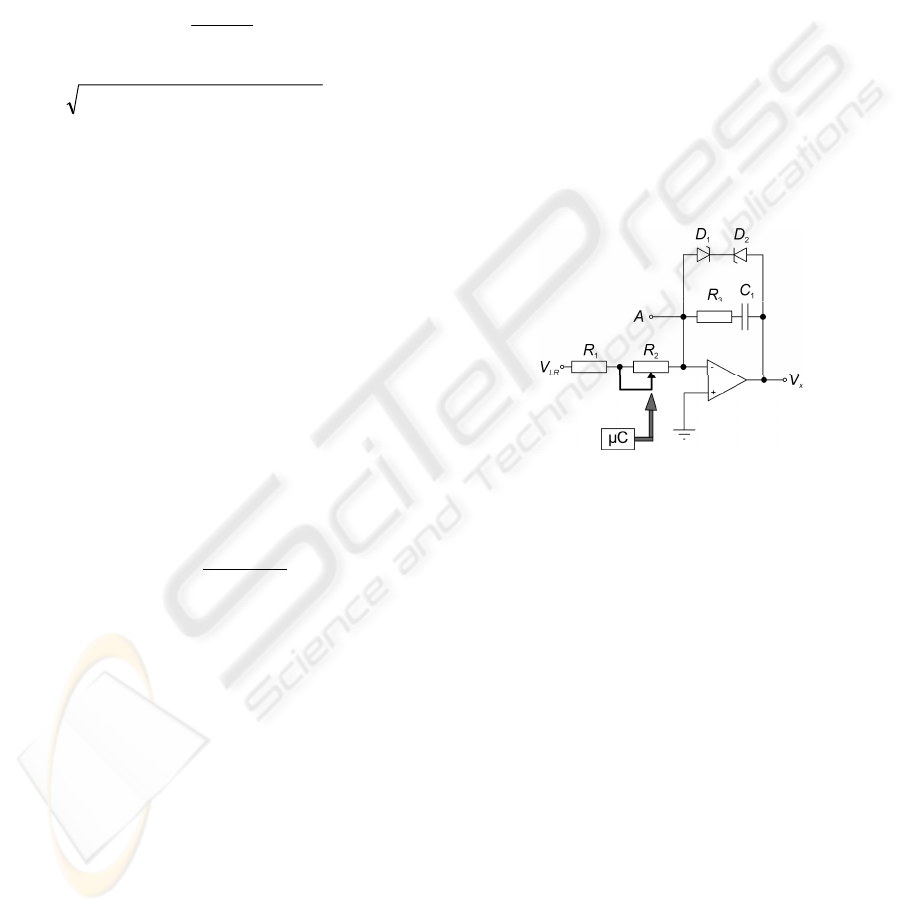
nusoidal signal with a frequency ω
0
is proposed. So,
a subsequent band-pass filter with the center fre-
quency ω
0
suppresses the disturbance signal intro-
duced by the reflector. To estimate the distance z
rad
the amplitude of u(t) is compared with the amplitude
v
1
(t) and so |H
1
(iω)| is calculated. With the experi-
mentally obtained relationship for K
D
in (15), z
rad
is
calculated in (16). The proportional value m has a
value of 45.13 V
-1
m
-1
.
x
Sum
D
K
Vm
K
⋅
⋅
=
4
(15)
))2(1(
4
0
42
0
222
ωω
RRrad
TTAAz +−−= (16)
)1(/
2
0
222
0
22
ωω
RSumRR
TmVKATA +−
with
|)(|
01
iHA = .
To obtain an appropriate value for the amplitude
of the signal u(t) the beam deviation y
x
(t) from the
center of the quadrant diode is analyzed. The devia-
tion should be smaller than a quarter of the beam
diameter to guarantee the interferometer function.
During distance estimation the deviation y
x
(t) is a
superposition of the lateral movement of the reflec-
tor z
lat,x
(t) and the introduced signal u(t). Therefore,
the amplitude of the signal u(t) is chosen to be only
10% of the maximal deflection so that the maximal
velocity v
lat
is not reduced. With the transfer func-
tion H
2
(s) and a maximal amplitude y
x,max
of y
x
(t) the
amplitude u
0
is calculated in (17).
|)(|
02
max,0
ω
iH
K
yu
D
x
⋅=
(17)
Because z
rad
is located in the denominator of (17)
its increase leads to a decreasing amplitude u
0
. Ac-
cording to the described limit of 10%, y
x,max
is set to
R/20 with R being the radius of the beam.
5 PRACTICAL
CONSIDERATIONS
The feedback controller is implemented in an analog
design. To generate the signal u(t), to measure the
signal v
1
(t) and to adapt the gain of the controller, a
microcontroller is used. The microcontroller is an
ATmega128 and is programmed in C. The variable
gain control is realized by digital potentiometers that
are set by the microcontroller. Figure 12 shows the
used circuit for one axis. The digital potentiometer
R
2
offers 127 linearly arranged steps. The resistance
can be adjusted between 1 kΩ and 50 kΩ.
The analog PI controller is built with standard
components without complex serial or parallel circi-
uts resulting in a time constant of T
R
= 132 µs and a
adjustable gain between K
R
= 6.00·10
-3
… 300·10
-3
.
The parameter T
R
remains constant even if the po-
tentiometers change their value. Because of the dis-
crete potentiometer positions there is an error be-
tween the optimal controller gain and the achieved
controller gain. There are only integer positions n
int
available. To obtain an optimal value for K
R
the
theoretical real number n
real
for the potentiometer
position is calculated. Afterwards, n
real
is rounded
down and up and the lower and the upper controller
gains K
l
and K
u
are calculated. The controller gain
with the minimal error in regard to the optimal value
is chosen.
Figure 12: Microcontroller controlling a digital potenti-
ometer and analog PI controller exemplarily shown for the
x-axis.
After power up sequence and beam loss during
operation, the laser beam searches the reflector in a
defined area. This is done by deflecting the mirrors
of the actuator without opening the feedback loop.
The influence of the analog part is reduced and only
the digital part controls the mirror deflection.
Figure 13 shows the operation principle. The
digital potentiometer is set to its maximal value. So,
the influence of the sensor signal to the input of the
PI controller is weak. This is comparable to an open-
ing of the feedback loop and the signal can be cross
talked easily.
The microcontroller introduces a signal at the in-
put of the PI controller. At the same time the re-
duced sensor signal of the diode acts as a distur-
bance variable. The output of the controller is digi-
talized and is compared to the set up variable w
α
.
The microcontroller multiplies the gain K
µ
with the
deviation e. So, the plant with integrating behavior is
controlled via a P controller which is a good combi-
DESIGN OF AN ANALOG-DIGITAL PI CONTROLLER WITH GAIN SCHEDULING FOR LASER TRACKER
SYSTEMS
11