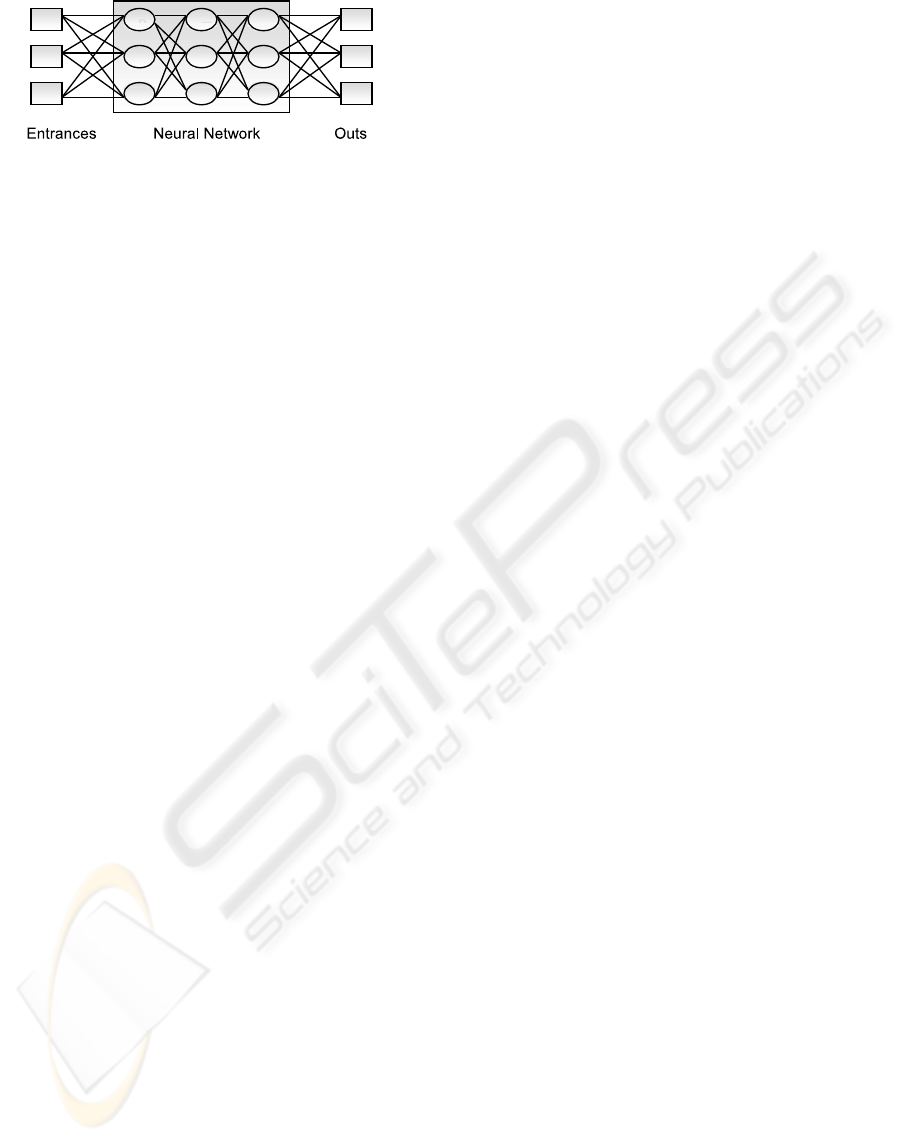
Figure 1: Basic model of a neuronal network.
For applications that demand networks with fewer
than 100 neurons and little training, the software im-
plementations are sufficient. When the problem re-
quires over 100 neurons and 10000 synapses, is nec-
essary to use hardware.
3 DEVELOPMENT
- Design of neuronal network
- Method
- Network training
- Operation
3.1 Design of the Neuronal Network
The variables of the system are:
• pH: This variable is very important because the
alga survives within a range of pH between 8.5
and 10.5. pH can be measured with a pH meter.
If the pH is low, then a valve connected with a
little tank, is open to give a bicarbonate sodium
solution. If it is high, another valve gives CO2 to
a dome on the surface aquaculture.
• Temperature: Spirulina Platensis can tolerate tem-
peratures between 13
◦
to 33
◦
C. If the tempera-
ture rises over the top limit a fan is connected and
the windows open. If the temperature is low, the
windows are closed (the aquaculture is in a green-
house).
• Flow density: The density of the flow is directly
related to salinity and conductivity. Thus, it can be
controlled by the regulation of the doses of clean
water, marine salt, nitrate and sodium bicarbonate
supplied to the culture. The maximum and mini-
mal density values are 1.05 and 1.20 g/cm
3
• Population density: When the Spirulina popula-
tion reaches a maximum density, this may result
in sudden death. The optimum time for collection
(harvest) is therefore before maximum density is
reached, at a density of 900 mg/l. Density was
measured with a laser device (Ponce, 2001). At
800 mg/l a pump is connected and the harvest be-
gins.
In order to train the neural network, the independent
variables were measured and the dependent variable
was forced to a desired value. During the training,
time was used as an additional variable to distribute
the learning into discrete cycles (Hagan and Demuth,
1999).
Independent variables:
- pH
- Temperature
- Flow density (salinity and electrical conductivity)
Dependent variable:
- Population density
After training, the system controlled 4 variables:
- pH
- Temperature
- Flow density (salinity and electrical conductivity).
- Population density
3.2 Method
It has 4 inputs (measured variables), and 4 outputs
- 3 of which variables that must be controlled; the
remaining output is for training the neural network.
The best way to train a neuronal network is by means
of variable forced learning (Guti´errez et al., 2004).
Training consists of producing successive cultures,
each one under different constant conditions, max-
imum and minimum values. Training is completed
when the learning margin error approaches zero. For
a different condition the system will computebetween
the 2 extreme data. Offside these maximum and min-
imal data the control does not work.
The extreme conditions are: pH min= 8.5 ; pH
max = 10.5
Temperature: min = 13
◦
C; max = 33
◦
C
Population density mg/l: min = 100; max = 800
Flow density g/cm
3
: min = 1.05 ; max = 1.20
The best control scheme for this problem is a
NARMA2 network (Norvig and Russell, 2003), a
neuronal controller that transforms nonlinear system
dynamics into linear dynamics by canceling the non-
linearities during training. This optimizes the perfor-
mance of the hardware. A linear system enables faster
training and control in real time for microprocessors.
The control input is computed to force the plant
output to follow a reference signal. The neural net-
work plant model is trained with static back propaga-
tion and is reasonably fast. It requires minimal online
computation (Rio and Molina, 2002).
ICINCO 2008 - International Conference on Informatics in Control, Automation and Robotics
290