mihai, D., 2004. Systèmes d’entraînements électriques I.
Problèmes fondamentaux. Systèmes avec moteurs à
courant continu, Ed. Universitaria, Craiova.
Mihai, D., 2006a. Additional Mathematical Pre-processing
for the Fuzzy Control of a Servodrive, WSEAS Trans.
on Circuits and Systems, Is. 11, Vol. 5, pp. 1575-1580.
Mihai, D., 2006b. An Optimized Fuzzy Control Algorithm
for Servodrives. Some Real-Time Experiments.
Proceedings, IS ’06, London, paper 1-4244-0195-
X/06-CD ROM, pp. 192-197.
Mrozek, B, Mrozek, Z., 2000. Modelling and Fuzzy
Control of DC Drive, ESM 2000, Ghent, pp186-190.
Silveira, P. E., Souza, J.R., Biazotto R. de, V. M., 2002.
Speed Control of an Autonomous Mobile Robot:
Comparison between a PID Control and a Control
Using Fuzzy Logic, J. Braz. Soc. Mech. Sci., vol.24,
no.2, pp.127-129.
Vas, P., 1999. Artificial-Intelligence-Based Electrical
Machines and Drives, Oxford University Press.
*** Technosoft S. A., 1997, MCK 240 DSP Motion
Control Kit. User Manual, Switzerland.
ON THE SAMPLING PERIOD IN STANDARD AND FUZZY CONTROL ALGORITHMS FOR SERVODRIVES - A
Multicriterial Design and a Timing Strategy for Constant Sampling
77