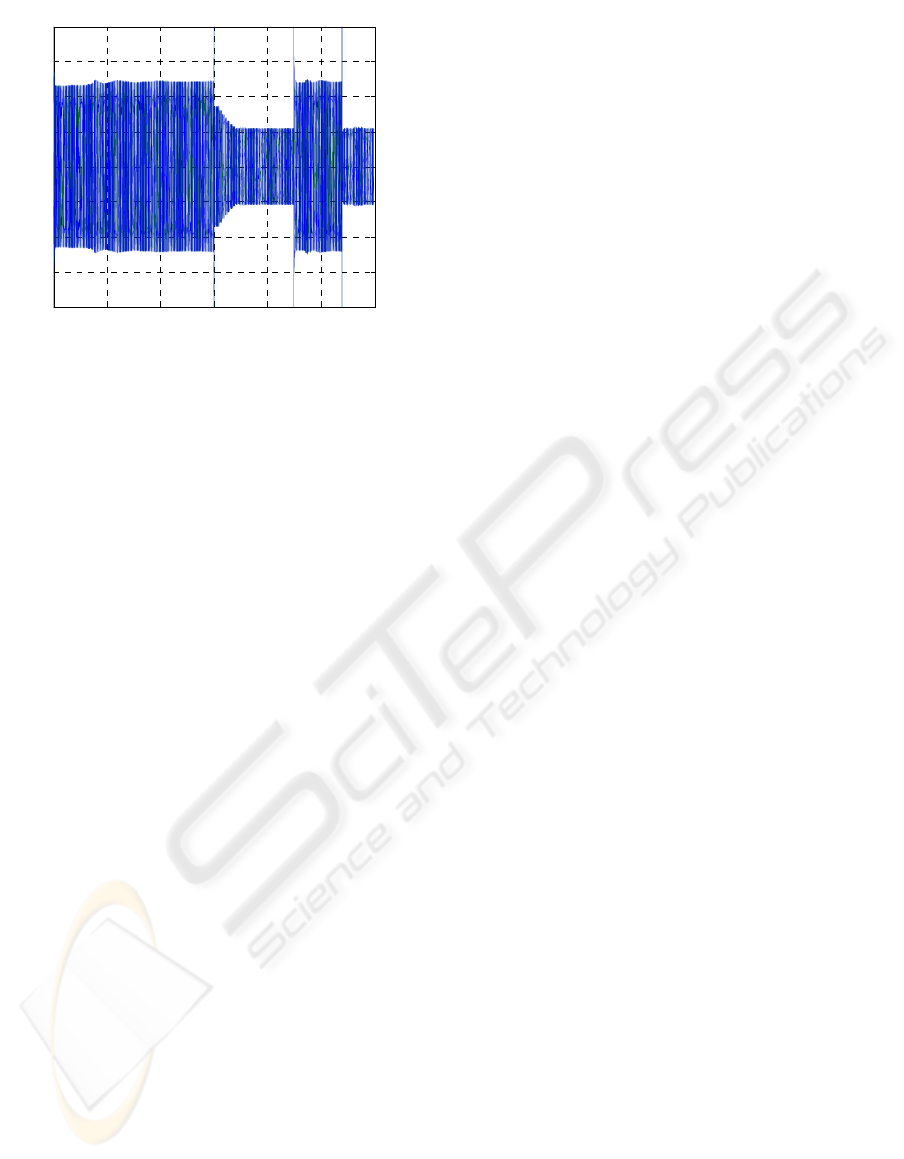
Figure 6: Results of simulation for operation of the fuzzy
controller: A) Reference and actual speed on the axis of
turbine in r.p.m.; B) Components of d-axis current; C)
Components of d-axis current and rotor flux; D)
Components of q-axis current and torque estimate; E) Out
power; F) Voltage in the phases A, B and C; F) Current in
the phases A, B and C.
4 CONCLUSIONS
The proposed control strategy consists of a more
effective way to implement the efficiency
optimization via flux control in an induction
machine. From the analysis of literature can be
observed that in the comparative study of the diverse
known search techniques, none of them results on a
process as fast as the one achieved with the present
method. This implies a great energy save, because
the system can be tuned all the time and operate at
maximum efficiency. Another noteworthy point is
that the transition from steady to transitory state
occurs without abrupt changes in the system, or
without any topological control change, since the
displacement from a low torque point to one of
higher torque or vice-versa is already programmed
in the base of rules. The salient features of this
technique are summarized next: i) It is applicable to
any machine size, and does not require knowledge of
machine parameters; ii) The rule base self tuning is
progressive, and does not need any intervention
from the operator; iii) Once tuned, the system is
capable of operating all the time at optimum
efficiency, without delay from one steady state
condition to another, with significant energy saving;
iv) During transients the rule base is kept active and,
as a consequence there is no switching from one
control strategy (for steady state) to another (during
transients), provided that the tuning has been
completed; v) Proper disturbance compensation is
included, such that no correction is needed to keep
torque and speed constant during the optimization
process; and vi) The system is capable of tracking
slow parameter deviations, guaranteeing true
optimum efficiency.
ACKNOWLEDGEMENTS
The authors wish to acknowledge the support of Fha
– Foundation for the Development of New
Technologies of Hydrogen in Aragón; CIRCE –
Centre of Research for Energy Resources and
Consumption; as well as CEFET-BA and University
of Zaragoza.
REFERENCES
Kumar,Vinod and Joshi, R. R. 2007. Fuzzy Logic Based
Light Load Efficiency Improvement of Matrix
Converter Based Wind Generator System. In Journal
of Theoretical and Applied Information Thecnology,
pp. 79 – 89. JATIT.
Leidhold, Roberto, Garcia, Guillermo and Valla, Maria
Inés. February 2002. Field-Oriented Controller
Induction Generator With Loss Minimization.
Transactions on Industrial Electronics. Vol. 49. No 1
pp. 147-156, February 2002. IEEE.
Sousa, G. C. D. and B. K. Bose, (1995), Fuzzy logic based
on-line efficiency optimization control of an indirect
vector controlled induction motor drive, Transactions
on Industrial Electronics vol. 42 nº 2, pp. 192-198.
IEEE.
Rüncos, F. at alli, Geração de Energia Eólica -
Tecnologias Atuais e Futuras. WEG Jaraguá do Sul.
Brasil. www.weg.com.br. WEG Máquinas S.A.
Simões, Marcelo Godoy, Franceschetti, N. N. and BOSE,
Bimal Kumar. 1999. Otimização de um Sistema de
Geração de Energia Eólica Através de Controle Fuzzy.
SBA Controle & Automação. Vol. No 01, pp. 48-58.
Brasil. Jan., Fev., Mar., Abril de 1999. SBA.
Sousa, G. C. D., Bose, B. K. and J. Cleland, (1992), “Loss
Modeling of Converter Induction Machine System for
Variable Speed Drive”, Proceedings of the IECON’92,
International Conference on Industrial Electronics,
Control and Instrumentation, vol. 1, pp. 114-120.
IECON.
F. Abrahamsen, Fred Blaabjerg,J. K. Pedersen, P. Z.
Grabowski and P. Thogersen, (1998), On the Energy
Optimized Control of Standard and High-Efficiency
Induction Motors in CT and HVAC Applications,
Transactions on Industry Applications, vol. 34, nº 4,
pp. 822-831. IEEE.
F. Abrahamsen, Fred Blaabjerg,J. K. Pedersen, (1996),
State –of-the-Art of optimal Efficiency Control of
Low Cost Induction Motor Drives, Power Electronics
and Motion Control, vol. 2, pp. 163-170. PEMC’96.
0 10 20 30 40 50 60
-20
-15
-10
-5
0
5
10
15
20
t (s)
Current (A)
Ia,Ib and Ic (A)
G )
ICINCO 2008 - International Conference on Informatics in Control, Automation and Robotics
18