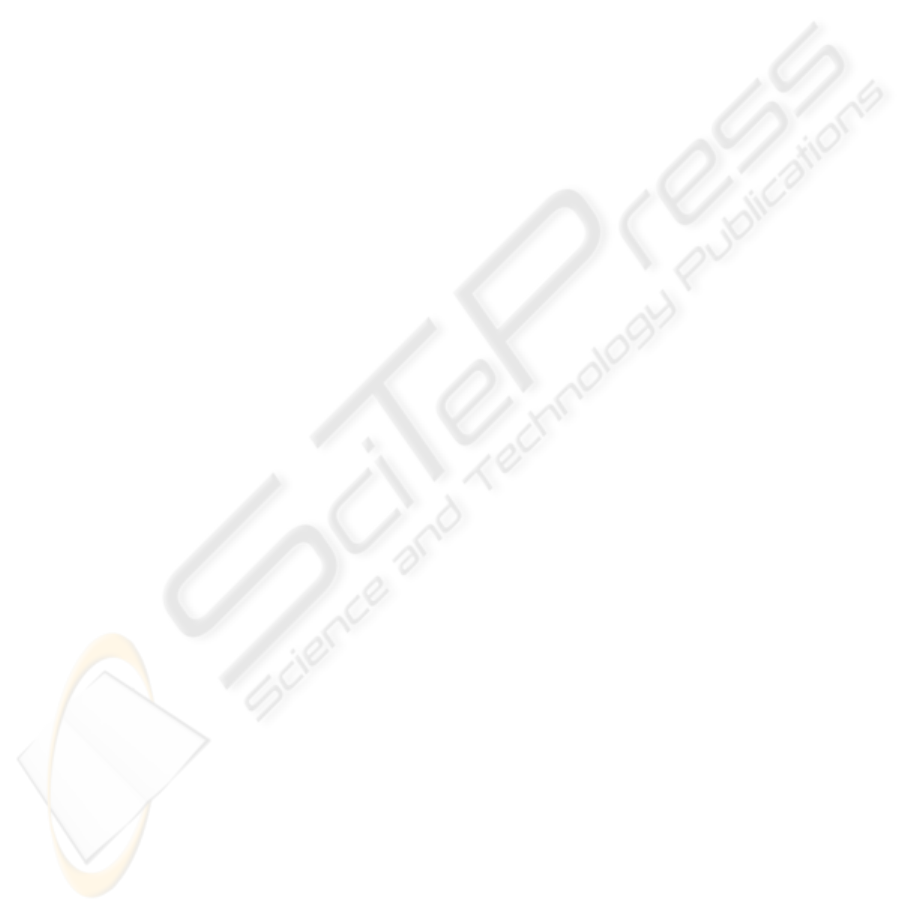
CALIBRATION ASPECTS OF MULTIPLE LINE-SCAN VISION
SYSTEM APPLICATION FOR PLANAR OBJECTS INSPECTION
Andrei Hossu and Daniela Hossu
University Politehnica of Bucharest, Faculty of Control and Computers
Dept. of Automatics and Industrial Informatics, 313 Spl. Independentei, sector 6, RO-77206, Bucharest, Romania
Keywords: Industrial Vision System, Line-Scan Camera, Dual-Camera Vision System, and Moving Scene in Robotic
Automation.
Abstract: The System Set-up Time it is one of the characteristics of an Industrial Vision System, besides the accuracy
performances and response time. Minimizing the set-up time while keeping the performances in accuracy
and in response time is one of the goals of any advanced Vision System. Starting from the purpose and the
required performances of the proposed Industrial Vision System, in the paper is presented a calibration
method developed for a multiple line-scan camera Vision System (in particular for a dual line-scan camera
system). The calibration method presented is based on analyzing the image of a calibration tool exposed to
the Vision System. There are presented the type of dimensional distortions identified from the experimental
results. The second part of the paper presents the calibration method. The Industrial Vision System
described in the paper is designed for silhouette inspection of planar objects located on a moving scene
(transport conveyor), in a robotic handling application (it is a pure 2D Vision System, the volumetric
characteristics of the analyzed objects being not relevant for the application). However the height of the
object is varying in time (from one set of objects to another). Due to the fact the distance between the
cameras and the objects is changing, the measuring results are affected. The proposed calibration method
allows the Vision System to self adjust the calibration parameters for a known change in height of the
objects, without affecting the accuracy system performances. In the final section of the paper are presented
some practical aspects of the proposed calibration method, and the balance between the off-line and the on-
line required computational efforts from the Vision System.
1 MULTI LINE-SCAN CAMERA
VISION SYSTEMS
CHARACTERISTICS
The class of the Artificial Vision Systems dedicated
for analyzing objects located on a moving scenes
(conveyor) presents some specific characteristics
relative to the Artificial Vision Systems dedicated
for static scenes. These characteristics are identified
also on the Image Calibration Process (Borangiu, et
al., 1994)., (
Haralick and Shapiro, 1992).
Figure 1 presents the model of the image
obtained from a dual line-scan camera Vision
System.
For this class of the Artificial Vision Systems we
could identify as relevant for the calibration process
the following characteristics:
- The system is using line-scan cameras for
the image acquisition.
- The system is a dual-camera.
- The obtained image has significant
distortions on (and only on) the image sensors
direction.
- There is an overlapped image area
between the two cameras. The end of the
acquisition line of the 1
st
camera is overlapping
the beginning of the acquisition line of the 2
nd
camera. This overlapping area is significant in
dimension and is a constant parameter resulted
during the artificial vision system installation
process.
- There is a lengthwise conveyor distance
between the acquisition lines of the two
cameras. This distance is also a constant
parameter and its value is fixed during the
system installation process.
36
Hossu A. and Hossu D. (2008).
CALIBRATION ASPECTS OF MULTIPLE LINE-SCAN VISION SYSTEM APPLICATION FOR PLANAR OBJECTS INSPECTION.
In Proceedings of the Fifth International Conference on Informatics in Control, Automation and Robotics - RA, pages 36-40
DOI: 10.5220/0001480300360040
Copyright
c
SciTePress