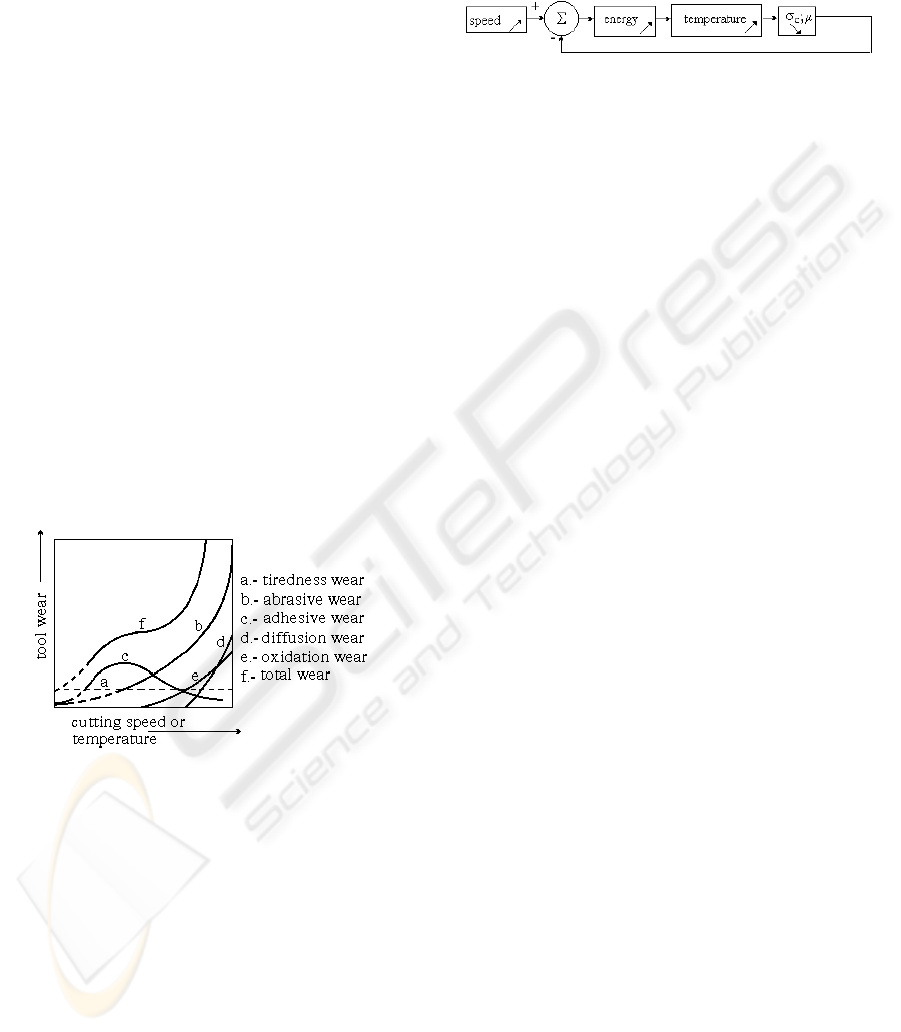
determination of real thermal status, non-stationary
and non-uniformly distributed, that, in time, leads to
a stationary and non-uniformly distributed thermal
status, depending on the influencing factors, the
most important of them being as follows:
- the cutting process parameters;
- the physical and mechanical properties of the
tool blade and splinter;
- the environmental heat exchange;
- the feed-back interdependence between
different influencing factors;
- the cutting process dynamic phenomena.
Cutting wear comes up because of interfering factors
effects and it is important to be known, especially
regarding the cutting tool.
Tool wear is progressive and it manifests under
many aspects (temperature increasing, processed
area deterioration, cutting forces increasing), finally
leading to their stop functioning.
The researches highlighted more blade wear
types, as shown in figure 3 that represents these
wear influences and makes possible an appreciation
of their weight as part of total wear. The diagram
shows that the abrasive wear has the highest
influence; it is determined by the friction conditions
of areas in contact: tool - processed part-splinter.
Figure 3: The influences of partial wear on total wear.
The splinter temperature increases due to the energy
exclusively obtained from friction: the friction
between the splinter and the tool and the friction
between inter- and intracrystals that comes up during
splinter formation and separation. The higher the
temperature the more plastic is the splinter, some of
its areas pass to the liquid phase, the intensity of the
above mentioned frictions decreases, smaller
amounts of energy are freed, splinter temperature
decreases, the splinter is more solid, more intense
frictions develop tending to increase the
temperature, and so on. Therefore, a combination of
effects with opposite tendencies takes place leading
to a splinter temperature, which is not equal to the
melting temperature of the processed part, but an
equilibrium temperature beyond the melting one.
Speed increasing, especially for high cutting speed,
leads to a feedback chain, according to figure 4.
Figure 4: The feedback influence of temperature
increasing on the mechanical characteristics of the
processed material.
According to this chain, cutting speed increasing
leads to cutting area temperatures increasing, the
effect is a deformation resistance and mechanical
work decreasing, thus implying wear reducing and a
higher tool durability.
The analysis of cutting conditions influence on
the tool temperature and tool wear leads to the
conclusion that the variation of wear medium
intensity is very similar to the variation of the
temperature on the tool.
The main objective of the present paper is to
combine in a single model the dynamic, thermal and
tribologic phenomena, in order to evaluate in
advance the wear intensity and to find out the way to
influence it.
2 THE RESEARCH
METHODOLOGY AND THE
UTILIZED MANNERS
Among the considered objectives, there can be
mentioned:
- the research of dynamic phenomena;
- the research of thermal and wear phenomena.
It was necessary to develop a physical model of the
phenomenon in order to perform the researches; in
fact, the phenomenon is a conventional image of the
real status, representing the basics of mathematical
modelling. The model has mathematical equations,
functionally describing the physical model, and
through it, the real phenomenon. For mathematical
model solving, difficult to be analytically solved,
there have been used numerical methods to obtain
solutions for the differential equations (Tomulescu,
2000).
The stages covered for phenomenon modelling
are, as follows:
- cutting area forces modelling, based on
Merchant model for free orthogonal cutting, where
is taken into consideration the fact that the splinter is
MATHEMATICAL MODELLING OF THERMAL AREA IN CUTTING TOOL
277