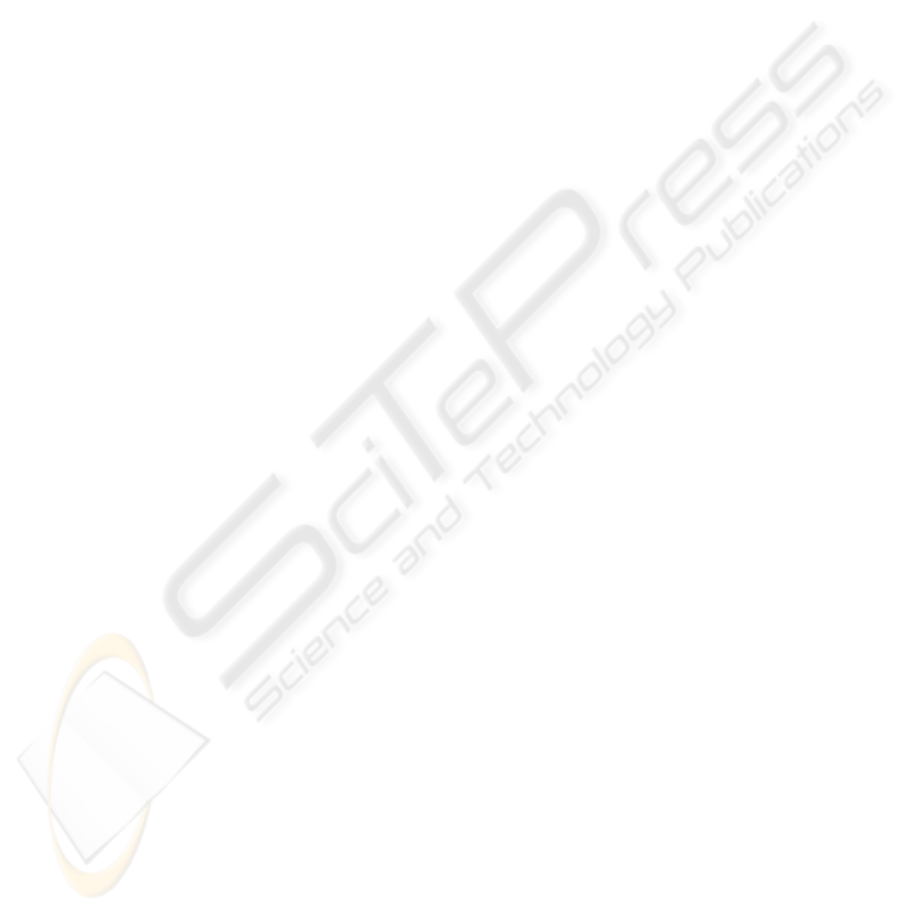
Technologies like JAVA or .NET are available to
program the appropriate user interface. The
graphical user interface (GUI) of such a device is
shown within a web-browser window independent
from the computer platform. The respective program
instructions (e.g. JAVA Applet) for the visualisation
and control are stored in this scenario in the
measurement device. In addition to this, user
manuals, service instructions or electronical data
sheets are available inside the device and accessible
by means of Ethernet protocols (e.g. ftp). The
challenge of implementing this method lies in the
appropriate hardware and software design of
measurement device.
3 SYSTEM ARCHITECTURE
In contrast to the traditional measurement device
visualisation, the development of additional PC-
Programs for control and visualisation could be
avoided if we are using the Ethernet technology. As
mentioned, the required human machine interface is
implemented by means of applets which are stored
in the respective device and are executed within a
web browser. The details of the applets and the
methods used for the implementation should not be
part of this work. The main focus of this paper
concerns the communication aspects of an
embedded web server solution. Using the Ethernet
protocols for the measurement device
communication increases the efforts for the
communication task in the device. This fact has two
consequences. Existing devices are not able to carry
out this additional task because of their limited
resources. New device developments have to
introduce additional hardware which is capable to
execute not only the application program but an
operating system with the Ethernet protocol stack. In
addition to the protocol stack, a files system and a
multitasking support are necessary to support the
desired web-services. Concerning the control aspects
of the measurement device, we have to take care not
to loose the real time aspects. From the economical
point of view we have to consider the side effects of
introducing an operation system (e.g. licences) and
the consequences in terms of additional hardware
(e.g. memory). Never the less a compatible solution
for existing measurement devices is required
additionally. A further aspect lies in the fact that the
introduction of a fast bus connection will not
automatically yield to a higher data acquisition rate.
Typically, existing firmware and protocols limit the
performance of the system. So a appropriate
hardware architecture is necessary to support the
demanded improvements.
Based on a principle which was already
implemented in a density meter (Röhrer, 1991) there
exists a trade off concerning the improvement of the
device communication. If we separate the non real-
time tasks like human machine interface from the
real-time control tasks of a system with the
introduction of two independent execution units (e.g.
computers), we can achieve a solution which
provides a lot of advantages. Using this concept, we
can use even existing small and economical
controller solutions without any modifications to
carry out the real time control task. In contrast to
this, improved communication or human machine
interaction is done by an additional device computer
which communicates with the real time controller on
a proprietary and efficient protocol (e.g. SPI). This
architecture provides the system not only with real
time advantages but also with economical benefits.
4 TEST BED INTEGRATION
Based on the above mentioned considerations the
device integration of measurement devices in an
automotive test-bed automation system should be
shown. An additional computer called EWI is
introduced which works as a gateway between the
traditional RS232 lines of the measurement device
and the Ethernet. Based on this component, a new
integration concept was developed.
4.1 EWI Definition
The main part of the integration concept is a
standalone working EWI (embedded web interface).
According to the different aspects of the
measurement devices (e.g. version, protocol,
hardware, technology), this system offers an overall
and compact solution for a new and standardized
integration concept for measurement devices in
automotive automation systems. The EWI was
development on the basis of a few important
concepts:
- An increase of the data communication rate
- A multi user access from the client systems
- Introduction of a new visualisation concept
The EWI offers different solutions for data
communication and exchange and is implemented as
an additional hardware component. Therefore it is
even applicable for existing devices. The highest
priority is set on the communication between the
different users. As shown in Figure 1, it takes care of
ICINCO 2008 - International Conference on Informatics in Control, Automation and Robotics
96