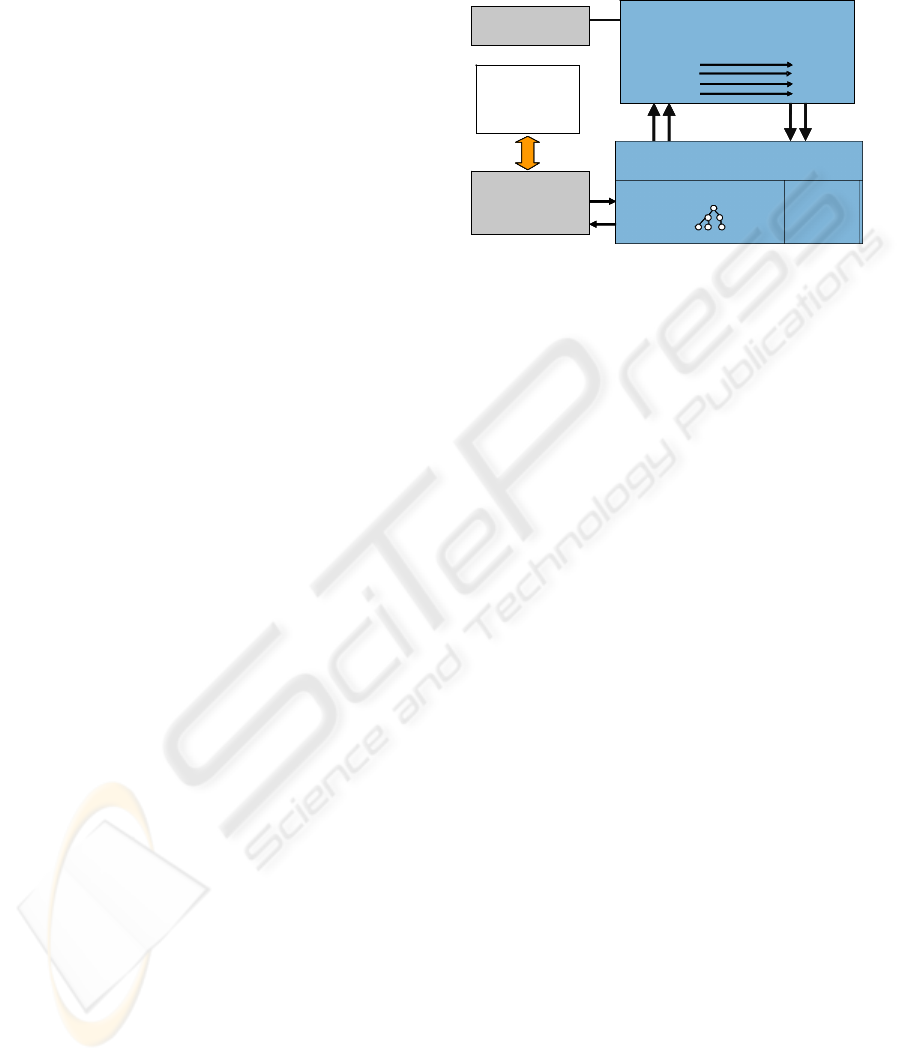
In addition to that the gained information has to be
processed – comprehending knowledge storage,
learning and problem solving. This requires an
explicit knowledge representation within the system
and the possibility to reason about the given
problems. The knowledge has to be stored in an
inferable way that deterministic algorithms can be
used to find possible ways through the problem
space to the desired goal.
For more complex processes the system has to
arrange the different tasks in a useful combination to
accomplish the job. This requires a sophisticated
planning module, which is one of our research
focuses. A coordination module is responsible for
the implementation of the scheduled tasks with the
action module.
Transparency of machine behaviour to a human
user will be one of the crucial aspects of the
cognitive technical system. The system itself and
human operators should be able to comprehend the
decisions the technical system takes and the
subsequent actions it executes. That is necessary to
prevent handling errors by the human operator and
increases the chance to discover and correct
malfunctions. Also the mental models of the
operator and the technical cognitive systems have to
be compatible. This leads to an increasing
acceptance of the system by the human operator
(Hartmann, 1995).
2.2 Cognitive Architectures
A possible approach to fulfil the discussed
requirements is the use of a cognitive architecture. In
1987 Newell defined the Unified Theory of
Cognition (UTC) (Newell, 1990). An approach
conforming to the UTC has to be composed of a set
of mechanisms which accounts for all forms
(processes) of cognition. In robotics and cognitive
science research aimed for developing architectures
sufficient to the UTC. Two popular representatives
are ACT-R (Adaptive Control of Thought—
Rational; Anderson, 2004) and Soar (originally
SOAR - State, Operator And Result; Laird, 2006).
Soar and ACT-R are both rule-based and goal-
oriented architectures, which can be used for
creating artificial intelligence.
The structure of Soar is characterized by
different models of the memory (Figure 4).
Production Rules entered by a user are included in
the long-term memory. With the help of the
perception module, the actual state of the
environment is modelled in the working memory.
Depending on this state and the preference memory
Soar elaborates and fires within a decision cycle
dertermined production rules and modifies entries in
the short-term memory.
long -term memory
(production rules)
short -term memory
working memory
perception
+
action
user
preference
memory
(+, -, >, <)
environment
long -term memory
(production rules)
short -term memory
working memory
perception
+
action
user
-
environmentenvironment
long -term memory
(production rules)
short -term memory
working memory
perception
+
action
user
preference
memory
(+, -, >, <)
environment
long -term memory
(production rules)
short -term memory
working memory
perception
+
action
user
-
environmentenvironment
long -term memory
(production rules)
short -term memory
working memory
perception
+
action
user
preference
memory
(+, -, >, <)
environment
long -term memory
(production rules)
short -term memory
working memory
perception
+
action
user
-
environmentenvironment
Figure 4: Structure of the memory in Soar.
The basic architecture of ACT-R consists of a set of
modules for processing different forms of
information (Anderson, 2004). In comparison to
Soar, ACT-R differs between declarative and
procedural knowledge. The basic idea of modelling
cognitive abilities like learning and problem solving
by using production rules is similar to the Soar
architecture. However, the functional aspects of the
different modules are deduced from psychological
theories. Since ACT-R is a theory focussing on
modelling human cognition, it also simulates
inefficient human behaviour which is not consistent
with industrial applications. Thus, there is only a
minor presence of the theory in the field of robotics
or automation so far.
Unlike more specialized approaches in cognitive
science and robotics, Soar and ACT-R provide a
generic concept for developing artificial intelligence.
We studied the two architectures in the face of their
pros and cons for their use in production
environments by examining criterias like
persistence, expandability and autonomy.
Soar is a suitable approach for modelling
cognitive systems for production environments. It
provides a wide field of the required capabilities like
learning, planning and problem solving within a
complex production rule system. However, our
research so far has shown that not all components of
Soar are adequate for a production environment.
Due to complexity of the application area, the real
time capability of Soar-architectures decreases with
the higher amount of knowledge stored in the
procedural memory, provoked by an increase in
possible matches for the reasoning algorithm
(Doorenbos, 1995). This is a common problem of
deliberative rule-based architectures. Architectures
which are used for mobile robots claiming improved
ICINCO 2008 - International Conference on Informatics in Control, Automation and Robotics
110