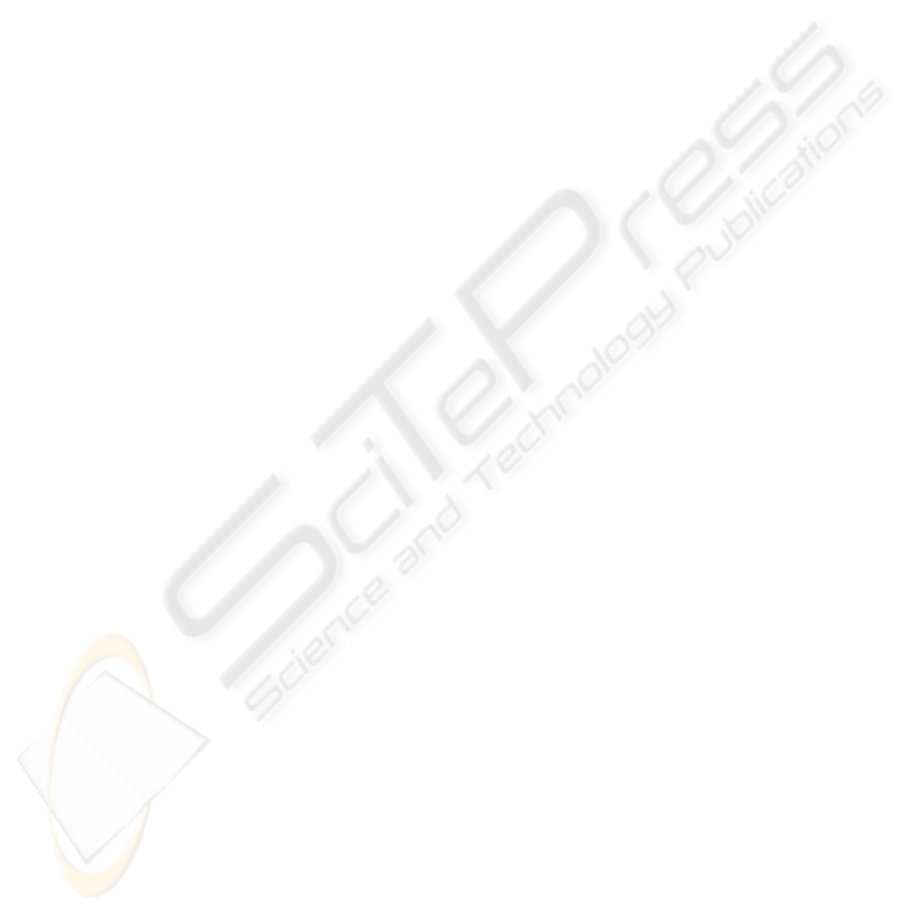
CONTRIBUTION CONCERNING ROBOT ACCURACY USING
NUMERICAL MODELING
Daniela Ghelase
1
, Luiza Daschievici
1
and Irina Ghelase
2
1
“Dunarea de Jos” University, Str. Domneasca, Nr. 47, Galati, Romania
2
Politehnica University, Bucharest, Romania
Keywords: Robot accuracy, numerical modelling, computer simulation, rigidity of gearing.
Abstract: The kinematical accuracy of robot is very important. It is induced by the rigidity of each mechanism of the
robot. The paper presents a numerical method to evaluate the rigidity of worm-gearing teeth. The software,
including setting-up and graphic display, could be adopted of any kind of cylindrical worm-gear drive or for
spur gear drives and bevel gear drives, mechanisms which are in the robot structure. Besides, we can
determine geometrical parameters of the gear drives which influence the increase of accuracy of robot
linkages.
1 INTRODUCTION
Into the kinematical chain there are worm-gear
drives, screw-nut mechanisms and pinion-rack
drives. During the working, these gear drives and
mechanisms of the robot deform under the load,
leading to the motion errors. The errors can not be
entirely eliminated, but their maximum values must
be limited. The theoretical advantage of the
conjugate action in involute gears is lost due to the
deflection of the teeth under load and due to the
manufacturing and assembling errors. These factors
produce instantaneous variations in the gear ratio.
As it is well-known, the rigidity of the meshing
teeth changes as the contact point moves from the
initial point of contact to the final point of contact.
During the meshing the normal force is mobile on
the tooth flank, it changes continuously the position
with respect to the fixing zone of the teeth. The load
is unevenly distributed, depending on the contact
ratio. Consequently, all these factors causes rotative
speed variations of the driven shaft, vibrations,
shocks, noise, power loss, low durability of gears.
The purpose of the present work is to develop a
methodology to evaluate the rigidity of the worm-
gearing tooth. By means of this methodology the
performances of the robot mechanisms may be
improved.
2 GEOMETRY OF THE
WORM-GEARING TOOTH
In order to analyze the rigidity of the worm-gearing
tooth we assume that the spatial gearing consists of
more plane-gearings (pinion-rack drives), that in fact
are cross sections perpendicular to worm-gear axis
(Figure 1). The analytic solving of the problem, even
for a ruled worm-gearing, is very difficult due to the
complexity of the equations of the plane-gearing
profiles that are involved in the enveloping.
Consequently, we use the “minimum distance
method” applied in the case of the “discrete
representation” of the enveloping profiles. Thus, the
enveloping profile of the elementary worm-gear
(plane-gear) can be determined numerically by
knowing “discretely” a matrix having as elements
the coordinates of the worm axial section and by
using the theorem of the “minimum distance
method”.
The minimum distance theorem in “discrete
way” states (Ghelase, D., Daschievici, L., 2006):
The envelope to the family of curves, represented
in “discrete way” as massive of the coordinates of
the points belonging to the family curves, consists of
the all points there are on these curves, for which, at
a certain size of the increment ϕ
1
, the distance at the
meshing pole is minimum.
24
Ghelase D., Daschievici L. and Ghelase I. (2008).
CONTRIBUTION CONCERNING ROBOT ACCURACY USING NUMERICAL MODELING.
In Proceedings of the Fifth International Conference on Informatics in Control, Automation and Robotics - RA, pages 24-29
DOI: 10.5220/0001478800240029
Copyright
c
SciTePress