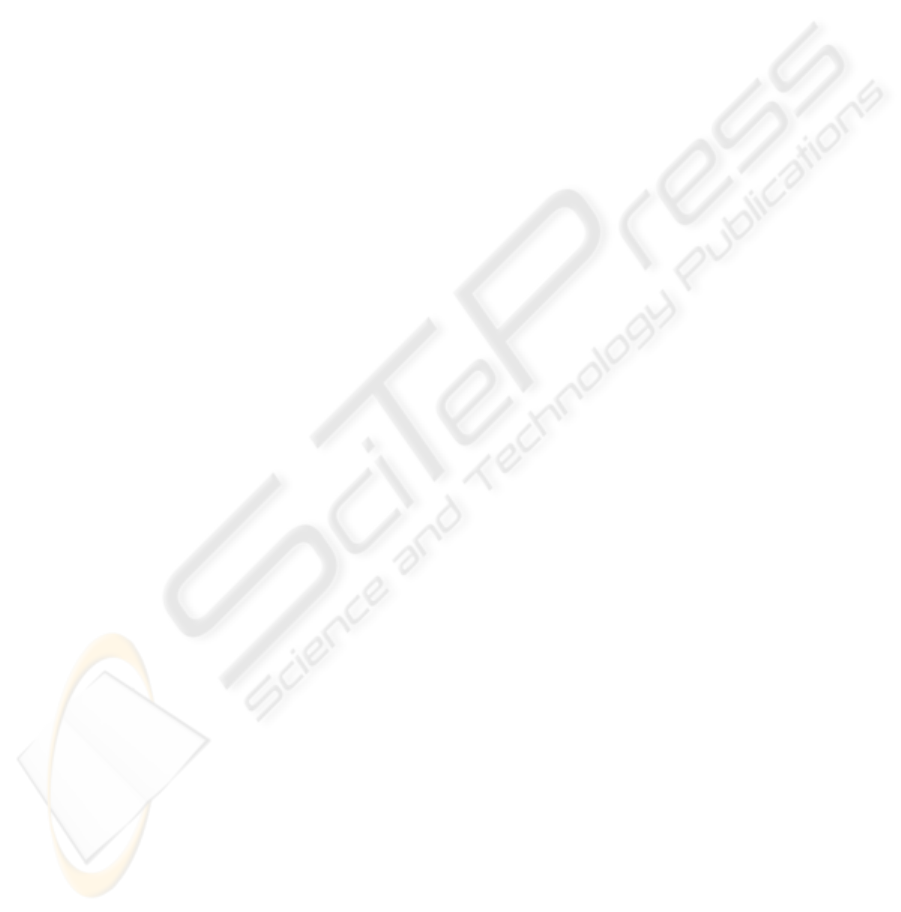
Yang, 2005) and (Jovanov et al., 2001). This is a 16-
bit processor running at 8MHz incorporating 60KB
of flash memory and 2KB of RAM and provides in-
terfacing opportunities via 48 GPIO lines and a 12-bit
ADC. The system developed by Lo and Yang used
ECG sensors, accelerometers, and a temperature sen-
sor to monitor patient health. The system developed
by Jovanov et al., was used for monitoring the elderly
and those undergoing physiotherapy.
Other systems expand upon commercial devices
such as the Mica2 and MicaZ motes developed at the
University of California, Berkeley, or Intel’s Imote
platform. This approach often has a disadvantage in
that the basic platform is generic, and may not di-
rectly provide the facilities required for the specific
BSN project. Such commercial platforms are also
often larger and heavier than custom developed plat-
forms as they are required to be general purpose in
order to achieve any commercial success. The MicaZ
mote uses the Atmega128L, an 8-bit processor run-
ning at 8MHz and featuring 128KB of flash memory
to which an additional 512KB is added externally on
the mote itself. A 10-bit ADC, UART and I2C bus are
also available. (Gao et al., 2005) developed a system
based around the this mote, adding various sensors
and supporting devices to allow patient tagging and
monitoring in an emergency response environment.
(Walker et al., 2006) present a blood pressure mon-
itoring system based on the MicaZ platform. In that
work, a commercial blood pressure monitoring device
is connected to the MicaZ via a serial interface.
2.2 Instrumenting First Responders
The best fit example of a commercial product de-
signed for the purpose of monitoring personnel carry-
ing out missions in dangerous environments is the Vi-
voResponder by (Vivometrics, 2007). VivoResponder
is based upon an earlier product called the LifeShirt
and is aimed at personnel engaged in firefighting
and hazardous materials training or emergency re-
sponse, industrial clean-ups using protective gear, and
biohazard-related occupational work. The VivoRe-
sponder is supplied in three parts: a lightweight, ma-
chine washable chest strap with embedded sensors; a
data receiver; and, VivoCommand software for moni-
toring and data analysis. The sensors embedded in the
chest strap monitor the subject’s breathing rate, heart
rate, activity level, posture, and single point skin tem-
perature.
Monitoring of the subject’s breathing is performed
using a method called inductive plethysmography,
where breathing patterns are monitored by passing a
low voltage electrical current through a series of con-
tact points around the subject’s ribcage and abdomen.
Monitoring of the subject’s heart rate is performed via
an ECG.
The VivoCommand software, provided with the
device, displays the gathered data from the chest strap
in real-time on a remote PC. The parameters are up-
dated every second along with 30-second average
trends. The parameters are displayed with colour cod-
ing intended to allow quick assessment of the status of
up to 25 monitored personnel simultaneously. Base-
line readings can be set individually per monitored
person.
The work developed here differs in intent: the aim
here is to provide a detailed thermal assessment based
on sensors integrated into the protective suit and de-
liver remotely abstracted comfort information.
2.3 Other Work on EOD Suits
Working from a physiological perspective, (Thake
and Price, 2007) have investigated the thermal strain
of a subject when wearing EOD suits in hot envi-
ronments. The work looks at quantifying the level
of strain by assessing how hot and tired the suit
wearer feels whilst wearing various combinations of
suit components. An “activity” regime was developed
for the assessment based on the types of activities that
a bomb disposal technician would undergo during a
mission and included walking on a treadmill, unload-
ing and loading weights from a rucksack, crawling
and searching activity, arm cranking and cognitive
tests. Aspects of hand-eye coordination and psycho-
logical performance were also assessed. The inves-
tigations have demonstrated a large increase in phys-
iological strain when wearing the EOD suit, though
benefits have been shown when the ambient air is
cooled for the suit ventilation purpose and lighter-
weight trousers are worn.
It is indeed these types of studies, together with
the user requests, that prompted the development
of the detailed physiological monitoring system pre-
sented in this paper. The activity regimes described
by Thake and Price were used in the experiments pre-
sented in this paper to allow validation of findings.
3 SYSTEM DESIGN AND
ARCHITECTURE
The main part of the prototype system is designed
following a sense-model-decide-act architecture as
shown in figure 2. The environment within the suit
is sensed in terms of temperature; sensed data is in-
tegrated into a model representing the thermal state
INSTRUMENTING BOMB DISPOSAL SUITS WITH WIRELESS SENSOR NETWORKS
25